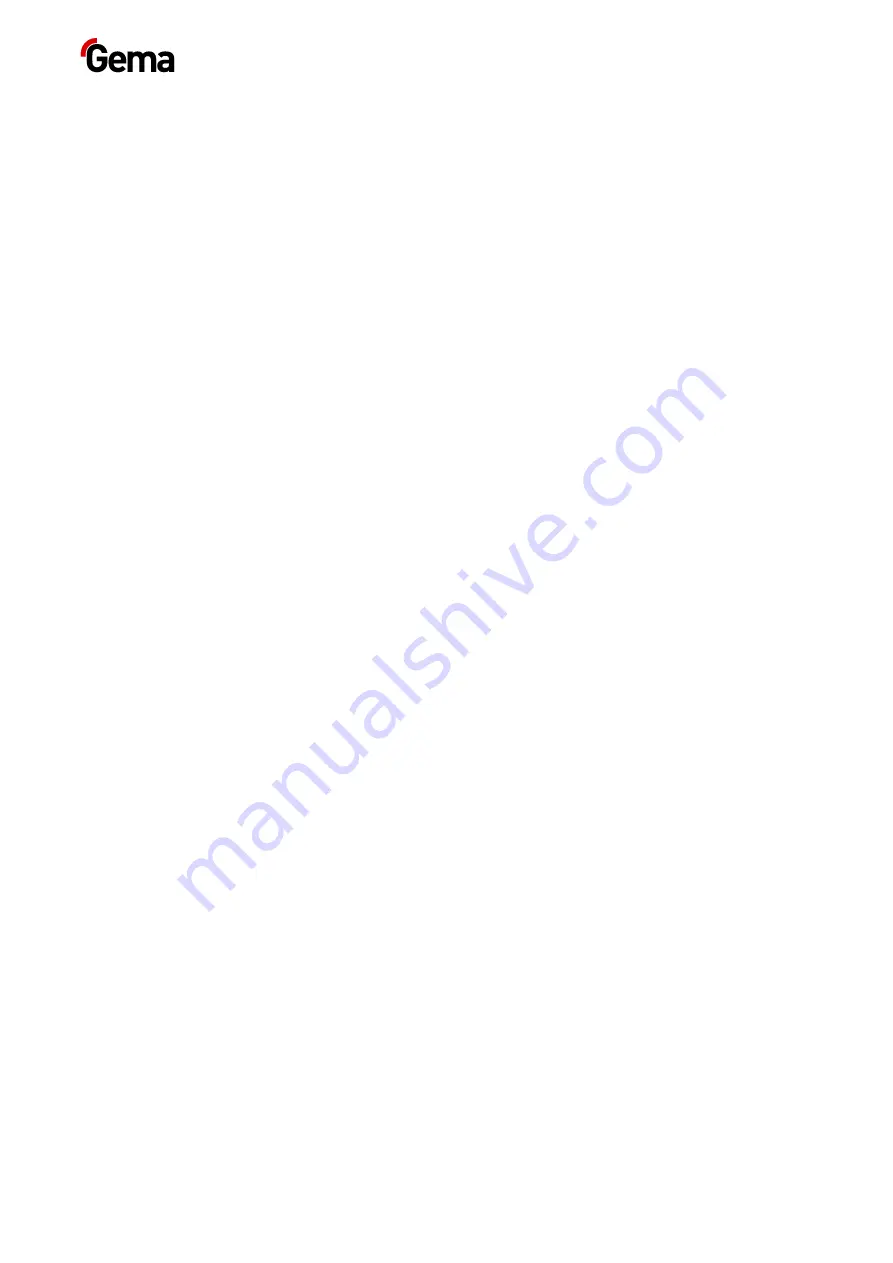
Rev. 00 03/19
Documentation OptiFlex Pro B
© Copyright 2019 Gema Switzerland GmbH
All rights reserved.
This publication is protected by copyright. Unauthorized copying is
prohibited by law. No part of this publication may be reproduced,
photocopied, translated, stored on a retrieval system or transmitted in any
form or by any means for any purpose, neither as a whole nor partially,
without the express written consent of Gema Switzerland GmbH.
Gema, EquiFlow, MagicCompact, MagicCylinder, OptiCenter, OptiFlex,
OptiGun, OptiSelect and OptiStar are registered trademarks of Gema
Switzerland GmbH.
ClassicLine, ClassicStandard, ClassicOpen, DVC (Digital Valve Control),
GemaConnect, MagicControl, MagicPlus, MonoCyclone, MRS,
MultiColor, MultiStar, OptiAir, OptiControl, OptiColor, OptiFeed, OptiFlow,
OptiHopper, OptiMove, OptiSieve, OptiSpeeder, OptiSpray, PCC (Precise
Charge Control), RobotGun, SIT (Smart Inline Technology) und
SuperCorona are trademarks of Gema Switzerland GmbH.
All other product names are trademarks or registered trademarks of their
respective holders.
Reference is made in this manual to different trademarks or registered
trademarks. Such references do not mean that the manufacturers
concerned approve of or are bound in any form by this manual. We have
endeavored to retain the preferred spelling of the trademarks, and
registered trademarks of the copyright holders.
To the best of our knowledge and belief, the information contained in this
publication was correct and valid on the date of publication. Gema
Switzerland GmbH makes no representations or warranties with respect
to the contents or use of this publication, and reserves the right to revise
this publication and make changes to its content without prior notice.
For the latest information about Gema products, visit
www.gemapowdercoating.com.
For patent information, see www.gemapowdercoating.com/patents or
www.gemapowdercoating.us/patents.
Printed in Switzerland
Gema Switzerland GmbH
Mövenstrasse 17
9015 St.Gallen
Switzerland
Phone
:
+41-71-313 83 00
Fax.: +41-71-313 83 83
E-mail: [email protected]
Summary of Contents for OptiFlex Pro B
Page 12: ...Rev 00 03 19 12 Safety OptiFlex Pro B ...
Page 34: ...Rev 00 03 19 34 Operation OptiFlex Pro B ...
Page 36: ...Rev 00 03 19 36 Decommissioning Storage OptiFlex Pro B ...
Page 50: ...Rev 00 03 19 50 Fault clearance OptiFlex Pro B ...
Page 54: ...Rev 00 03 19 54 OptiSelect Pro GM04 OptiFlex Pro B ...
Page 62: ...Rev 00 03 19 62 Maintenance Repairs OptiFlex Pro B ...
Page 64: ...Rev 00 03 19 64 Fault clearance OptiFlex Pro B ...
Page 67: ...Rev 00 03 19 OptiFlex Pro B Spare parts list 67 OptiFlex Pro B Spare parts fig 17 ...
Page 75: ...Rev 00 03 19 OptiFlex Pro B Spare parts list 75 Inside back plate fig 23 OptiStar CG21 ...
Page 77: ...Rev 00 03 19 OptiFlex Pro B Spare parts list 77 Connecting material fig 24 ...
Page 88: ...Rev 00 03 19 88 Spare parts list OptiFlex Pro B OptiFlow IG07 spare parts fig 28 ...
Page 90: ...Rev 00 ...