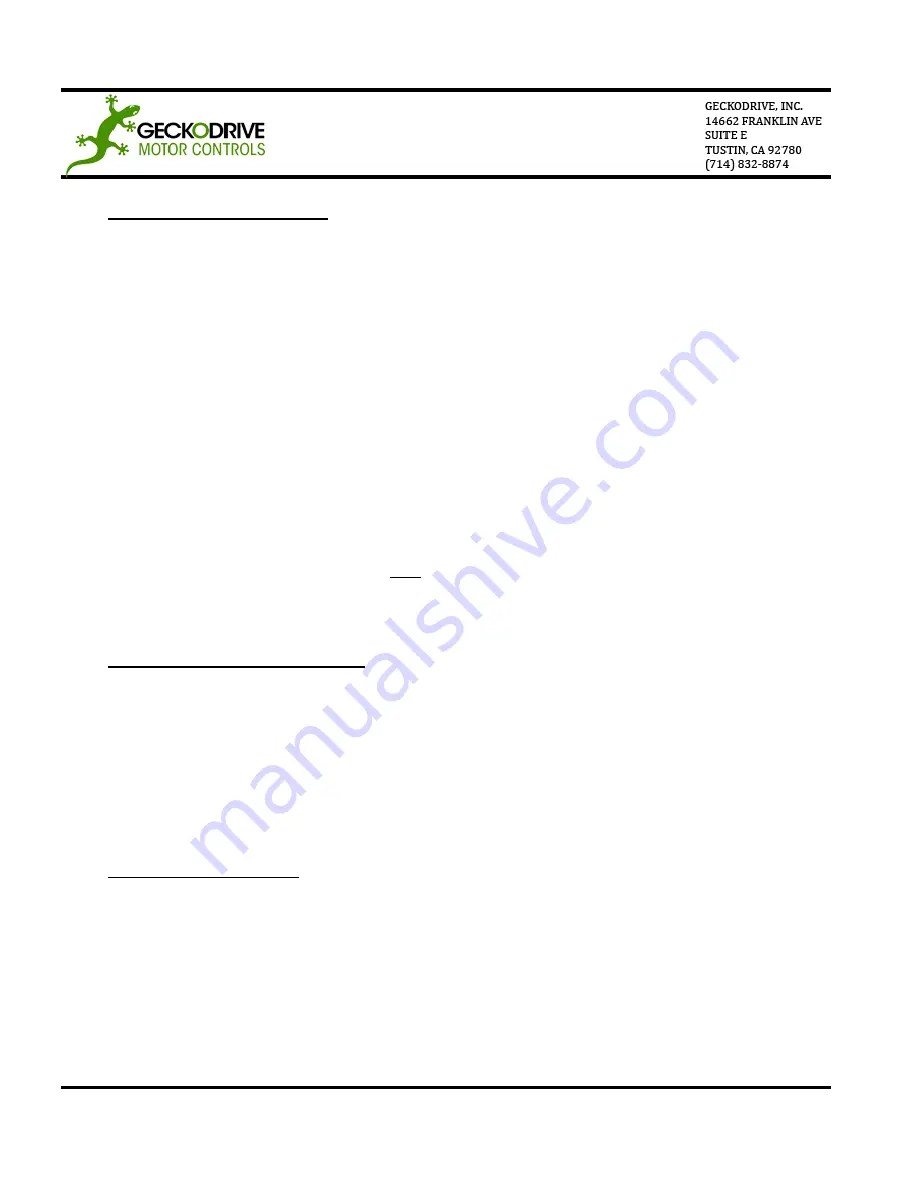
3
G320X SERVO DRIVE
REV 10: May 13, 2010
STEP 1: CONNECTING THE ENCODER
The encoder must be at minimum a 25 line-count digital quadrature encoder and must operate on a 5VDC power supply. If
the encoder supply current is more than 50 mA, use an external +5VDC supply. It may have an INDEX output, which will not be
used. If it has differential outputs, use only the “+” phase outputs.
TERMINAL 6
Encoder Ground
Connect the encoder power supply ground to this terminal.
TERMINAL 7
E5VDC
Connect the e5VDC to this terminal
TERMINAL 8
CH A
Connect the encoder channel “A” to this terminal
TERMINAL 9
CH B
Connect the encoder channel “B” to this terminal
To determine the optimal encoder line count, please follow the instructions below.
1.) Determine motors no load RPM
2.) Calculate rated RPM as 80% of no load RPM
3.) Divide (#2) by 60 to get revolutions per second
4.) Determine the CNC program’s maximum step pulse frequency (in Hz)
5.) Divide (#4) by (#3), which will give you the maximum counts per revolution
6.) Divide (#5) by 4, which will give you the max line count
7.) Pick the first standard line count below (#6)
An example of using that formula with a 45kHz step pulse frequency and a maximum motor RPM of 3000:
(45kHz / 40) / 4 = 281.25
STEP 2: CONNECTING THE POWER SUPPLY
IMPORTANT:
Never
put a switch on the DC side of the power supply! This will damage, if not destroy, your drive!
Keep the power supply leads short and use the largest wire gauge that will easily fit in the terminals. If the lead length is more than
18” use a 1000 uF capacitor across the G320X power supply terminals. Make sure your power supply can provide the peak current
the motor may draw. The power supply voltage must be between 18 VDC and 80 VDC.
TERMINAL 1
POWER GROUND
Connect the power supply (-) to this terminal.
TERMINAL 2
+18 TO 80 VDC
Connect the power supply (+) to this terminal
STEP 3: TESTING THE ENCODER
At this point the encoder should be tested for functionality. You can test the encoder on the G320X by watching the indicator LEDs
on the board.
Turn on the power supply. The FAULT indicator (red LED) should be on for 1 second and then turn off. The IN-POSITION indicator
(green LED) should turn on and remain on. The POWER indicator (green LED) should always be on. Turn the motor shaft VERY
slowly by hand. The IN-POSITION indicator (green LED) will turn off when you turn the motor more than two encoder counts. The
Warn indicator (yellow LED) will turn on when you have turned the motor more than 128 encoder counts. The FAULT indicator (red
LED) will turn on when you turn the motor past the following error limit (see option switch section). After 1 second the FAULT light
will turn off and the IN-POSITION LED will come back on.