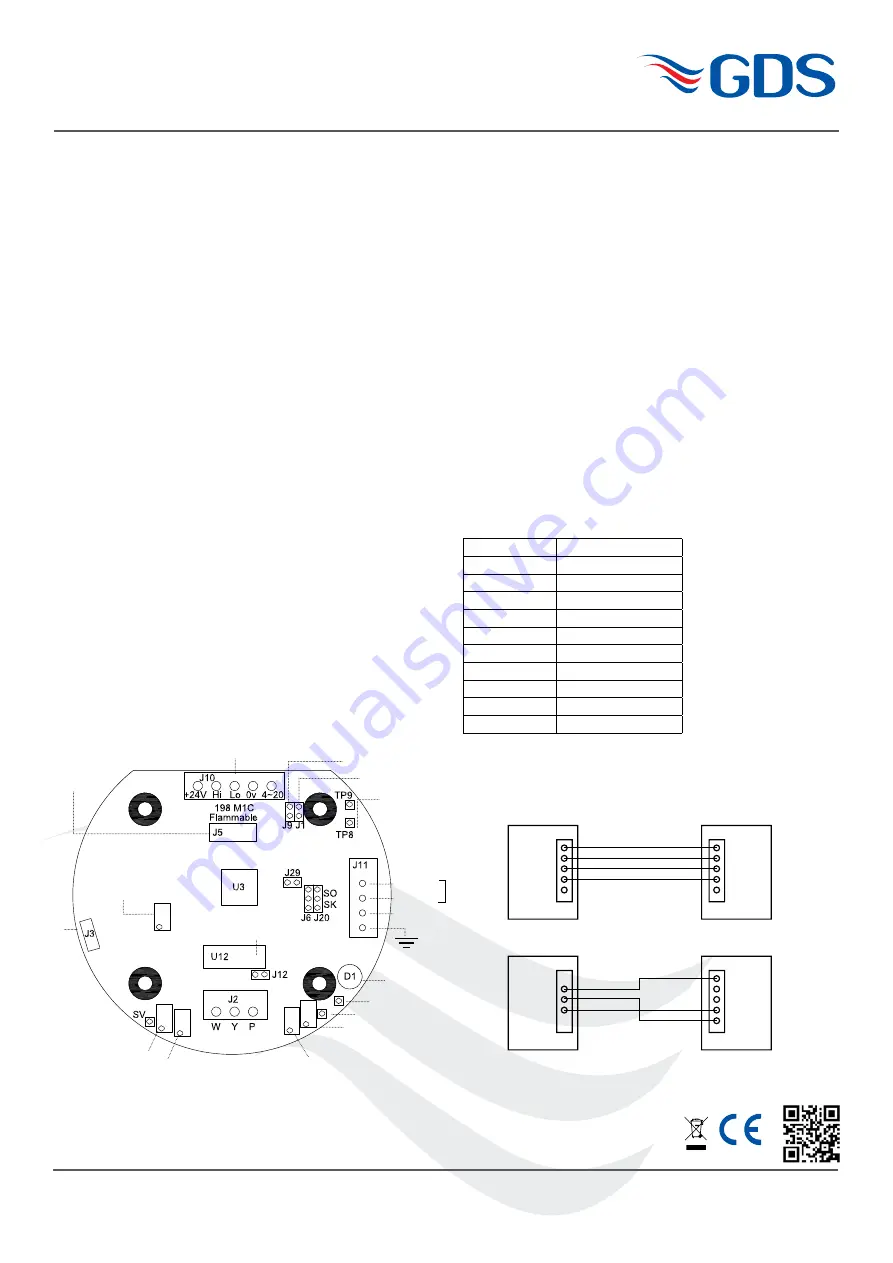
T E C H N O L O G I E S
Fig.1
Fig.2
Fig.3
The Combi sensors which have an LCD display fitted also incorporate 3
reed switches which can be activated using external magnets through the
glass window of the flameproof XDIwin enclosure.
These magnets do
not act instantly and have to be in close proximity to L, M and
R on the front display for a few seconds to activate a software
setup function.
The left magnet
enters the Auto zero ON or OFF menu.
This allows small drift changes in the sensor to be compensated for
but is not operational when the sensor readings are greater than 5%
of full scale. Therefore auto zero is inactive when a larger gas reading
is present. When the remove magnets message appears, move the left
magnet away and then the display shows if auto zero is ON or OFF. The
left magnet puts auto zero ON and the right magnet turns it OFF. With
no magnets present, the display will return to normal after a few seconds
timeout.
The right magnet
allows the CAN address of the sensor to be
changed. When the ADDRESS menu is displayed with a prompt to
remove the magnet, and then the display shows the address and that the
right magnet decreases it whilst the left magnet will increase it. This is then
stored in internal non volatile memory and the display will automatically
revert to normal operation.
The centre magnet
is used to inhibit the sensor. As with the left and right
magnet functions the display requests that you remove the magnet and
then the state of the inhibit appears on the LCD. The left magnet then puts
the sensor into inhibit whilst the right magnet removes it. An amber LED on
the front panel under the LCD flashes when the sensor is inhibited. When
all magnets are removed, the display will revert to normal operation.
