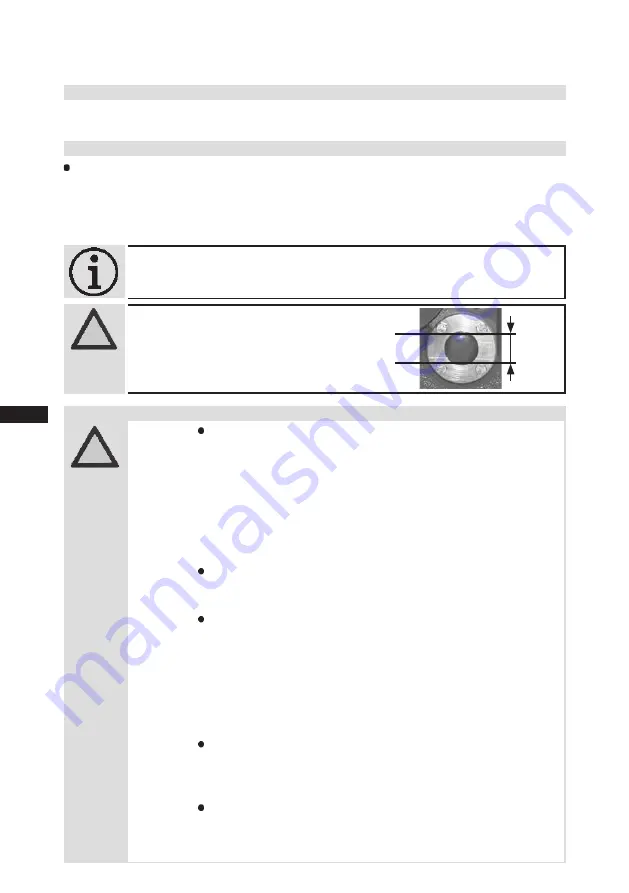
8
D
GB
F
E
I
Ru
09963-11.2015-DGbFEIRu
3
|
Areas of application
ATTENTION! Compressor operation is possible within the operating limits
shown in the diagrams. Please note the significance of the shaded
areas. Thresholds should not be selected as design or continuous
operation points.
- Permissible ambient temperature (-20°C) - (+60°C)
- Max. permissible discharge end temperature 140 °C
- Max. permissible switching frequency 12x /h.
- A minimum running time of 3 min. steady-state condition
(continuous operation) must be achieved.
For operation with supplementary cooling:
- Use only oils with high thermal stability.
- Avoid continuous operation near the threshold.
For operation with capacity regulator:
-
Continuous operation, when the capacity regulator is activated,
is not permissible and can cause damage to the compressor.
- The suction gas superheat temperature may need to be reduced
or set individually when operating near to the threshold.
-
When the capacity regulator is activated, the gas velocity in
the system can not under certain circumstances ensure that
sufficient oil is transported back to the compressor.
For operation with frequency converter:
- The maximum current and power consumption must not be
exceeded. In the case of operation above the mains frequency,
the application limit can therefore be limited.
When operating in the vacuum range, there is a danger of air
entering on the suction side. This can cause chemical reactions,
a pressure rise in the condenser and an elevated compressed-gas
temperature. Prevent the ingress of air at all costs!
The compressors are filled at the factory with the following oil type:
- for R134a, R404A/R507, R407C
FUCHS Reniso Triton SE 55
- for R22
FUCHS Reniso SP 46
Compressors with ester oil charge (FUCHS Reniso Triton SE 55) are marked with an X in the type
designation (e.g. HG
X
5/945-4).
3.1 Refrigerants
• HFKW / HFC:
R134a, R404A/R507, R407C
• (H)FCKW / (H)CFC:
R22
3.2 Oil charge
3.3 Limits of application
INFO!
For refilling, we recommend the above oil types.
Alternatives:
see lubricants table, Chapter 7.5.
The oil level must be in the
visible part of the sight
glass; damage to the com-
pressor is possible if over-
filled or underfilled!
ATTENTION!
max.
min.
1,8 Ltr.
oil level
Fig. 3
~
~