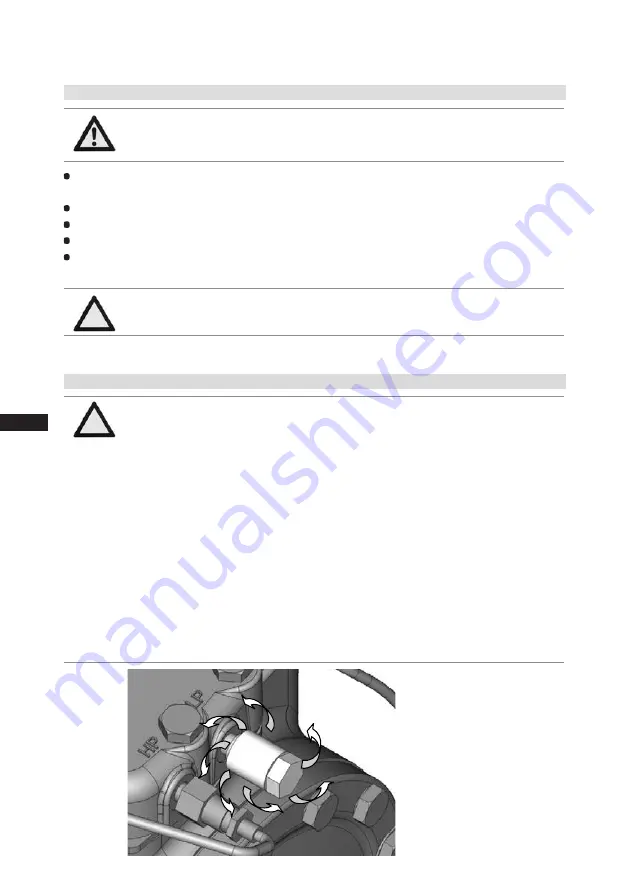
20
D
GB
F
E
96422-07.2018-DGbFEI
CO
2
streaming
out
Fig. 15
6
|
Commissioning
Check that the safety and protection devices (pressure switch, motor protection, electrical contact
protection measures, etc.) are functioning properly.
Switch on the compressor and let it run for at least 10 minutes.
The machine should reach a state of equilibrium.
Check the
oil level
: The oil level must be visible in the sight glass.
After a compressor is replaced, the oil level must be checked again. If the level is too high, oil
must be drained off (danger of oil liquid shocks; reduced capacity of the refrigerating system).
WARNING
Ensure that both shut-off valves are open before starting the
compressor!
ATTENTION
If larger quantities of oil have to be topped up, there is a risk of oil
impact effects. If this is the case, check the oil return!
6.6 Start-up
6.7 Decompression valves
ATTENTION
The compressor is fitted with two decompression valves. One valve
each on the suction and discharge side. If excessive pressures are
reached, the valves open and prevent further pressure increase.
Thereby CO
2
is blown off to the ambient!
In the event that a pressure relief valve activates repeatedly, check
valve and replace if necessary as during blow-off extreme condi-
tions can occure, which may result in a permanent leak. Always
check system for refrigerant loss after activation of pressure relief
valve!
The decompression valves do not replace any pressure switches
and the additional safety valves in the system. Pressure switches
must always be installed in the system and designed or adjusted in
accordance with EN 378-2 or appropriate safety standards.
Failure to observe can result in risk of injury from CO
2
streaming
out of the two decompression valves!