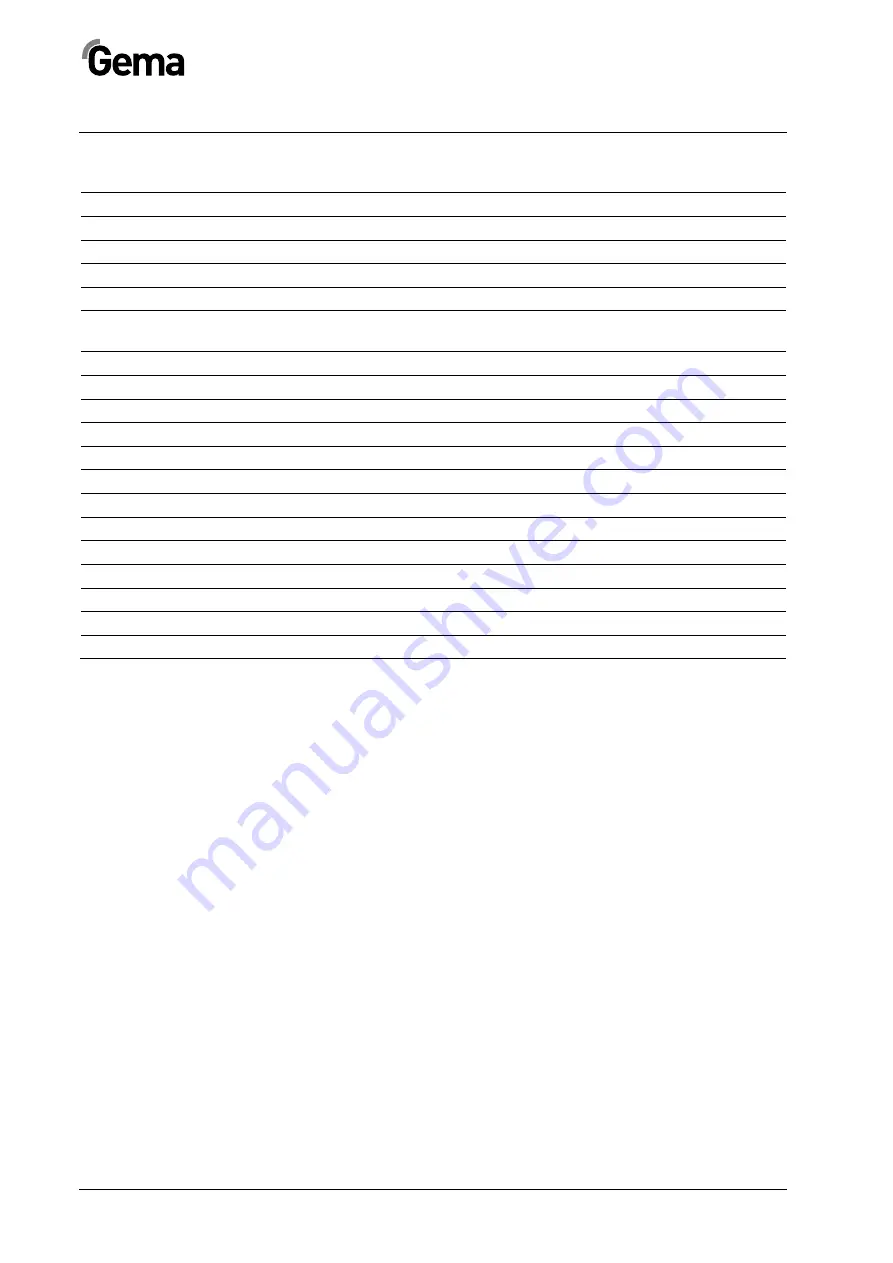
V 03/13
32
•
Spare parts list
OptiFlex 2 V
OptiFlex 2 V fresh powder system – Spare parts list
3
IG06 injector – complete (see corresponding user manual)
1007 780
4
Pneumatic connection for conveying air – complete (incl. Pos. 4.1, 4.2, 4.3)
4.1
Quick release connection – NW5, Ø 8 mm, red
261 645
4.2
Nut with kink protection – M12x1 mm, Ø 8 mm
201 316
4.3
Plastic tube – Ø 8/6 mm, red
103 500*
5
Pneumatic connection for supplementary air – complete (incl. Pos. 5.1, 5.2 and
5.3)
5.1
Quick release connection – NW5, Ø 8 mm, black
261 637
5.2
Nut with kink protection – M12x1 mm, Ø 8 mm
201 316
5.3
Plastic tube – Ø 8/6 mm, black
1008 038*
8
Fluidizing/suction unit – complete
1007 509
9
Pneumatic connection for Fluidizing air – complete (incl. pos. 9.1, 9.2 and 9.3)
9.1
Quick release connection – NW5, Ø 6 mm
200 840
9.2
Nut with kink protection – M10x1 mm, Ø 6 mm
201 308
9.3
Plastic tube – Ø 6/4 mm, black
1001 973
12
Rubber damper – Ø 20x25 mm, M6/2 mm
246 000
13
Hexagon shakeproof nut – M6
244 430
14
Powder hose – Ø 15/10 mm, 6 m
1001 673*#
15
Short description
1007 143
16
Operating manual
*
Please indicate length
#
Wearing part
Summary of Contents for OptiFlex 2 V
Page 12: ......
Page 18: ......
Page 22: ......
Page 26: ...V 03 13 24 Initial start up OptiFlex 2 V 11 12 13 14 15 16 17 18 19 20 21 ...
Page 28: ......
Page 32: ......
Page 36: ...V 03 13 ...