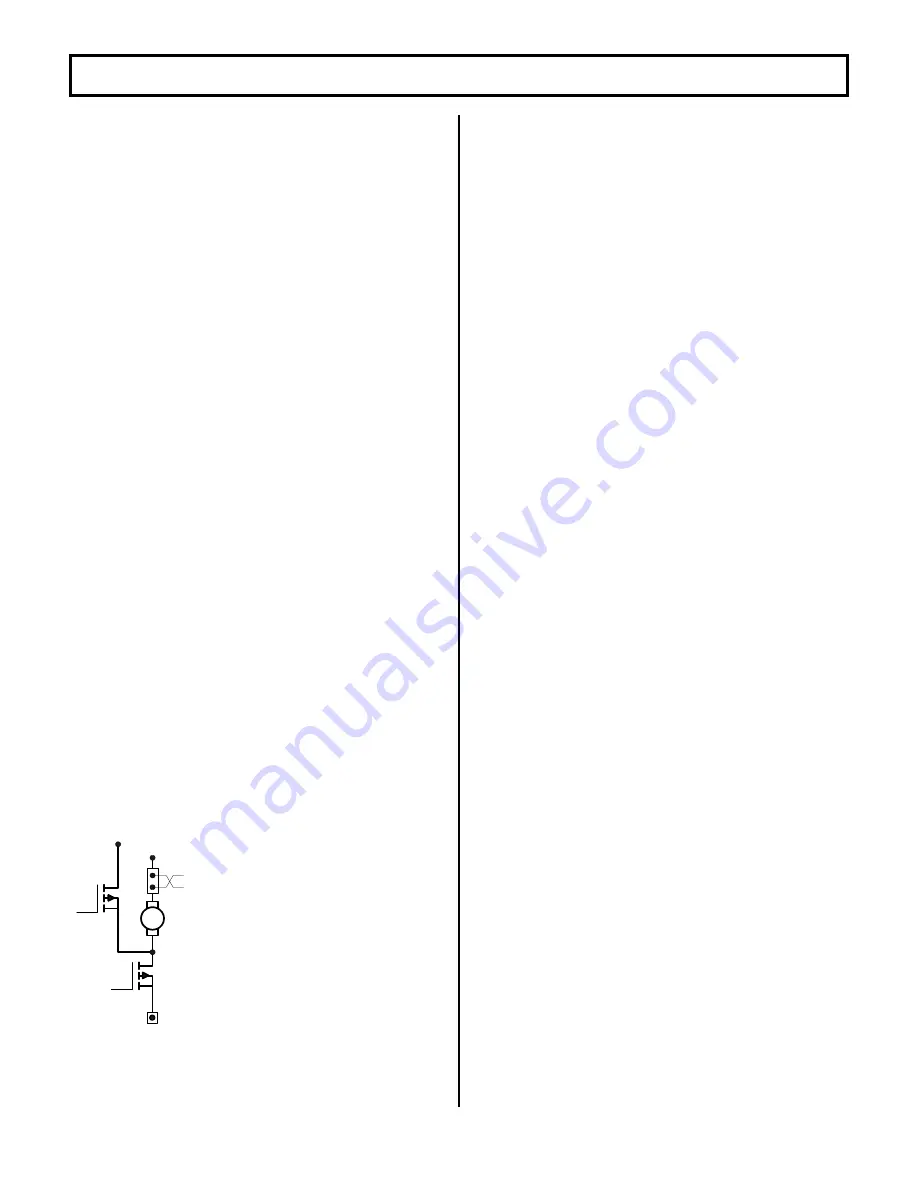
BASIC OPERATION AND FEATURES
SX TRANSISTOR CONTROL
Page
5
Section 2.1.1.a Standard Operation
The oscillator section of the card has two adjustable
features, creep speed and minimum field current. The
creep speed can be adjusted by Function 2 of the handset.
The field control section allows the adjustment of the field
weakening level in order to set the top speed of the motor.
This top speed function (Minimum Field Current) is enabled
when the armature current is less than the value set by
Function 24. Top Speed can be adjusted by Function 7 of
the handset .
The % ON-time has a range of approximately 0 to 100
percent. The SX controllers operate at a constant
frequency and the % ON-time is controlled by the pulse
width of the voltage/current applied to the motor circuits.
Section 2.1.1.b Control Acceleration
This feature allows for adjustment of the rate of time it
takes for the control to accelerate to 100% applied battery
voltage to the motor on hard acceleration. Armature C/A is
adjusted by Function 3 from 0.1 to 22 seconds.
Section 2.1.2 Current Limit
This circuit monitors motor current by utilizing sensors in
series with the armature and field windings. The
information detected by the sensor is fed back to the card
so that current may be limited to a preset value. If heavy
load currents are detected, this circuit overrides the
oscillator and limits the average current to a value set by
Function 4 and Function 8 of the Handset. The C/L setting is
based on the maximum thermal rating of the control.
Because of the flyback current through 3REC, the motor
current is usually greater than battery current, except at
100% ON time.
Section 2.1.3 Regenerative Braking to Zero Speed
Slow down is accomplished when
releasing accelerator pedal or
depressing brake pedal by providing
a regulated amount of retarding
torque for deceleration. If the vehicle
is moving, and the accelerator pedal
is released, the regen signal is
initiated. Once the regen signal has
been initiated, the field current is
increased (armature circuit shown in
Figure 5). Armature current is
regulated to the regen current limit as set by Function 9. As
the vehicle slows down, the field current continues to
increase, and transistor Q2 begins to chop. The field
current will increase until it reaches a preset value set by
Function 10, and transistor Q2 on-time will increase until it
reaches 100% on-time. Once both of the above conditions
have been met, and regen current limit can no longer be
maintained, the braking function is canceled. Part of the
energy produced by the motor during regen is returned to
the battery, and part is dumped in the motor as heat.
ARM
Q1
Q2
Figure 5
Section 2.1.4 Auxiliary Speed Control
Section 2.1.4.a Field Weakening
This function allows the adjustment of the field weakening
level in order to set the top speed of the motor. The function
is enabled when the armature current is less than the value
set by Function 24 and the accelerator input voltage is
greater than 2.9 volts. It is important to note that this
function is used to optimize motor and control
performance, and this setting will be determined by GE and
OEM engineers at the time of vehicle development.
This
setting must not be changed by field personnel without the
permission of the OEM.
Section 2.1.4.b Speed Limits
This feature provides a means to control speed by limiting
motor volts utilizing "adjustable speed limits", initiated by
individual limit switches. The NC switches are connected
between input points on the control card and battery
positive. The lower motor volt limit always takes priority
when more than one switch input is open. This motor volt
limit regulates top speed of the transistor controller, but
actual vehicle speed will vary at any set point depending on
the loading of the vehicle.
Section 2.1.4.c Top Speed Regulation
This feature requires a system tachometer. The standard
GE system tach is built into the motor and provides four
pulses per armature revolution. Once the control has been
calibrated to the vehicle parameters (gear ratio
and wheel rolling radius), using Function 1, speed can be
measured with a resolution of +/- 1 mph. When traveling
down an incline, if the vehicle speed increases to the
overspeed setting, the control automatically transitions to
the regen mode. The maximum incline on which the control
will be able to maintain regulation is determined by the
characteristics of the motor, the maximum regen armature
current limit setting (Function 9), and the maximum regen
field current limit setting (Function 10).
When the vehicle reaches the bottom of the incline, and
the vehicle speed decreases below the overspeed setting
on the level surface, the control automatically transitions
back to the normal running mode.
Section 2.1.5 Ramp Start
Updated Sept 2019