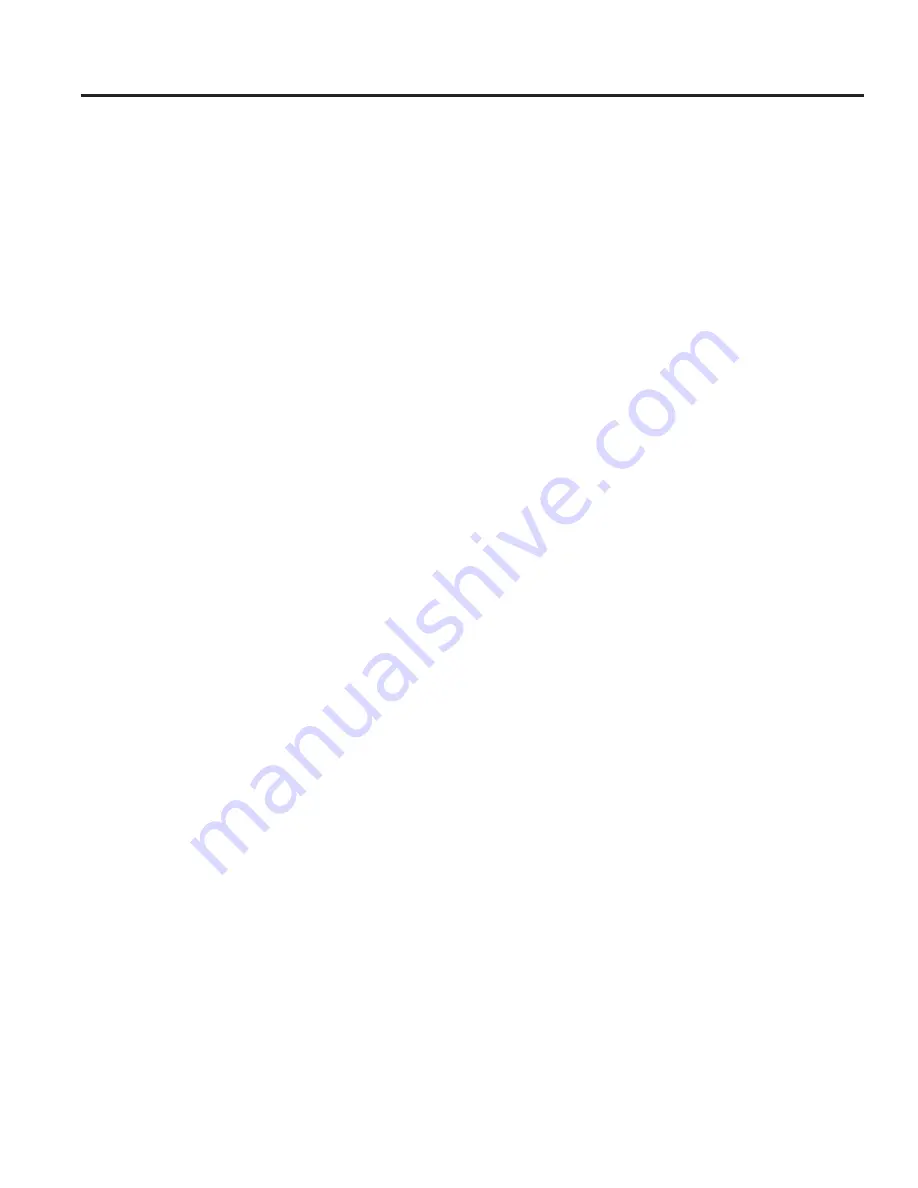
7
Installation Manual
Toll Free: 800-635-0289 • Email: [email protected] • Web: www.ametekfactoryautomation.com
Chapter 3: Connections and Wiring
Once the LDT has been installed, wiring connections can be made. Units are available with Integral cable
assemblies, bare leads or 5 pin M12 (A-Code) connector options. Refer to part numbering on unit in question for
proper wiring. See Appendix A for part numbering grid. See Figure 3-2 for connection options.
Once the LDT has been installed, wiring connections can be made. On units with the M12 connector option it is
recommended to uses an industry standard 5 pin 12mm Euro style cordset with a shield tied to the coupling nut.
On units with our Integral Cable option the shield is tied directly to the LDT’s housing. To reduce electrical noise
the shield must be properly used. Connect the cable’s shield to the controller system Ground. Always observe
proper grounding techniques and isolate high voltage (i.e. 120/240VAC) from low voltage (i.e. 24 VDC cables).
Warning: Do not use molded cordsets with LEDs!
It is preferable that the cable between the LDT and the interface device be one continuous run. If you are using a
junction box, it is recommended that the splice junction box be free of AC and/or DC transient-producing lines. The
shield should be carried through the splice and terminated at the interface device end.
NOTE:
When grounding the LDT, a single earth ground should be connected to the Power Supply Common (circuit
ground). The LDT Power Supply Common should be connected to the Power Supply Common (-) terminal. The LDT
power supply (+VDC) should be connected to the power supply positive terminal (+). The LDT cable shield should
be tied to earth ground at the power supply. The LDT analog common should not be connected to earth ground
and should be used for connection to interface devices only.
The 958A offers up to 16-Bits of resolution, and is fully programmable over the entire active stroke length. Keep in
mind that there is a 1.18” Null Zone at the connector end of the LDT and a 2.49” Dead Band at the other end of the
LDT that the magnet must stay out of at all times. The units come fully programmed from the factory and do not
require re-programming unless desired.
The analog output is referenced to the analog common terminal and should not be referenced to any of the other
common terminals. For wiring, see Figure 3-1. For programming Zero and Span, See Section 3.4.
3.1: Wiring
Figure 3-1 shows two common methods for wiring the 958A to a customer supplied interface device, such as a PLC
or motion controller. The two different methods are commonly referred to as Single Ended Input and Differential
Input. Differential Input is the preferred wiring method.
With the Differential Input, the Analog Common wire is connected to the customer supplied input device and
the Power Supply Common is wired separately to the customers supplied power source. When wired using the
Differential method, the electrical noise and voltage offset errors produced by the currents running through the
Power Supply Common are eliminated. The Power Supply Common and Analog Common are internally connected
inside of the 958A LDT.