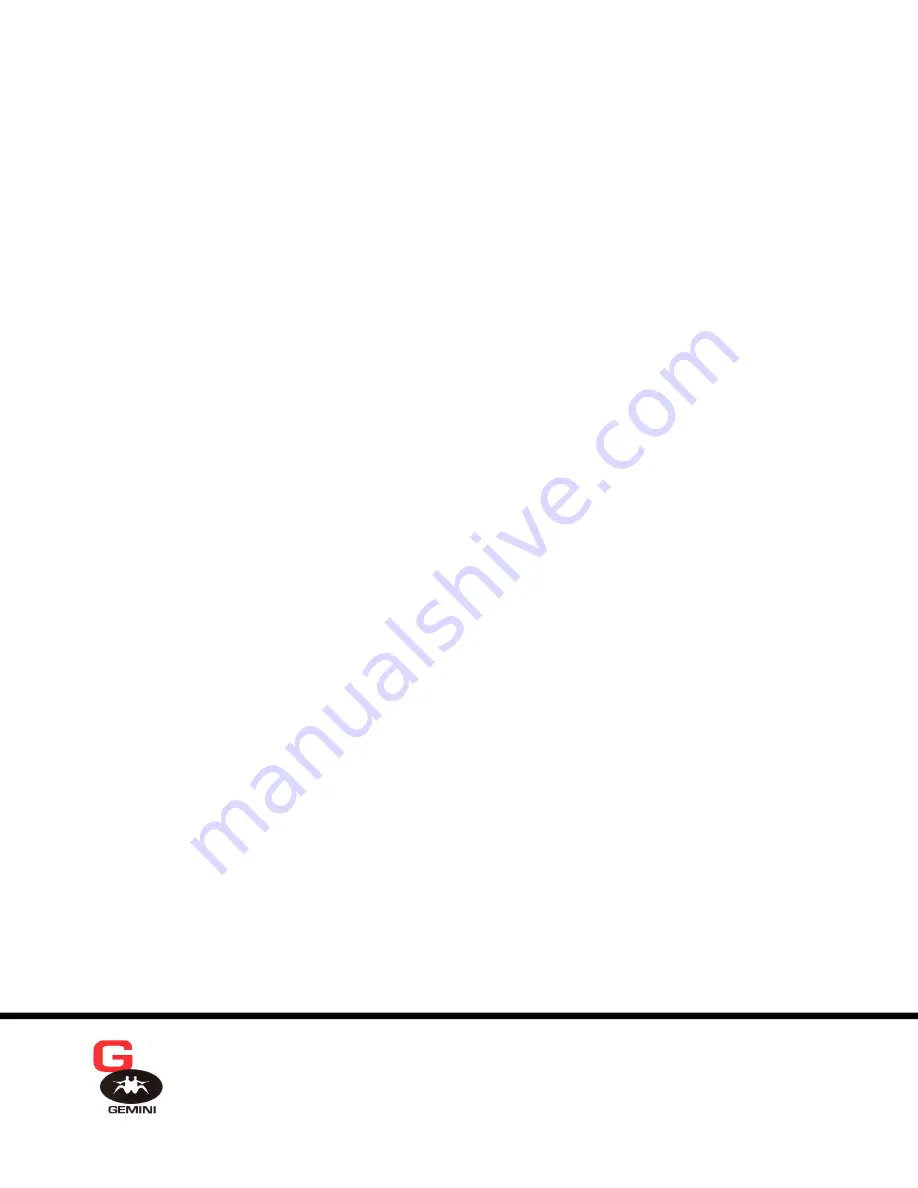
GEMINI CONTROLS LLC
Phone (262) 377-8585
P.O. Box 380 W61 N14280 Taunton Ave.
FAX (262) 377-4920
Cedarburg, WI 53012
Email: [email protected]
www.geminicontrols.com
SETUP FOR TACH FEEDBACK
If tack feedback is used , first setup the drive with armature voltage feedback.
1. Change the jumper on the top board from position “I” to position “H”.
2. Install a jumper on position “A, B, C, D, E, F, or G”, whichever corresponds to the maximum tach voltage at rated
speed.
3. Turn the “IR COMP” pot. fully counterclockwise. Turn the “CL” pot. down to 25%.
4. Apply a 10% speed reference and turn power on, observing the direction of rotation and whether the motor stabilizes at
a low speed or runs away to full speed.
a. If the motor runs away in the desired direction, remove power and reverse the polarity of the tach leads.
b. If the drive runs in the wrong direction, remove power and reverse the polarity of the armature leads.
c. If the drive runs at a low controlled speed, but in the wrong direction, remove power and reverse the polarity of both the
armature and tach leads.
d. If the drive runs at controlled low speed in the proper direction, all connections are correct.
5. Increase the current limit setting “CL” to 50%, and adjust the stability pot. “STAB” for optimum stability while varying
the speed reference.
6. Adjust the maximum speed pot. “MAX SP” for rated motor speed, and repeat step 5.
7. Adjust the current limit “CL” only as high as needed for the application, but not high enough to permit more than 10
amperes DC to the motor, as measured with a DC ammeter in series with the motor.
This completes the drive setup.