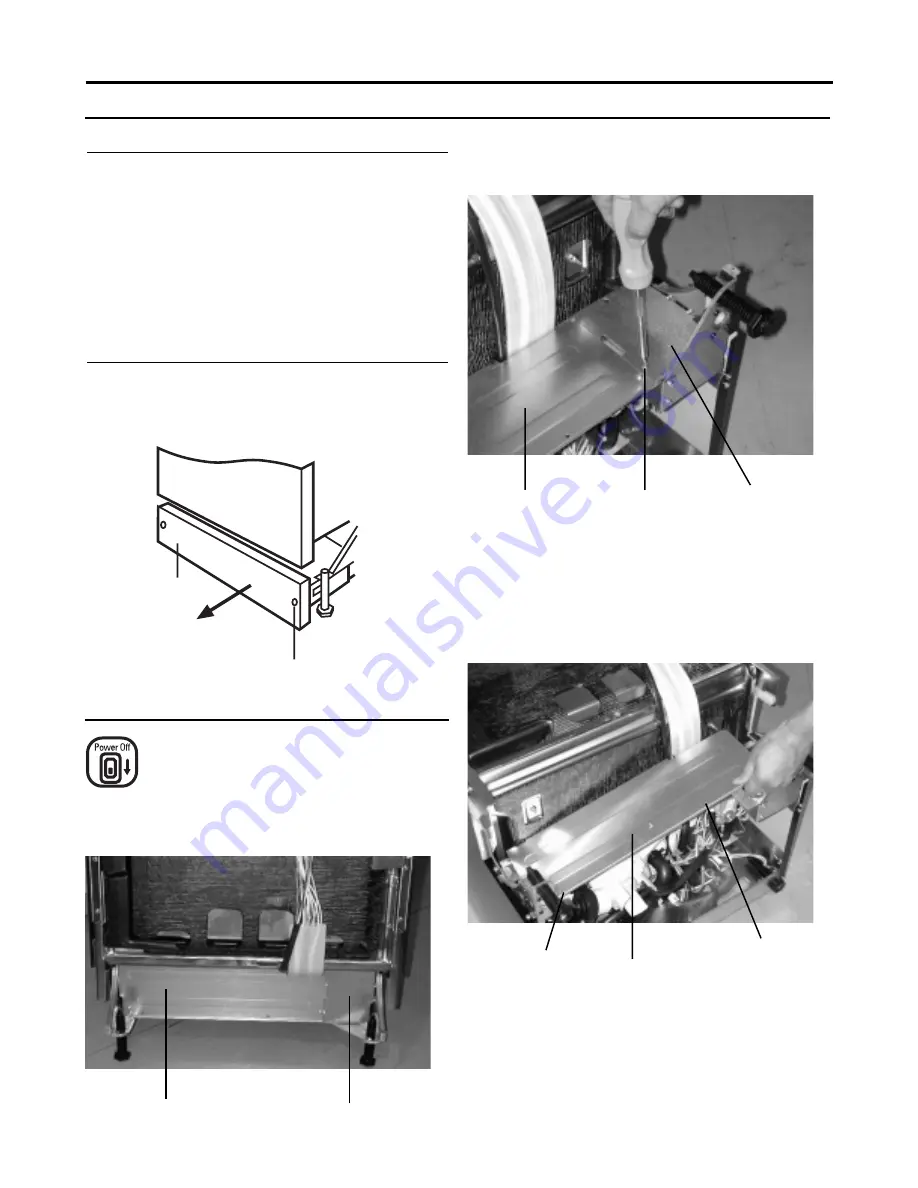
6000 & 7000 Series DISHWASHERS
PAGE 32
5.1 GENERAL ACCESS
These dishwashers have a removable Kick Panel fitted in
front of an Electrical Access Panel. These panels require
removal to access under sump components such as thermo-
stats, drain pump, water inlet solenoid valve, turbidity sensor,
pressure switch, wash motor capacitor, heating element,
wash motor, sump, drying fan etc.
The front door panel will require removal to gain access to
the control panel and internal components such as PCB,
door microswitch, door latching mechanism, wiring connec-
tions, detergent and rinse aid dispenser, etc.
5.1.1 Kick Panel removal
Remove the 2 fixing screws holding the Kickplate in position,
then slide the Kickplate out from under the dishwasher.
Remove the sound insulation panel.
5.0 SERVICE PROCEDURES
5.1.2.3 Remove the Electrical Access Panel.
Kickplate
Fixing Screws
5.1.2 Electrical Access Panel removal
5.1.2.1 Remove the Door Front Panel. (Refer to 5.2.2 or
5.2.3)
5.1.2.2 Remove the Mains Terminal Cover.
Electrical
Access Panel
Removal.
Mounting Screw.
Mounting Screw.
Mains Terminal
Cover.
Mains Terminal Cover.
Electrical Access Panel.
Mounting
Screw.
Electrical
Access Panel.
CAUTION. Switch off electrical power supply