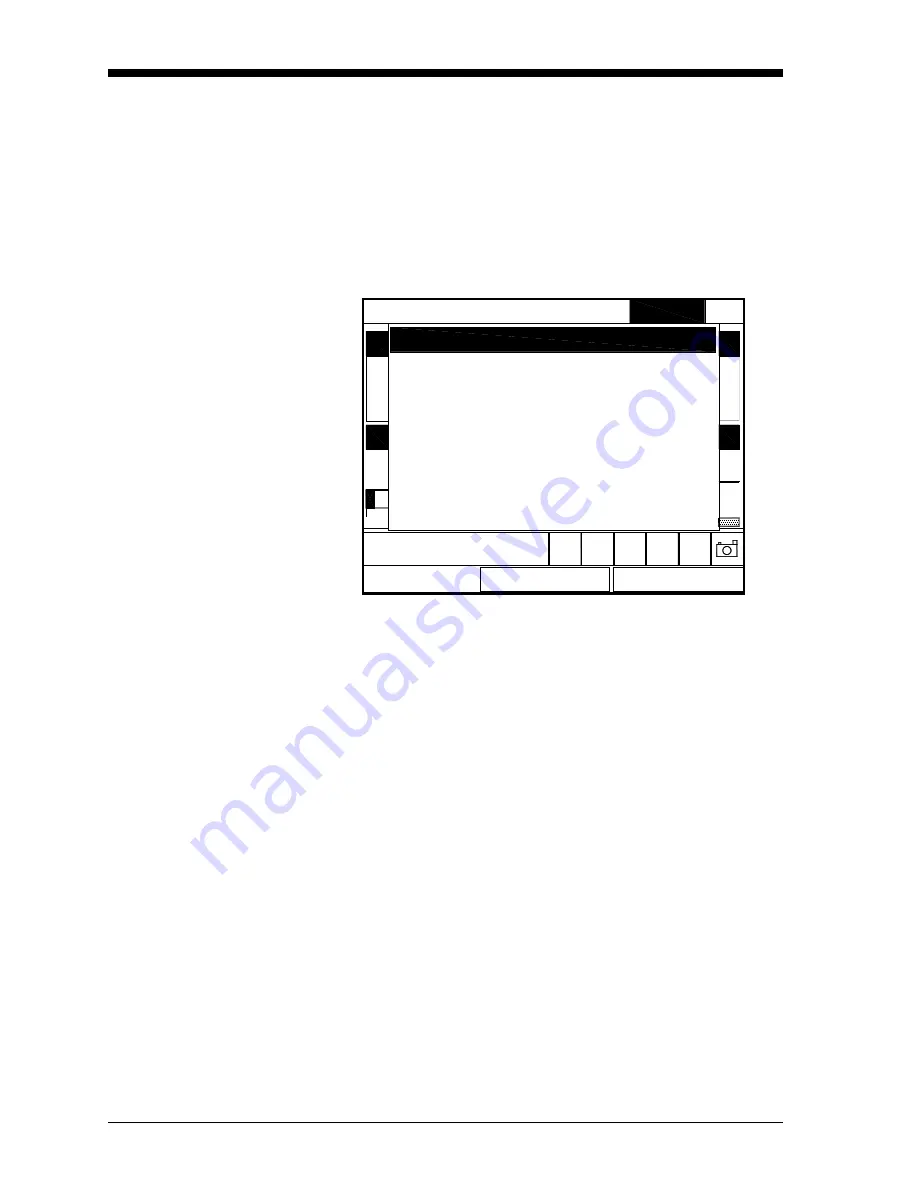
February 2009
1-10
Diagnostics
Testing the Watchdog
Timer Circuit
The CTF878 includes a watchdog timer circuit. If a software error
causes the meter to stop responding, this circuit automatically resets
the meter. A properly functioning CTF878 restarts if you run the
Watchdog Test.
To start the Watchdog Test, scroll to the Watchdog Test option in the
Test Menu and press
[ENTER]
. The screen appears similar to
Figure 1-8 below.
Figure 1-8: Watchdog Test Screen
Press
[F2]
(No) to cancel the test and return to the Menu screen, or
press
[F3]
(Yes) to start the test. The CTF878 should go blank for a
few seconds, and then restart. If it does not follow this sequence,
consult the factory.
Units
Site Program Meter Logging
*** WARNING ***
This test should automatically
restart your meter!
Press "Yes" to start the test.
Press "No" to cancel the test.
No
Yes
Service
Watchdog Test
Summary of Contents for CTF878
Page 1: ...GE Sensing Model CTF878 Clamp On Tag Flowmeter User s Service Manual ...
Page 2: ...GE Sensing Model CTF878 Clamp On Tag Flowmeter User s Service Manual 910 254SA4 February 2009 ...
Page 6: ...Chapter 1 ...
Page 18: ...Chapter 2 ...
Page 30: ...Chapter 3 ...
Page 43: ...Chapter 4 ...
Page 51: ...Chapter 5 ...
Page 63: ...Appendix A ...
Page 64: ...Service Record Introduction A 1 Data Entry A 1 ...