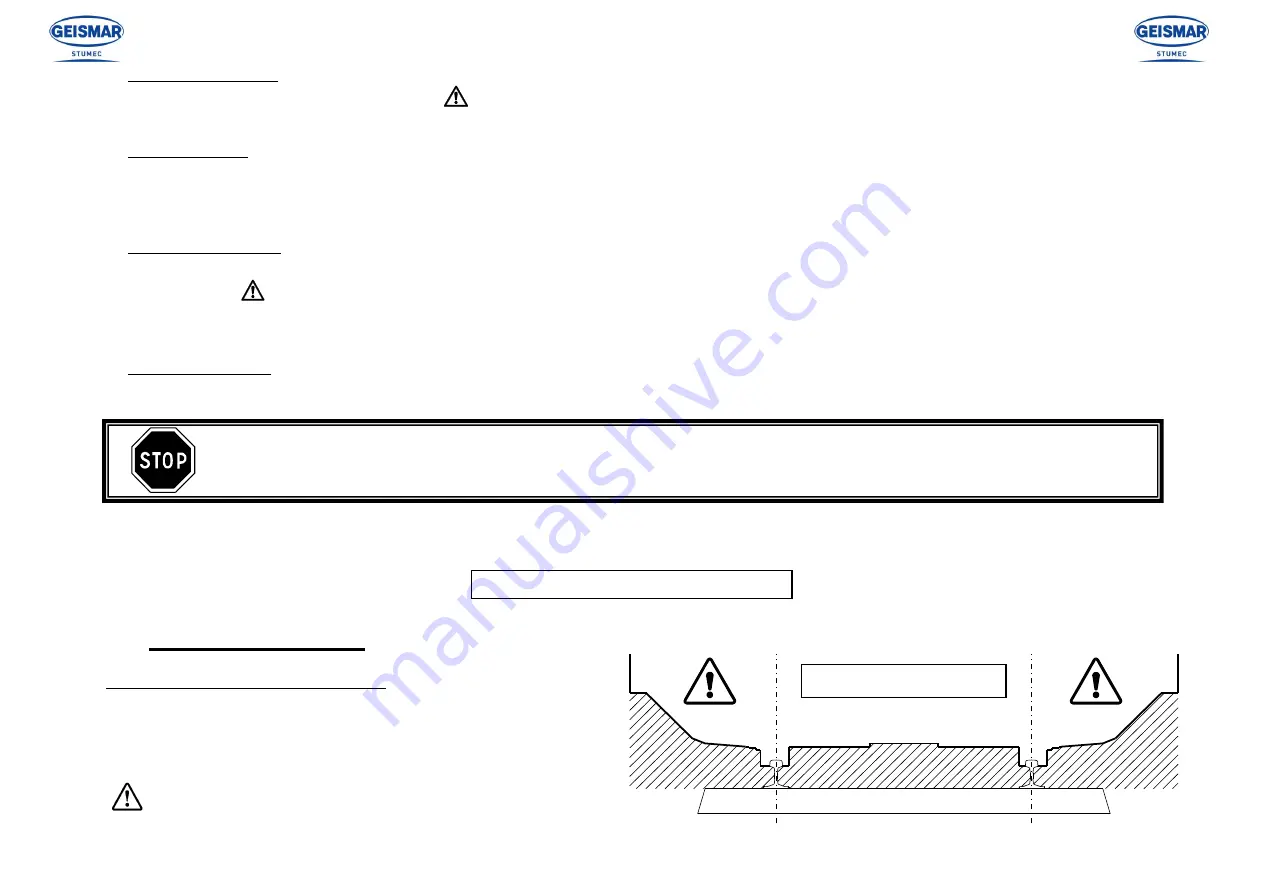
3.3
MIW3_Gb_01165_130204.doc
4.1
•
Checking the fuel level
(this check is done with the engine stopped)
-
Check the fuel level and top up if necessary (
: be sure to refer to
1.3 “General safety instructions” / “Utilisation and handling of fuel” and 3.2.2
“Filling with fuel”).
•
Functional checks
(these checks are done with the engine stopped)
-
Check the correct operation of the accelerator trigger, the accelerator trigger safety lock and the combination lever. These devices must move freely and not
be modified.
-
Check that the shaft rotates freely under no load.
•
Check of safety devices
-
Make sure that the handles are clean and dry.
-
Start the engine (
: be sure to refer to
4.2 “Utilisation of the machine”) and check that the engine stops when the combination lever is moved to the “
0
”
position.
-
Check that the wrench does not rotate when the accelerator trigger is in the idle position (refer to §5.1.4 "Carburettor" if adjustment is required).
•
Miscellaneous checks
-
Check that no oil leaks are present and that all mounting bolts are tight.
IF
ANY
ABNORMALITY
IS
FOUND
DURING
THIS
INSPECTION
PHASE
OR
IN
THE
COURSE
OF
UTILISATION,
THE
MACHINE
MUST
BE
RESTORED
TO
COMPLIANCE
BY
COMPETENT
PERSONNEL
OR
BY
THE
MANUFACTURER
BEFORE
BEING
USED
AGAIN
.
CHAPTER 4 – UTILISATION
4.1
Conditions of utilisation
Working zone and position of operator
The operator must work in the zone between the two rails of the same
track. The operator must be inside this zone in order to carry out bolting
or screwing work (on the inside and outside of the rail).
If specific work has to be done from outside the working zone,
check the safety conditions, particularly if traffic on the adjacent
line is not interrupted.
WORKING ZONE
Summary of Contents for MIW.3
Page 1: ... MIW 3 PORTABLE MOTOR IMPACT WRENCH MIW 3 ANGLAIS ...
Page 2: ... ...
Page 46: ......
Page 47: ......
Page 48: ......
Page 49: ......
Page 50: ......
Page 51: ......
Page 52: ......
Page 53: ......
Page 54: ......
Page 55: ......
Page 56: ......
Page 57: ......
Page 58: ......
Page 59: ......
Page 60: ......
Page 61: ......
Page 62: ......
Page 63: ......
Page 64: ......
Page 65: ......
Page 66: ......
Page 67: ......
Page 68: ......
Page 69: ......
Page 70: ......
Page 71: ......