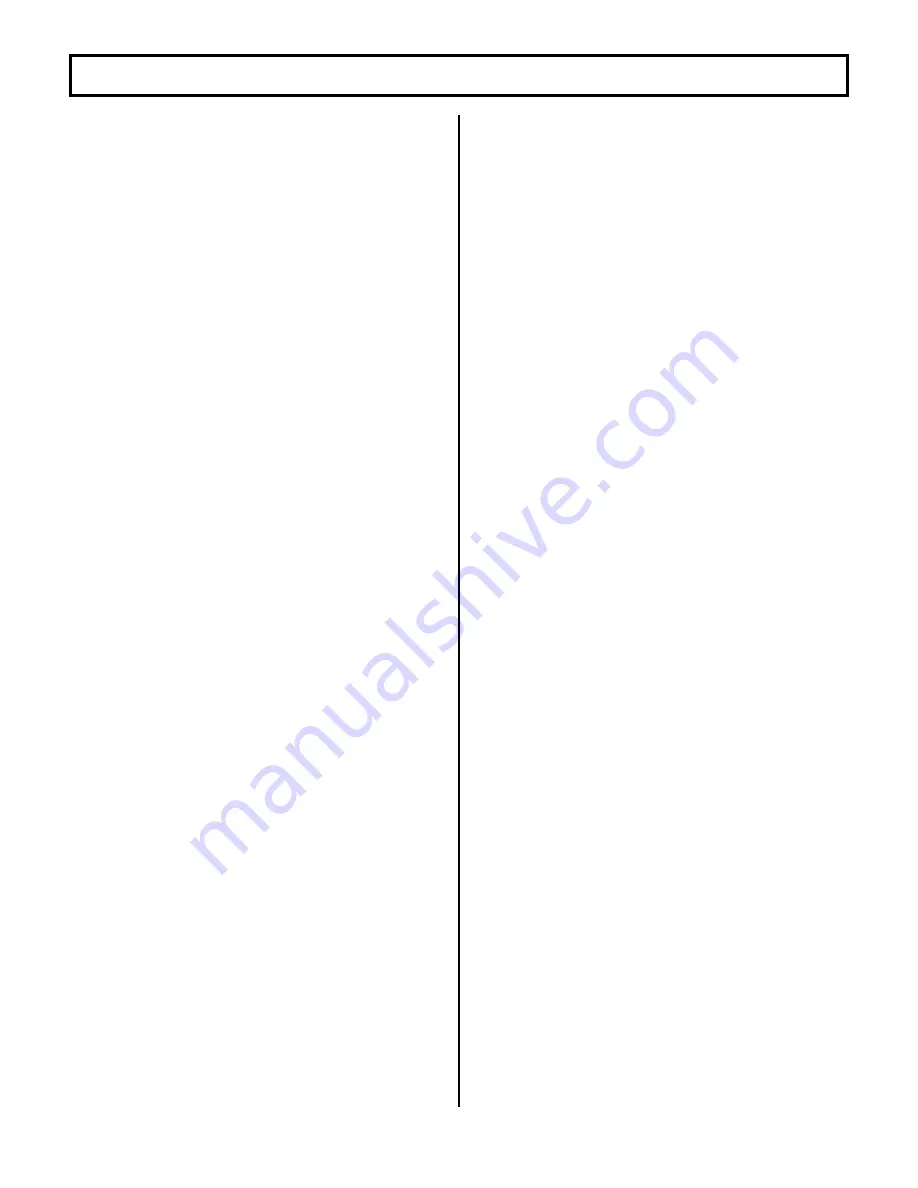
BASIC OPERATION AND FEATURES
SX TRANSISTOR CONTROL
Page
8
down to 50 percent of a nominal battery voltage of 36-84
volts, and 75 percent of a nominal battery voltage of 24
volts. Lower battery voltage may cause the control to
operate improperly, however, the resulting PMT should
open the Line contactor, in the event of a failure.
This feature is used to display Status Code 99 and/or
activate a speed limit when the vehicle operating hours
match the hours set into the maintenance alert register.
This feature is set with the Handset using Functions 19 and
20. The operator is alerted that maintenance on the vehicle
is required.
Section 2.3 Diagnostics
Section 2.3.4 Battery Discharge Indication (BDI)
Section 2.3.1 Systems Diagnostics
The latest in microprocessor technology is used to provide
accurate battery state of charge information and to supply
passive and active warning signals to the vehicle operator.
Features and functions:
The control detects the system's present operating status
and can be displayed to either the Dash Display or the
Handset. There are currently over 70 status codes that are
available with SX systems using Traction and Pump
controls and Truck Management Module (TMM). Along
with the status code display from the TMM, the SX control
is capable of reducing the current to the motor, alerting the
operator of a critical fault condition.
•
Displays 100 to 0 percent charge.
•
Display blinks with 20% charge. Disables pump circuit
with 10% charge. Auto ranging for 36/48 volt operation.
Adjustable for use on 24 to 80 volts.
Section 2.3.4.a Internal Resistance Compensation
Section 2.3.2 Status Codes
This feature is used when the Battery Discharge Indicator
is present. Adjustment of this function will improve the
accuracy of the BDI.
Section 2.3.2a Standard Status Codes
The SX traction control has over 30 Status Codes that
assist the service technician and operator in trouble
shooting the vehicle. If mis-operation of the vehicle occurs,
a status code will be displayed on the Dash Display for
vehicles so equipped, or be available by plugging the
Handset into the “y” plug of the logic card.
Section 2.3.5 Handset
This is a multi-functional tool used with the LX, ZX, and SX
Series GE solid state controls. The Handset consists of a
Light Emitting Diode (LED) display and a keyboard for data
entry. Note, for ordering purposes, a separate Handset part
is required for SX controls.
With the status code number, follow the procedures
outlined in DIAGNOSTIC STATUS CODES to determine the
problem and a solution.
Features and functions:
Note: The Status Code Instruction Sheets do not claim to
cover all possible causes of a display of a "status code ".
They do provide instructions for checking the most direct
inputs that can cause status codes to appear.
•
Monitor existing system status codes for both traction
and pump controls. Monitor intermittent random status
codes.
•
Monitor battery state of charge, if available.
•
Monitor hourmeter reading on traction and pump
controls. Monitor or adjust the control functions.
Section 2.3.2.b Stored Status Codes
This feature records the last 16 "Stored Status Codes" that
have caused a PMT controller shut down and/or disrupted
normal vehicle operation. (PMT type faults are reset by
cycling the key switch). These status codes, along with the
corresponding BDI and hourmeter readings, can be
accessed with the Handset, or by using the RS 232
communications port and dumping the information to a
Personal Computer terminal.
Section 2.3.6 RS 232 Communication Port
This serial communication port can be used with
Interactive Custom Dash Displays to allow changes to
vehicle operating parameters by the operator. Or, it can be
used by service personnel to dump control operating
information and settings into a personal computer program.
Section 2.3.3 Hourmeter Readings
Section 2.3.6.a Interactive Dash Display
This feature will display the recorded hours of use of the
traction and pump control to the Dash Display each time
the key switch is turned off.
Modes
The Interactive Custom Dash Display allows the operator to
select the best vehicle performance for changing factory
(task) conditions. There are four (4) "operator interaction
Section 2.3.3.a Maintenance Alert & Speed Limit
September 2004