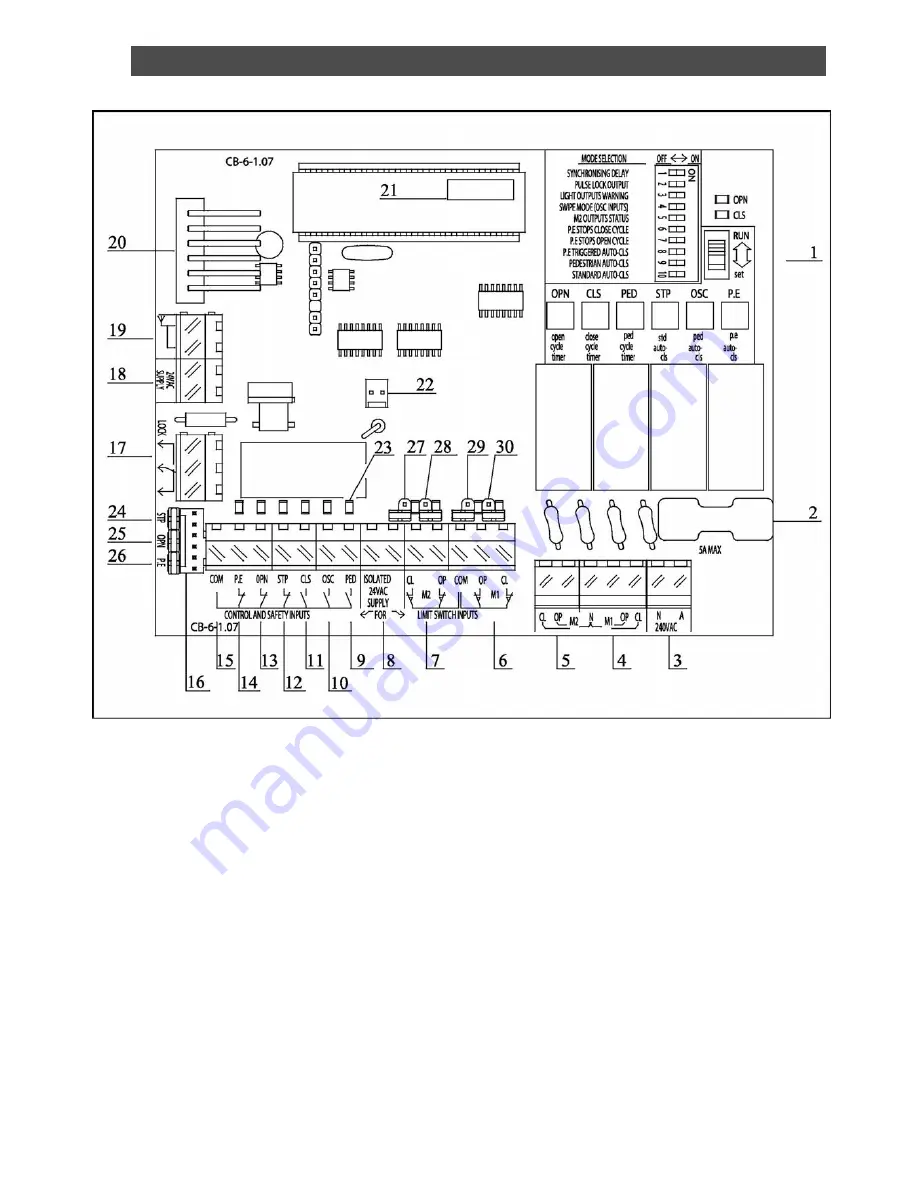
8
CONTROL BOARD LAYOUT FOR INVERTER CONTROLS
1.
Mode Selection and Adjustment
17.
Electric Lock Control Terminals
2.
Protection Fuse
18.
Terminals for 24vAC Supply for
3.
Inverter Input Terminals
Control Logic
4.
Motor 1 Drive Output Terminals for Inverter
19.
Plug In Receiver's Antenna Terminals
5.
Motor 2 Drive Output Terminals for Inverter
With Optional Shield
6.
Motor 1 Limit Switch Inputs
20.
Connector for Plug-In Receiver
7.
Motor 2 Limit Switch Inputs
(no t shown)
8.
Terminals for Isolated 24vAC Supply
21
Firmware Version Label
for Limit Switch and Control Inputs
22
Light Control Relay Interface
9.
Pedestrian Access Control Input
Connector
10.
Open/Stop/Close Control Input
23.
Input Status L.E.Ds.
11.
Close Control Input
24.
Stop Input Jumper
12.
Stop Control Input
25.
Open Input Jumper
13.
Open Control Input
26.
PE Beam Input Jumper
14.
Photoelectric Safety Beam Input
27.
M2 Close Limit Jumper
15.
Common Terminal for Inputs [9]
28
M2 Open Limit Jumper
Thru [14].
29
M1 Close Limit Jumper
16.
Control Input Harness Connector
30.
M1 Open Limit Jumper
Summary of Contents for 450L
Page 7: ...7 Operator Dimensions ...
Page 12: ......