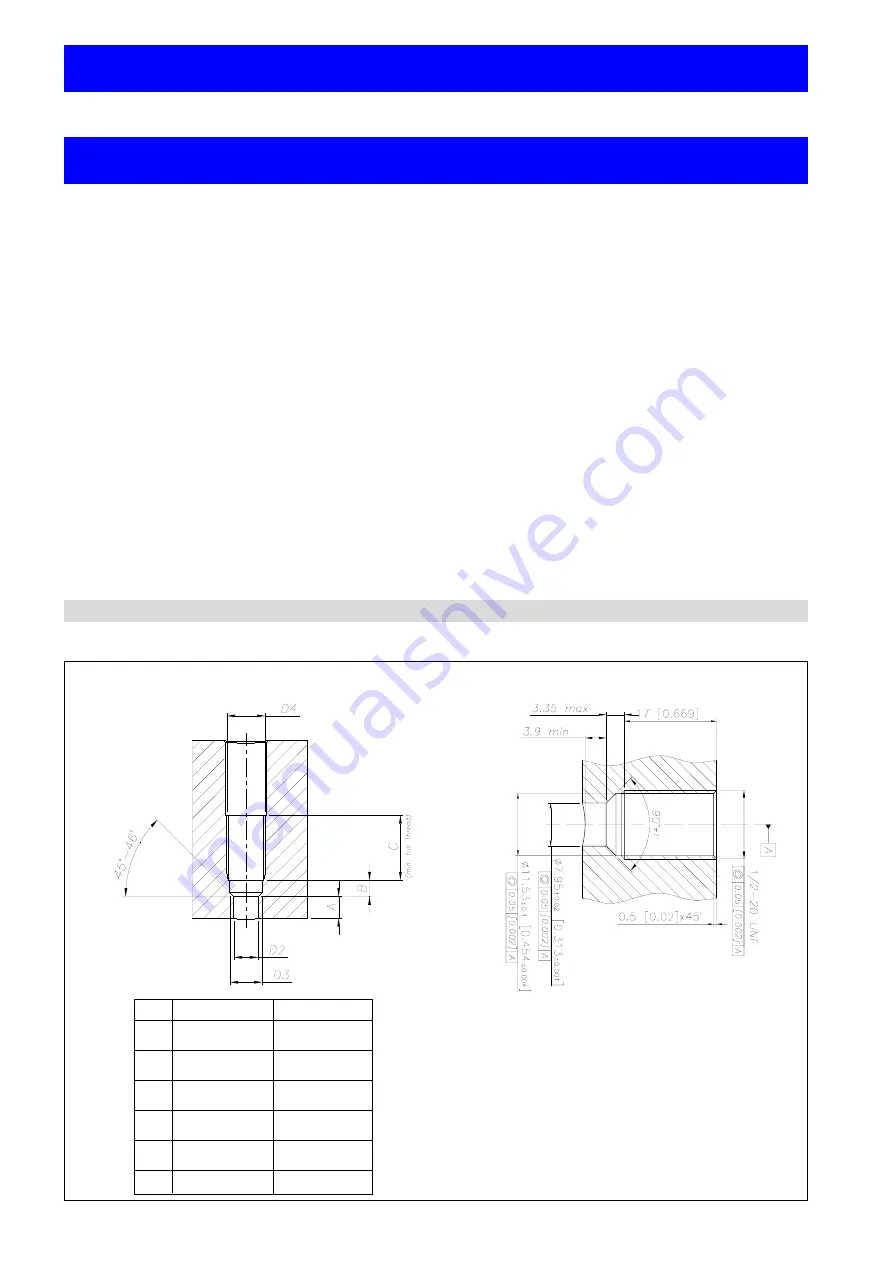
10
80636B_MAN_HMF - HWF_05-2022_ENG
5� Mechanical Dimensions
The installation seat has to be realized:
D1
1/2-20UNF M18x1�5
D2
.313 ±.001”
.398 ±.001”
[7.95 ±0.02mm]
[10.10 ±0.02mm]
D3
.454 ±.004”
.634 ±.004”
[11.53 ±0.1mm]
[16.10 ±0.1mm]
D4 .515”
[13mm]
.790”
[20mm]
minimum
minimum
A .225”
[5.72mm]
.240”
[6.10mm]
minimum
minimum
B .17”
[4.3mm]
.16”
[4.0mm]
maximum
maximum
C .75”
[19mm]
.99”
[25mm]
Rigid rod / flexible sheathing / flexible plus thermocouple version
Exposed capillary version
6� Installation and positioning on the machine
TECHNICAL DATA
Extrusion processes require very high temperatures. Extrusion pressure can be checked by means of especially
designed transducers. Thanks to their special mechanical construction, in which the measurement element is
isolated from the Melt, they resist to such high temperatures. The constructive principle is based on hydraulic of
pressure; mechanical strain is transferred by means of a non-compressible transmission liquid.
Strain gauge technology translates the physical quantity (pressure) into an electrical signal.
Following advice for extending the sensors lifetime.
a) Avoid shocks and abrasions to the in contact diaphragm. Protect the transducer with its cover each
time you remove it from its seat.
b) The seat must be prepared perfectly and with appropriate tools in order to respect the depth and axiality
of the holes and tapping.
Pay particular attention to the coaxiality of the holes to the thread, because diaxialities greater than 0.2 mm will
break the transducer during assembly. It is essential that hole depth guarantees the absence of chambers or air
pockets in which extrusion material may be trapped.
To prevent contact with the extrusion screw or with tools used to clean the extrusion chamber, the front diaphragm
must not extend from the inner wall of the extruder.
c) Before assembling the transducer in machines already in operation, make sure that the housing is clean.
Remove any residual with the suitable cleaning device.
d) The transducer should be removed only with the machine empty (without pressure) but still hot.
e) The transducer should be cleaned with solvents for the material being processed.
Any mechanical action on the contact diaphragm modifies its operation and could break it.
6�1� Installation seat
For the mechanical dimensions please keep as reference the product datasheets or Gefran website www.gefran.com