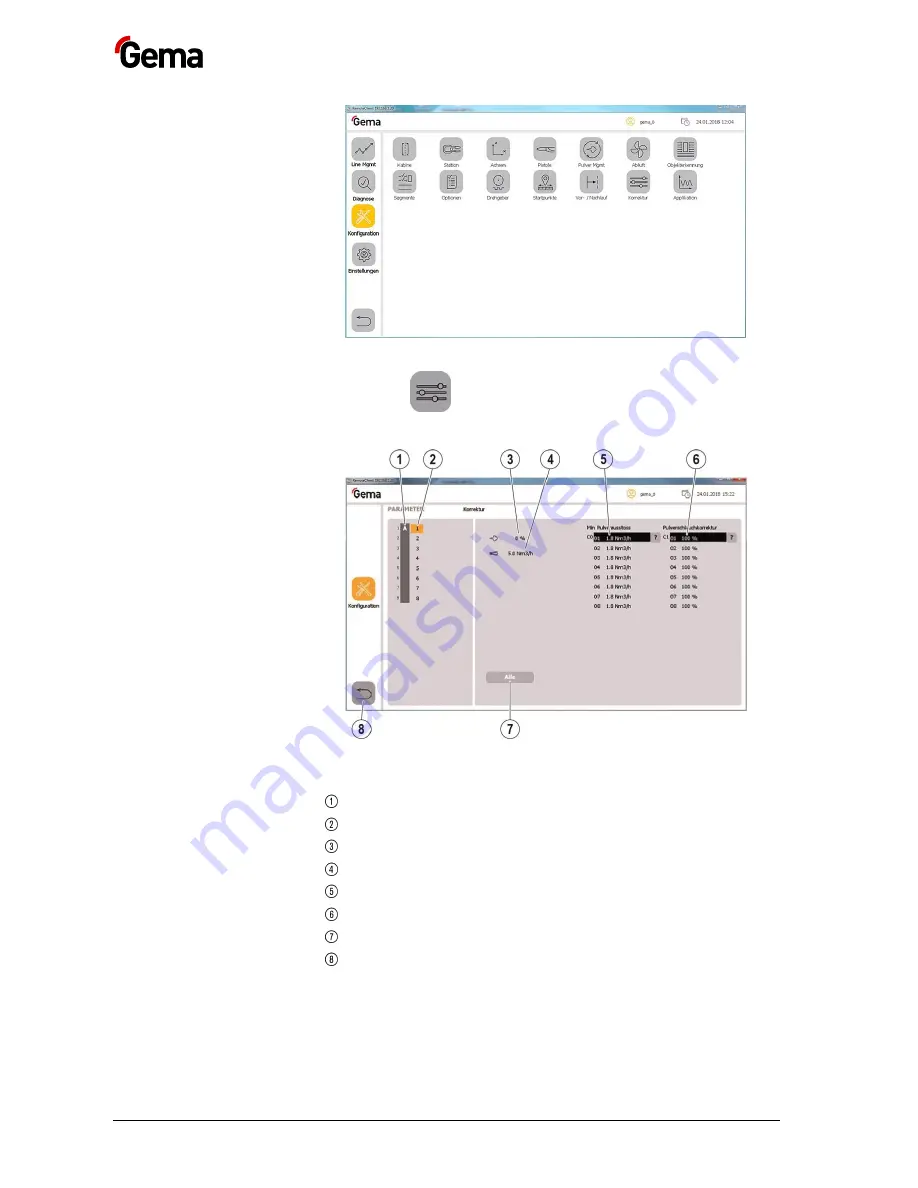
Rev. 00 08/17
68
Maintenance / Repairs
MagicControl 4.0 (CM40)
Fig. 67:
3.
Press the
key
The following page is displayed:
Fig. 68: Powder output/powder hose correction
Station
Gun (
activated
/deactivated)
Powder output
Total air
Minimum powder output
Powder hose correction
Changes per gun or all guns at the same time
Exit current page
4.
Set the total air to
4.0
(Nm³/h) on the
(4)
display. Set the powder
output to
0
(%) on the
(3)
display
5.
Check the correction value for minimum powder output
C0
on the
(5)
display, and set it to
1.8
(Nm³/h) if necessary
Summary of Contents for MagicControl 4.0
Page 6: ......
Page 24: ...Rev 00 08 17 24 Product description MagicControl 4 0 CM40 ...
Page 59: ...Rev 00 08 17 MagicControl 4 0 CM40 Operation 59 ...
Page 60: ...Rev 00 08 17 60 Operation MagicControl 4 0 CM40 ...
Page 74: ...Rev 00 08 17 74 Fault clearance MagicControl 4 0 CM40 ...
Page 82: ...Rev 00 ...