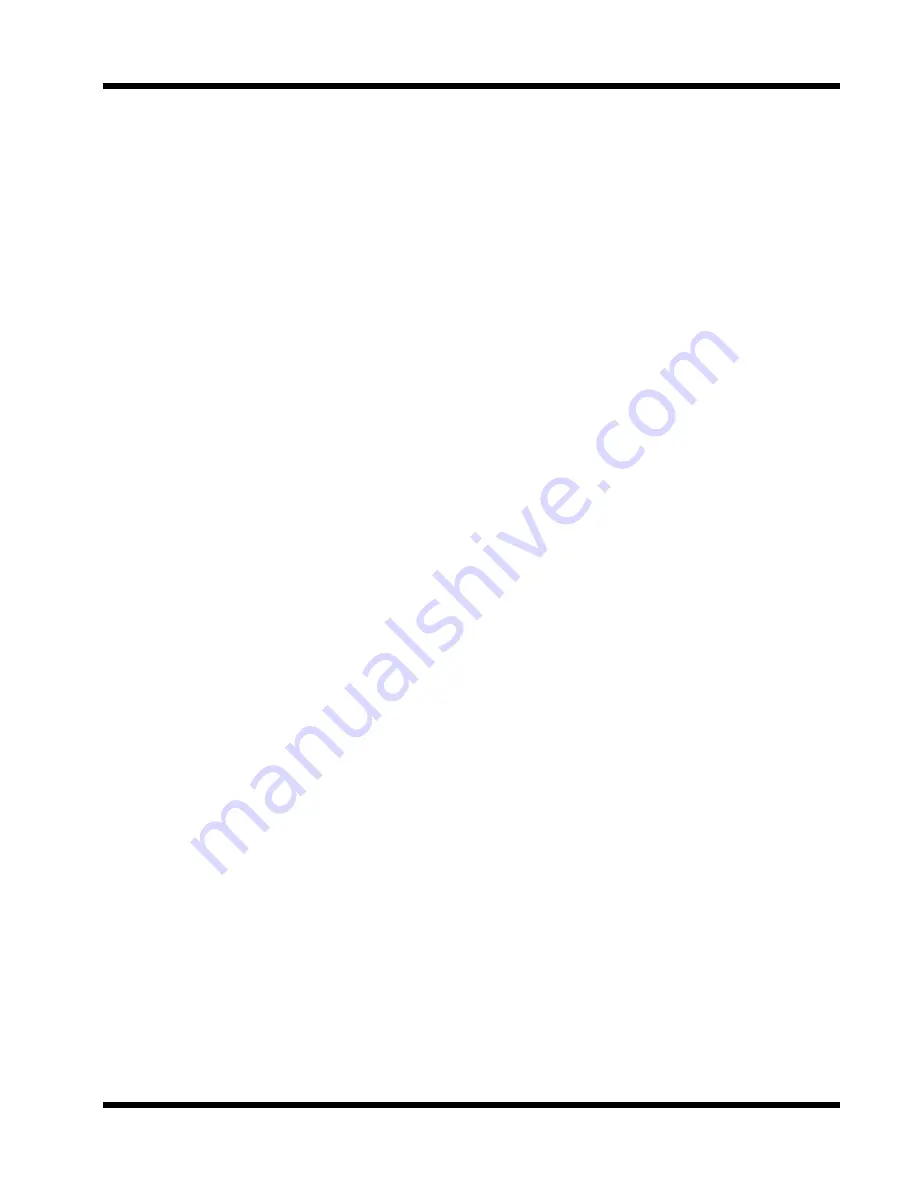
Page 4 - 3
Installation
Orca 80-99 Operation and Maintenance Manual
© GBC Films Group June 2000
7.
Once the ramps are secured and the hold down plates
are removed, the machine can be rolled off the crate
bottom. This will require four people handling the machine
on its four corners and carefully rolling the machine off the
crate bottom (see diagram). The machine can now be
rolled into its final operating position.
Choose a spot with sufficient space around the unit so
that there can be front and back work tables and adequate
space for efficient material flow. Thus, a typical room area
requirement for the ORCA 80-99 is 20 X 24 feet (6.0 x
7.3 Meters) to allow use of work tables in front and to
the rear of the machine. See the suggested layout in Fig.
1-1 (page 4-4).
Once the Orca 80-99 Laminator has been placed in its
final position, optimum performance is obtained by
installing the supplied leveling pads and leveling the
machine. Install one leveling pad on each foot-bolt,
tightening securely.
Lower the leveling pad to the floor by turning down the
foot bolts. Turn all the bolts sufficiently to lift all four of
the casters off the floor.
CAUTION:
Some generation of static electricity is
unavoidable during the laminating process due to
the nature of the materials used. In order to avoid
any hazard of ignition, fire or explosion due to
static spark,
it is imperative that the operating
environment is free of dust, flammable liquids, and
vapors.
Then, face the machine and place a carpenter’s level left-
to-right on one of the idlers. Adjust the bolts on the front
two foot brackets so that the machine is level left-to-right.
Then, move the level to the rear of the machine and adjust
the rear two leveling pads.
Next, place the level front-to-rear on one of the air cylinder
brackets and adjust the bolts equally on the two foot
brackets on that side. Move the level to the other air
cylinder bracket and repeat the procedure for the other
side.
After both sides have been leveled front-to-back, go back
and check the side-to-side level condition of the front
and rear of the machine to insure that it has not changed.
If it has, repeat the procedure until the machine’s front,
rear, and both sides are all level. Tighten the lock nuts
securely to the foot brackets.
8.
At this point a qualified electrician connects power to
the machine. Make sure
before
supply power is provided
that the machine circuit breaker is in the off position. This
is also the point where the appropriate supply of clean,
dry compressed air is connected to the machine (see power
and air requirements).
Electrical Requirements
The ORCA 80-99 is designed to accept 220 to 240-volt
AC, 50/60-Hz, 60 Amps, single phase 3 wire (USA).
The peak power required by the unit is 55 Amperes. Or,
in Europe only 3-N phase 230/400 VAC, 50 Hz, 25
Amps per phase.
Before
attempting to electrically connect or operate your
new Orca 80-99 Laminator, a qualified, licensed electrician
should be consulted to ensure that an adequate power
supply, having the appropriate capacity, overcurrent
protection, safety lockouts, etc., is available; and to ensure
that the power supply of the Orca 80-99 is in accordance
with all established national and regional electrical codes
and standards.
CAUTION:
The air supply to the Orca must be clean and dry
or the machine will be damaged.
GBC Pro-Tech, will not be responsible for damage
to the equipment caused by improper connection,
incorrect power supply or other incorrect electrical
installation.
Before initial power is applied to the machine assure that
all toggle switches on the front and rear control panels
and the main power circuit breaker (inside/bottom of the
left-side cabinet) are set to
OFF
. The AC connection is
located on the bottom/front of the left-side cabinet.