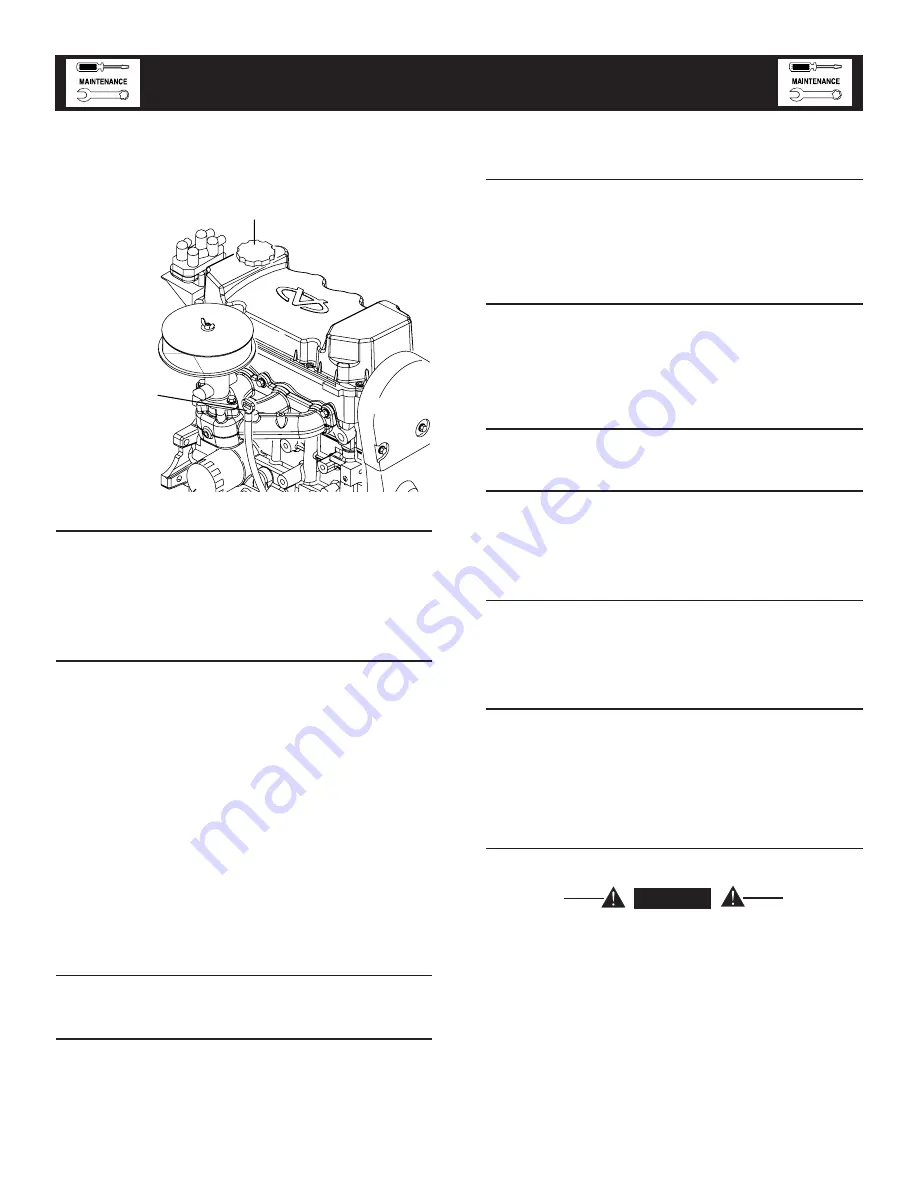
Figure 10.1 - Oil Dipstick and Oil Fill Cap
OIL FILL CAP
OIL
DIPSTICK
BATTERY FLUID
Check battery electrolyte fluid based on the
Maintenance Schedule. Fluid should cover separa-
tors in all battery cells. If fluid level is low, add dis-
tilled water to cover tops of separators. DO NOT USE
TAP WATER IN BATTERY.
ENGINE COOLANT
Check coolant level in coolant recovery bottle. See
Specifications.
Add recommended coolant mixture as necessary.
Periodically remove radiator pressure cap (only
when engine has cooled down) to make sure the
coolant recovery system is functioning properly.
Coolant should be at bottom of radiator filler neck.
If coolant level is low, inspect gasket in radiator
pressure cap. Replace cap, if necessary. To have
pressure cap tested, contact a Service Dealer.
Inspect cooling system and coolant recovery sys-
tem for leaks.
MAINTENANCE OWNER/OPERATOR
CAN PERFORM
CHECK ENGINE OIL LEVEL
Refer to “Checking Fluid Levels”.
CHECK BATTERY
See “Checking Fluid Levels”.
Check battery cables for condition, tightness, cor-
rosion or damage. Clean, tighten or replace as
necessary.
•
•
•
•
EXERCISE SYSTEM
Start the generator engine at least once every seven
days and let it run at least 20 minutes. For more
detailed exercise information, see the respective sec-
tions in the Control Panel Technical Manual that is
supplied with the unit.
INSPECT COOLING SYSTEM
Inspect engine cooling system. See “Maintenance
Schedule”.
Check hoses for damage, deterioration, leaks, etc.
Correct any discrepancies found.
Check hose clamps for tightness.
CHECK ENGINE COOLANT LEVEL
See “Checking Fluid Levels”.
PERFORM VISUAL INSPECTION
Complete a thorough visual inspection of the entire
engine-generator monthly. Look for obvious damage,
loose, missing or corroded nuts, bolts and other fas-
teners. Look for fuel, oil or coolant leaks.
INSPECT EXHAUST SYSTEM
Inspect the exhaust system at least once every three
months. Check all exhaust system pipes, mufflers,
clamps, etc. for condition, tightness, leaks, security,
damage.
CHECK FAN BELT
Inspect fan belts every three months. Replace any
damaged, deteriorated, worn or otherwise defec-
tive belt.
Check fan belt tension. Thumb pressure, exerted
midway between pulleys, should deflect about 3/8
to 5/8 of an inch. Adjust belt tension as required.
INSPECT ENGINE GOVERNOR
Visually inspect electronic governor.
DANGER
Do not attempt to adjust the governor. Only
qualified service facilities should adjust the
governor. Excessively high operating speeds
are dangerous and increase the risk of personal
injury. Low speeds impose a heavy load on the
engine when adequate engine power is not
available and may shorten engine life. Correct
rated frequency and voltage are supplied only
at the proper governed speed. Some connected
electrical load devices may be damaged by incor-
rect frequency and/or voltage. Only qualified
service technicians should adjust the governed
speed.
•
•
•
•
•
Standby Generator Sets
Maintenance
10-2
Maint011 Rev.
D 06/07
Summary of Contents for Guardian 005324-1
Page 24: ...Standby Generator Sets Notes...
Page 25: ...Standby Generator Sets Notes...
Page 26: ...Standby Generator Sets Notes...
Page 27: ...Standby Generator Sets Notes...
Page 28: ......
Page 30: ......
Page 32: ......
Page 34: ......
Page 36: ......
Page 38: ......
Page 40: ......
Page 42: ......
Page 44: ......
Page 46: ......
Page 48: ......
Page 50: ......
Page 51: ......
Page 52: ......
Page 53: ......
Page 54: ......
Page 55: ......
Page 56: ......
Page 57: ......
Page 58: ......
Page 59: ......
Page 60: ......
Page 61: ......
Page 62: ......
Page 63: ......