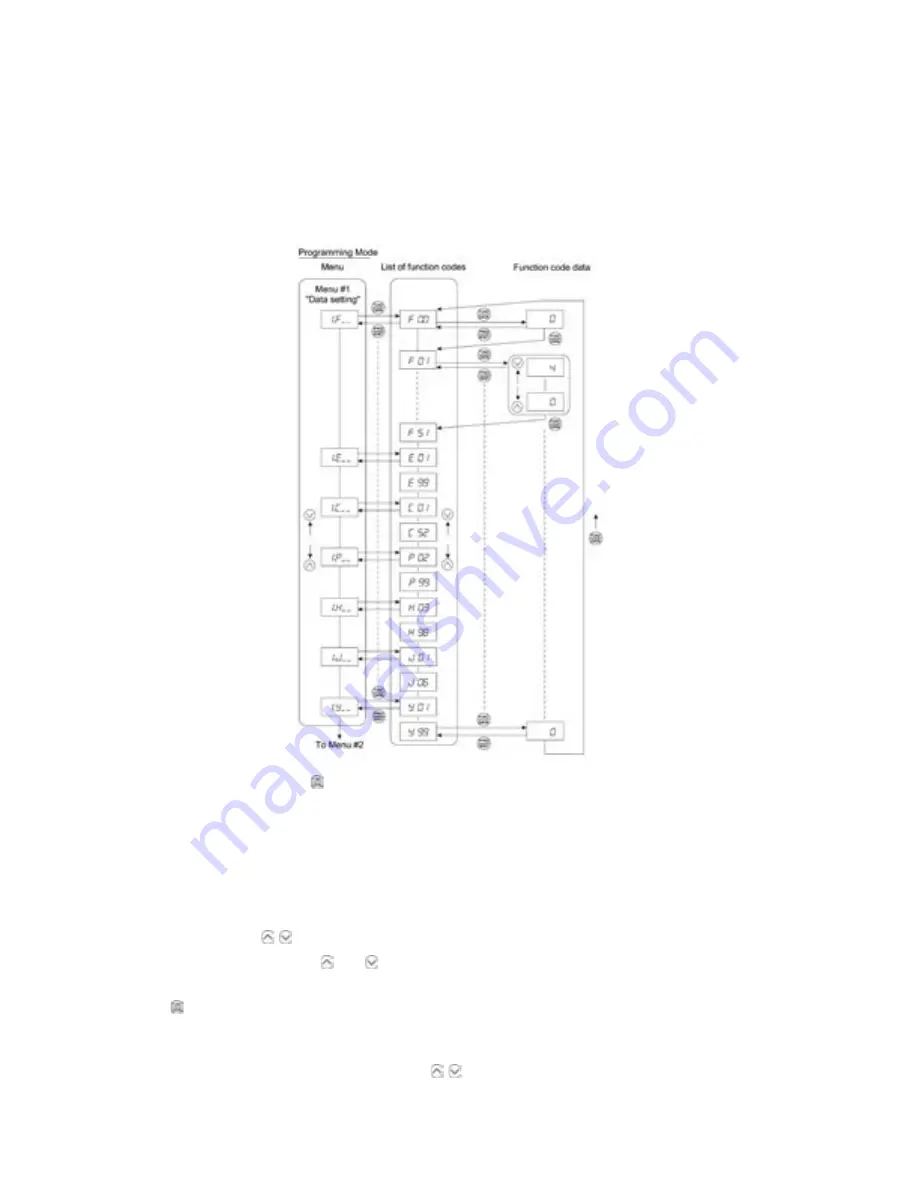
3-10
3-11
Changing, reflecting, and saving of function code data during running
Some function code data can be changed while the motor is running and some can not. Further, amongst the
function codes whose data can be changed while the motor is running, there are some for which the changes can
be reflected immediately and others for which that is not possible. Refer to the “Changes during running” column in
Chapter 5, Section 5.1 “Function Code Tables.”
Figure 3.4 shows the status transition for Menu #1 “Data settings” and Figure 3.5 shows an example of the function
code data changing procedure.
* Press the key when the y99 data is displayed to return to F00.
Figure 3.4 Status Transition Diagram for “Data Setting”
Basic key operation
This section will give a description of the basic key operation, following the example of the function code data
changing procedure shown in Figure 3.5.
This example shows you how to change function code F01 data from the factory default of “Potentiometer operation
on the keypad (F01 = 4)” to “ / key operation (F01 = 0).”
(1) With the menu displayed, use the and keys to select the desired function code group. (In this example,
select 1.F_ _).
(2) Press the key to display the function codes in the function code group selected in (1). (In this example, func-
tion code F00 will appear.)
Even if the function code list for a particular function code group is displayed, it is possible to transfer the
display to a different function code group using the / keys.
StockCheck.com
Summary of Contents for Fuji Electric MICRO-SAVER AF-300
Page 1: ...GEH 6647 AF 300 Mini Startup Guide S t o c k C h e c k c o m ...
Page 20: ...1 4 Notes S t o c k C h e c k c o m ...
Page 36: ...2 16 Notes S t o c k C h e c k c o m ...
Page 56: ...3 20 Notes S t o c k C h e c k c o m ...
Page 102: ...7 8 Notes S t o c k C h e c k c o m ...
Page 112: ...8 10 8 4 External Dimensions See dimensions table on next page S t o c k C h e c k c o m ...
Page 118: ...8 16 Notes S t o c k C h e c k c o m ...