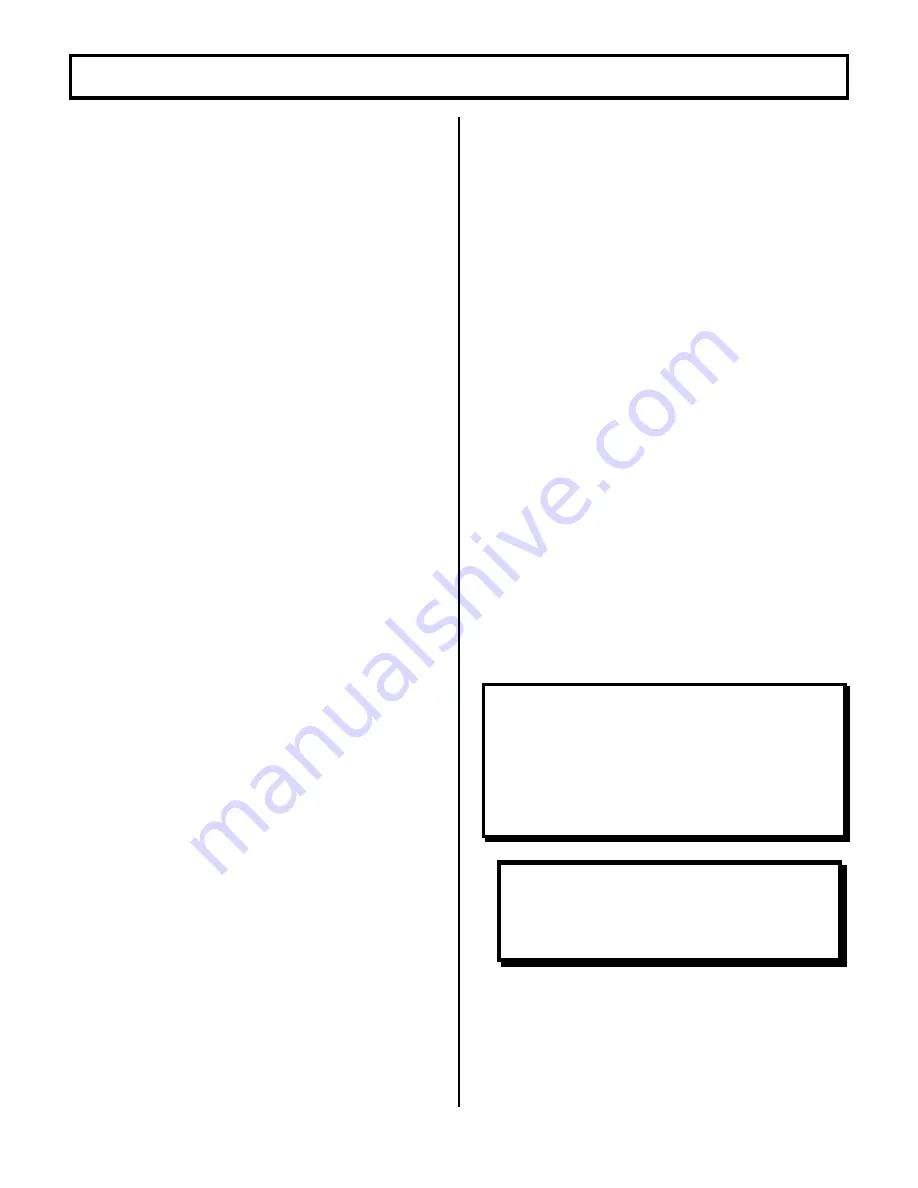
ADJUSTABLE FEATURES
SX TRANSISTOR CONTROLS
Page
65
September 2004
This function allows the monitoring of certain control
functions by looking directly at the RAM of the
microprocessor. Because absolute memory locations need
to be known, this function should not be used without
detailed instructions from the GE application engineer.
This function should only be adjusted by the vehicle OEM.
To ensure optimum operation of the control, this function
must be left with zero stored in this register.
FUNCTION 26
FIELD TO ARMATURE CURRENT RATIO
( Push CONT 11)
This function sets the ratio between armature and field
current when operating below the maximum field current
and above the Field Weakening Start point. The setting
represents the quantity of field current changed for each 1
amp of armature current changed.
For a 36/48V control:
Range
0 to 0.314 field amps/armature amp
Setting
0 to 13
Resolution
0.024 field amps/armature amp
Example
Setting of 10 = 0.24 field
amps/armature
amp
For a 72/80V control:
Range
0 to 0.269 field amps/armature amp
Setting
0 to 13
Resolution
0.021 field amps/armature amp
Example
Setting of 10 = 0.20 field
amps/armature
amp
For a 1000A control:
Range
0 to 0.507 field amps/armature amp
Setting
0 to 13
Resolution
0.038 field amps/armature amp
Example
Setting of 10 = 0.38 field
amps/armature
amp
FUNCTION 27
MINUTES REGISTER
(Push CONT 12)
This register is only intended for storage of the minutes
value for proper operation of the hour meter and should not
be adjusted.
FUNCTION 28
STORED STATUS CODE COUNT POINTER
( Push CONT 13)
This register contains the location of the last stored status
code recorded of the 16 stored status codes. These stored
status codes have caused a PMT controller shutdown
and/or disruption of normal vehicle operation.
To determine which stored status code was the last one
recorded, read the number stored in Function 28. Using the
Memory Map
for your logic card, match the
"stored status
code pointer number"
[the number shown in
(bold italics)
in the HS (Handset) number column] on the memory map,
with the number obtained from Function 28. This will be the
last stored status code recorded.
Note:
When scrolling through the stored status code
register, the register always starts at status code 1 and
scrolls to status code 16. Instructions for scrolling the
register are in section 6.3.2 of this instruction booklet.
FUNCTION 29
POWER STEERING HOURS
(ONES AND TENS)
( Push CONT 14 )
This register is only intended for storage of the ones and
tens values of the hours of operation of the power steering
motor and should not be adjusted.
FUNCTION 30
POWER STEERING HOURS
(HUNDREDS AND THOUSANDS)
( Push CONT 15 )
This register is only intended for storage of the hundreds
and thousands values of the hours of operation of the
power steering motor and should not be adjusted.
FUNCTION 48
MODE 1 ARMATURE CONTROLLED
ACCELERATION
( Push CONT 1)
This function allows for the adjustment of the rate of time it
takes for the control to accelerate to 100% applied battery
voltage to the motor on hard acceleration.
DASH DISPLAY INTERACTIVE MODES
The following functions (functions 48 through 63) are
mode settings that are activated from the Interactive Dash
Display. Each function must be set using the logic table
shown below. If you try to set this function outside these
guidelines, an error code will be displayed to prompt you
to enter the correct setting.
The following functions have function numbers larger
than the numbers on the Handset keyboard. To
access these functions. Push the CONT key and the
number shown in the following instructions at the
same time. THE SEAT SWITCH MUST BE CLOSED.