The left and right magnets together allow the calibration menu
to be used.
Removing both magnets as instructed on the LCD presents the first part of
this multi menu which is ZERO. With no gas present use the left magnet
to increase the reading and the right magnet to decrease to achieve a
zero reading on the display. A timer is displayed on the LCD and when
this reaches 0, the next menu is displayed. This timer is 15 seconds
approximately and is reset back each time a magnet is near. Waiting till
timeout is acceptable but this timeout can be speeded up by placing a
magnet near to the centre position.
SPAN is the next part of the menu and gas should be applied to the
sensor at this time.
The left magnet increases the gain and the right magnet reduces gain. The
actual sensor value can be seen on the display to rise or fall respectively.
LOW ALARM is the next menu and left and right magnets increase and
decrease this value.
HIGH ALARM is next followed by OVER RANGE alarm.
The direction of the alarms is displayed as ^ for rising and v for falling but
these can be changed using left and right magnets together.
Sensor cell supply table
CAT300A
2v/300mA
CAT170A
2v/175mA
SEM-1
4v/170mA
GDS PRIME
4v/70mA
CAT335C
2.5v/335mA
THE300A
2v/300mA
SS10
2v/175mA
CAT335A
2.5v/335mA
CAT335B
2.5v/335mA
CAT100A
2v/100mA
CAT165
2.2v/165mA
EOL
CAN
4-20
MPU
FAULT
TP1
OV
TP11
TP9
TP5
TP8
TP10
198M1C
ISS M
TP
7
ZERO
ZERO
TP12
DISP
MPU active LED
(Flashing)
Fault LED
Sens V Test Point
TP7 + TP12
Sensor cell input
Sensor Volts
(RV3)
Zero
(RV2)
Span
(RV1)
4mA
(RV4)
Sensor Zeroing LEDs
CAN Transmitting LED
4-20mA SInk/Source
4-20mA Test
Jumper
End-of-line Jumper
Relay/Win Ribbon
LCD Contrast
Win Only
RS232
PC Data In/Out
Win Data Ribbon Cable
4-20op Test Points
FIELD TERMINALS
HI LO
24V Can+ Can- OV 4-20mA
24V Hi
Lo OV 4-20
mA
P
Y
W
Control Unit
CAN 1 or 2
Sensor
Addressable
+24
Hi
Lo
0v
4~20mA
+24
Hi
Lo
0v
Control Unit
4~20mA Input
Sensor
3-Wire Direct
4~20mA Signal
+24
Hi
Lo
0v
4~20mA
+24
Sig
0v
EOL
T
FAULT
MPU
SK
SE
204M1C
ISS M
CONTRAST
Fault LED
Gas Type Header
Sensor cell input
20mA
Span
(RV2)
4mA
Zero
(RV1)
Sensor 4-20mA Routing Configurations
(see diagram)
CAN Transmitting LED
4-20mA Test
Jumper
Relay/Win Ribbon
LCD Contrast
Win Only
End-of-line Jumper
+24V Test Point
(w.r.t 0V)
+24V
RS232
PC Data In/Out
Win Data Ribbon Cable
4-20mA Test Pins
4-20mA Sink Source
External 4-20mA Input
(eg. Infrared)
+24V O/Pt
(eg. Infrared)
FIELD TERMINALS
HI LO
24V Can+ Can- OV 4-20mA
24V Hi
Lo OV 4-20
mA
P
Y
W
Mainboad to Sensor wiring
Sensor Jumper configuration
Control Unit
CAN 1 or 2
Sensor
Addressable
+24
Hi
Lo
0v
4~20mA
4~20 IN
SO
SK
+24
Hi
Lo
0v
Control Unit
4~20mA Input
Sensor
3-Wire Direct
4~20mA Signal
+24
Hi
Lo
0v
4~20mA
+24
Sig
0v
Control Unit
4~20mA Input
Sensor
2-Wire Direct
4~20mA Signal
+24
Hi
Lo
0v
4~20mA
+24
Sig
0v
Control Unit
CAN 1 or 2
Sensor
Addressable 4~20mA Input
+24
Hi
Lo
0v
4~20mA
+24
Hi
Lo
0v
4~20 IN
SO
SK
4~20 IN
SO
SK
4~20 IN
SO
SK
ange
t magnets
Using magnets (set up)
Display
Contrast
Field terminals
Relay PCB
Connector
Display PCB
Connector
Test
Test Pins
24v DC
OV
FLT
OUT
IN
AG
Zero LED
ADDR
4mA
20mA
Sensor
Zero
Sensor Volts
Comms
Port
EOL
Vo
This document is not contractual and the equipment specification may be modified at any time without prior notice.
E:
T:
+44 (0)113 286 0166
GDS TECHNOLOGIES LTD
|
FUSION POINT
|
ASH LANE
|
GARFORTH
|
LEEDS
|
LS25 2GA
|
UK
Technical Sheet ref C893Sv.14
198D1C