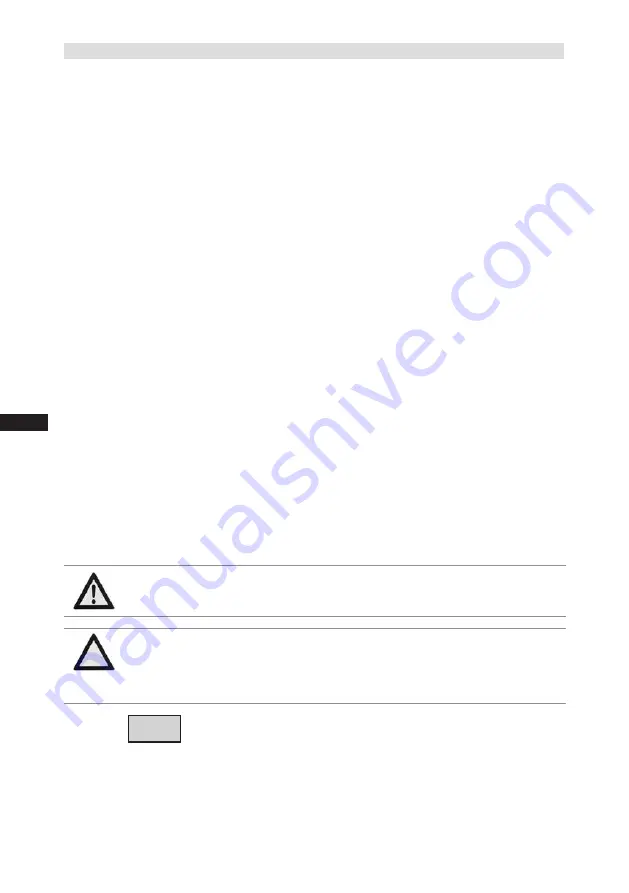
28
D
GB
F
E
I
96403-08.2019-DGbFEIRu
5.6 Circuit diagrams for control section Y/YY part winding start
Legend for circuit diagram Y/YY
(part-winding-start)
FB1
Fault protection switch (release current 30 mA)
FC2.1
Control fuse
FC2.2
Control fuse LR / oil sump heater
SF1
Control voltage O/I
QA2
Performance contactor part winding I
QA3
Performance contactor part winding II
KF3
Collective malfunction alarm contactor
KF4²
Electronic trigger unit INT69 EX2
KF5
Time relay for time delayed connect of the second part winding
BT3¹
Pump down- pressostat/ thermostat or external enabling switch
BP1/BP2¹ High/low pressure monitoring in accordance with the relevant national regulations
X SS
Terminal strip in the external switch cabinet
X KK
Terminal strip in the supplemental terminal box with recognised protection type
Optional
KF1
Time delay relay (on delay) max. 90 sec. (bypass time at start)
KF2
Time delay relay (drop-off delay) max. 90 sec. (function begins when the
oil pressure / monitoring is reached during operation)
BP3
Oil differential pressure sensor INT250 (Kriwan)
EB1
Oil sump heater (ATEX design)
LR
Capacity regulator (ATEX design)
¹) Operate these components with the appropriate type of protection only
²) Regard deviating connection voltage!
When using 24 V DC the installation of a safety isolating transformer is mandatory.
= Installation outside of the explosion endangered area
ATTENTION Ensure that power is supplied via QA2 to winding 1 (50 %)
(1U1 / 1V1 / 1W1) and via QA3 to winding 2 (50 %) (2U1/ 2V1 / 2W1).
The motor contactors (QA2 / QA3) are each to be rated for approx.
50 % of the max. operating current.
WARNING
With the installation of control and adjust parts the valid regulati-
ons for the explosion protection have to be observed!