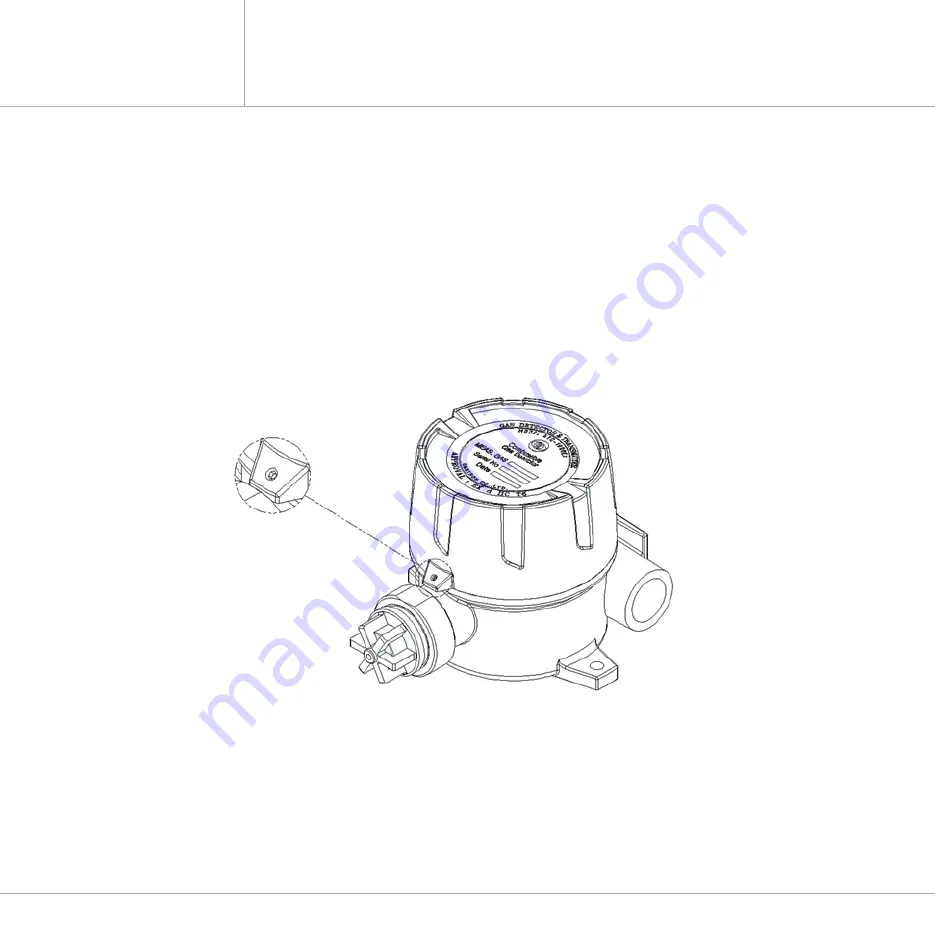
GTD-1000Tx
Instruction Manual
5. Installation
[Figure 3. Slotted Set Screw]
■ It is prohibited for an individual, other than an approved user or a technician responsible for installation and
repair from the head office, to install a gas leak sensor on site or open the cover of the installed gas leak sensor
and manipulate it. This may cause serious loss of life and property from fire, explosion, and etc. In addition,
please check whether there is any remaining explosive gas or combustible material in the surroundings. Power
must be turned off before performing work.
5.1. Detachment of Housing Cover
■ Turn the slotted set screw (M4 x 1ea) fixing the cover part of main body 3~4 turns counter clockwise (ccw) using
a hex wrench (M2) then turn the cover of gas leak detector ccw to detach the cover.