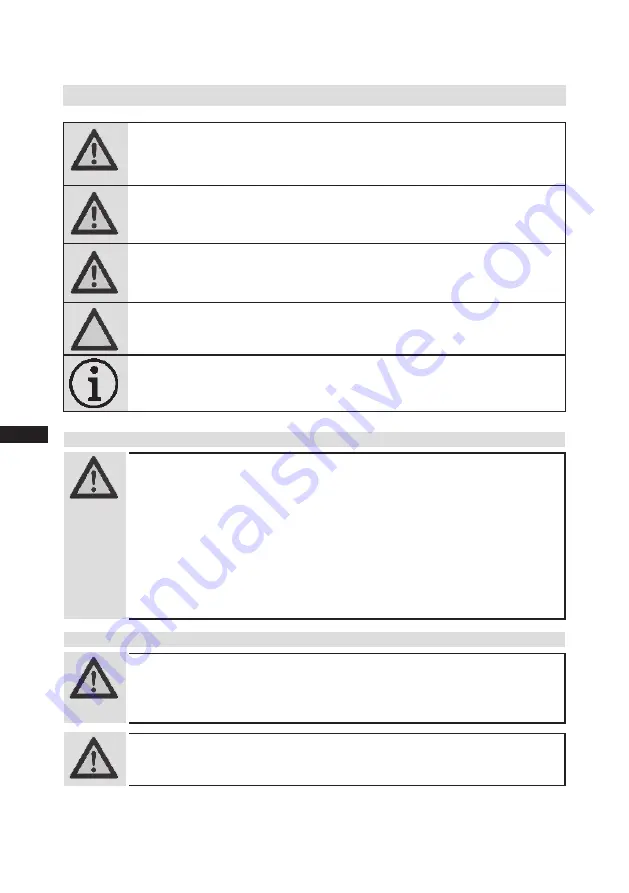
4
D
GB
F
E
96098-11.2014-DGbFE
1.1 Identification of safety instructions:
DANGER!
Indicates a dangerous situation which, if not
avoided, will cause immediate fatal or serious injury.
WARNING!
Indicates a dangerous situation which, if not
avoided, may cause fatal or serious injury.
CAUTION!
Indicates a dangerous situation which, if not
avoided, may cause fairly severe or minor injury.
ATTENTION!
Indicates a situation which, if not
avoided, may cause property damage.
INFO!
Important information or tips on simplifying work.
1
|
Safety
1.2 Qualifications required of personnel
WARNING! Inadequately qualified personnel pose the risk of
accidents, the consequence being serious or fatal injury.
Work on compressors is therefore reserved for personnel
with the qualifications listed below:
• For example, a refrigeration technician, refrigeration mechatronic
engineer.
As well as professions with comparable training, which enables
personnel to assemble, install, maintain and repair refrigeration and
air-conditioning systems. Personnel must be capable of assessing
thework to be carried out and recognising any potential dangers.
1.3 General safety instructions
DANGER!
•
Refrigerating compressors are pressurised machines and as such
call for heightened caution and care in handling.
The maximum permissible overpressure must not be exceeded,
even for testing purposes.
WARNING!
•
Risk of burns! Depending on the operating conditions, surface
temperatures of over 60°C on the discharge side or below 0°C on
the suction side can be reached.