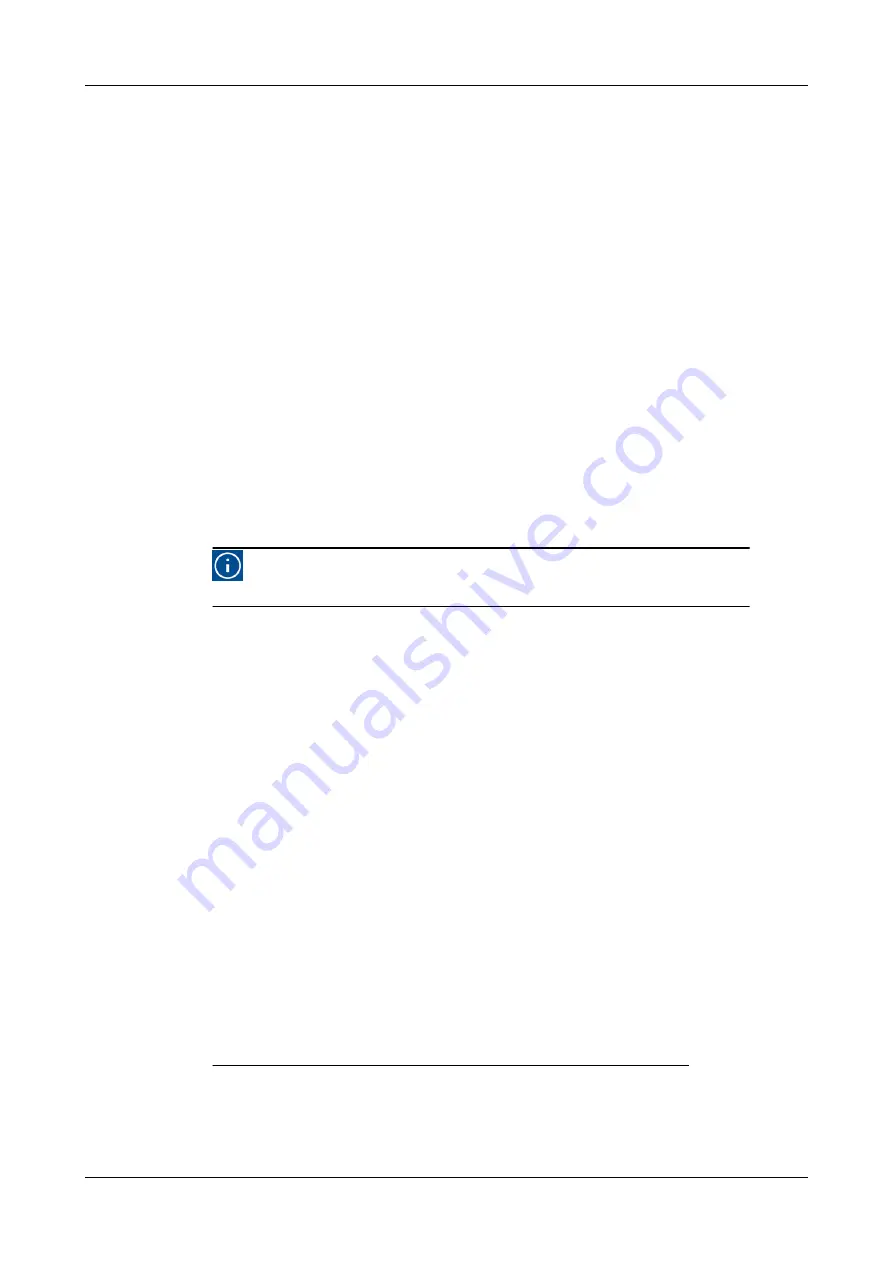
Re-adjustment procedure:
i.
Run the compressor for 15 minutes until the crankcase oil is at its stable
operating temperature [Toil] of 50
o
C and check:
1) The lubricating oil pressure difference (A)
2) The control oil pressure difference (B)
After the initial run the oil pressure differences should be slightly higher.
ii.
Determine the lubricating oil pressure difference (difference between the
pressure gauges of the oil and suction or [dOil]).
iii.
Determine the control oil pressure difference (difference between the
pressure gauges of oil pump discharge
3
and suction.
iv.
Remove the plug of both oil pressure regulators if the pressures need to be
re-adjusted.
v.
Turn the slotted pin with a screwdriver clockwise or counter clockwise for a
higher or lower oil pressure respectively, until the required control &
lubricating oil pressure differences have been achieved
4
.
vi.
Replace both plugs.
Hint!
If the valve lifting fails, check the control oil pressure regulator!
1.4.6
Checking direction of rotation of motor shaft
Prior to installing the intermediate coupling element, the direction of rotation of
the motor shaft must be checked. The direction of rotation can be determined
from the arrow-sticker at the oil pump.
1.4.7
Installing the drive guards (if present)
Only after the compressor is ready for the initial startup! Refer to the drive guard
installing procedures included in the order documentation.
1.4.8
Initial oil warm up
Prior to the initial start-up, the crankcase heater (if present) must be energised.
For the min. oil temperature refer to “Product Information (PI)“.
1.4.9
Initial start-up
1.4.9.1 Limitations of part load operation and start-up
3
To be measured by means of a special control oil pressure gauge to be connected on the oil
pump.
4
Re-adjusting one regulator will affect the other one, so be sure that both regulators are
properly (re-)adjusted.
INSTALLATION AND PREPARATION FOR USE
PREPARATIONS FOR USE
P-NL-094_imm_VHS_English_13
28
26.07.2021