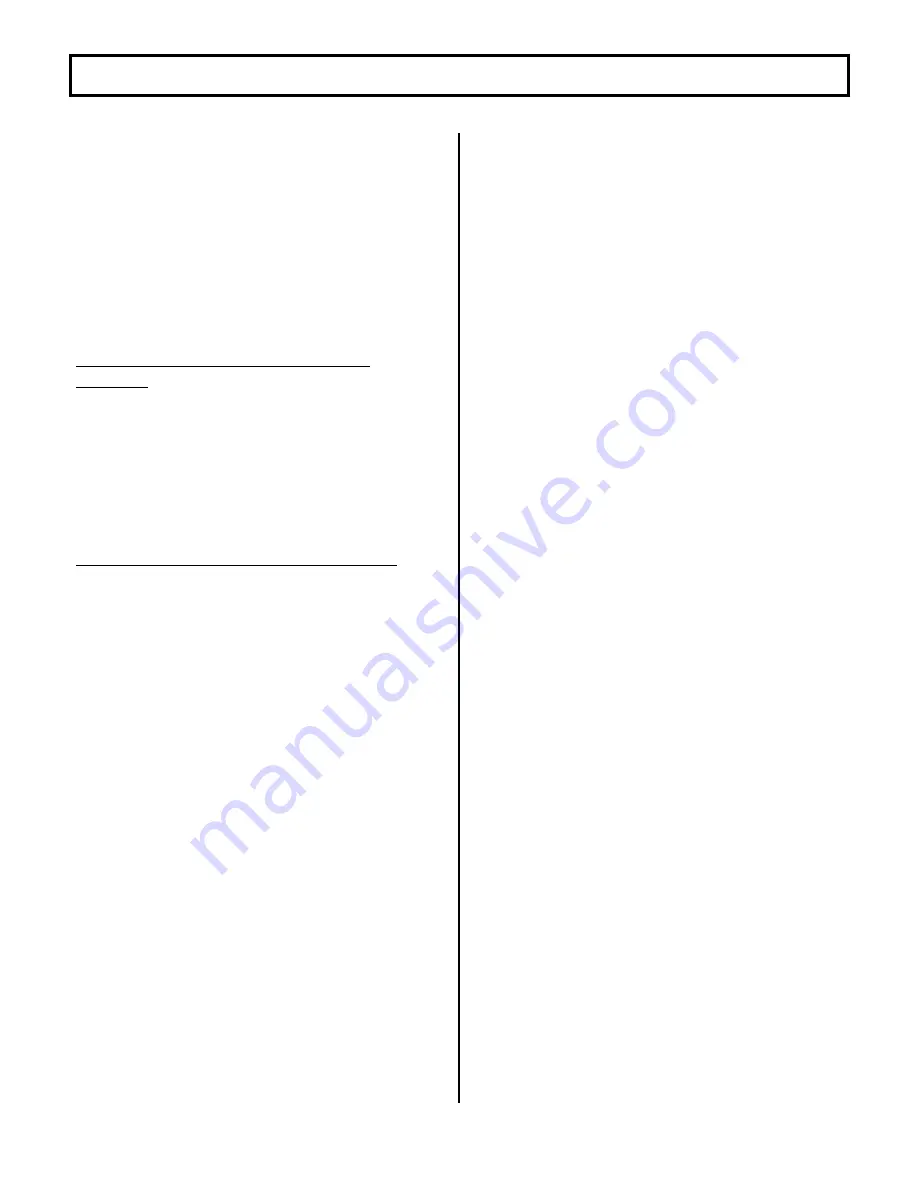
DIAGNOSTIC STATUS CODES
IT TRANSISTOR CONTROL
Page
14
April 2012
Section 4.0 TROUBLESHOOTING AND DIAGNOSTIC STATUS CODES
Section 4.1 General Maintenance Instructions
The transistor control, like all electrical apparatus,
does have some thermal losses. The semiconductor
junctions have finite
temperature
limits, above which
these devices may be damaged. For these reasons,
normal maintenance should guard against any action
which will expose the components to excessive heat
and/or those conditions which will reduce the heat
dissipating ability of the control, such as restricting air
flow.
The following Do’s and Don’ts should be
observed
:
Any controls that will be applied in ambient
temperatures over 100° F (40° C) should be brought
to the attention of the vehicle manufacturer.
All external components having inductive coils must
be filtered. Refer to vehicle manufacturer for
specifications.
The wiring should not be directly steam cleaned.
In
dusty areas, blow low-pressure air over the control to
remove dust. In oily or greasy areas, a mild solution
of detergent or denatured alcohol can be used to
wash the control, and then low-pressure air should be
used to completely dry the control.
For the control to be most effective, it must be
mounted against the frame of the vehicle. The metal
vehicle frame, acting as an additional heat sink, will
give improved vehicle performance by keeping the
control package cooler.
Apply a thin layer of
heat-transfer grease (such as Dow Corning 340)
between the control heat sink and the vehicle frame.
Control wire plugs and other exposed transistor
control parts should be kept free of dirt and paint that
might change the effective resistance between
points.
CAUTION: The vehicle should not be plugged
when the vehicle is jacked up and the drive
wheels are in a free wheeling position. The higher
motor speeds can create excessive voltages that
can be harmful to the control.
Do not hipot (or megger) the control. Refer to control
manufacturer before hipotting.
Use a lead-acid battery with the voltage and ampere
hour rating specified for the vehicle. Follow normal
battery maintenance procedures, recharging before
80 percent discharged with periodic equalizing
charges.
Visual inspection of FSIP contactors contained in the
traction and pump systems is recommended to occur
during every 1000 hours of vehicle operation.
Inspection is recommended to verify that the
contactors are not binding and that the tips are intact
and free of contaminants.
FSIP does not recommend that any type of welding
be performed on the vehicle after the installation of
the control(s) in the vehicle. FSIP will not honor
control failures during the warranty period when such
failures are attributed to welding while the control is
installed in the vehicle.
Section 4.2 Cable Routing and Separation
Electrical noise from cabling of various voltage levels
can interfere with a microprocessor-based control
system. To reduce this interference, FSIP
recommends specific cable separation and routing
practices, consistent with industry standards.
Section 4.2.1 Application Responsibility
The customer and customer’s representative are
responsible for the mechanical and environmental
locations of cables. They are also responsible for
applying the level rules and cabling practices defined
in this section.
To help ensure a lower cost, noise-free installation,
FSIP recommends early planning of cable routing
that complies with these level separation rules.
On new installations, sufficient space should be
allowed to efficiently arrange mechanical and
electrical equipment.
On vehicle retrofits, level rules should be considered
during the planning stages to help ensure correct
application and a more trouble-free installation.
Section 4.2.2 Signal/Power Level Definitions
The signal/power carrying cables are categorized into
four defining levels: low, high, medium power, and
high power. Within those levels, signals can be
further divided into classes.
Sections 4.2.2.a through 4.2.2.d define these levels
and classes, with specific examples of each. Section
4.2.3 contains recommendations for separating the
levels.