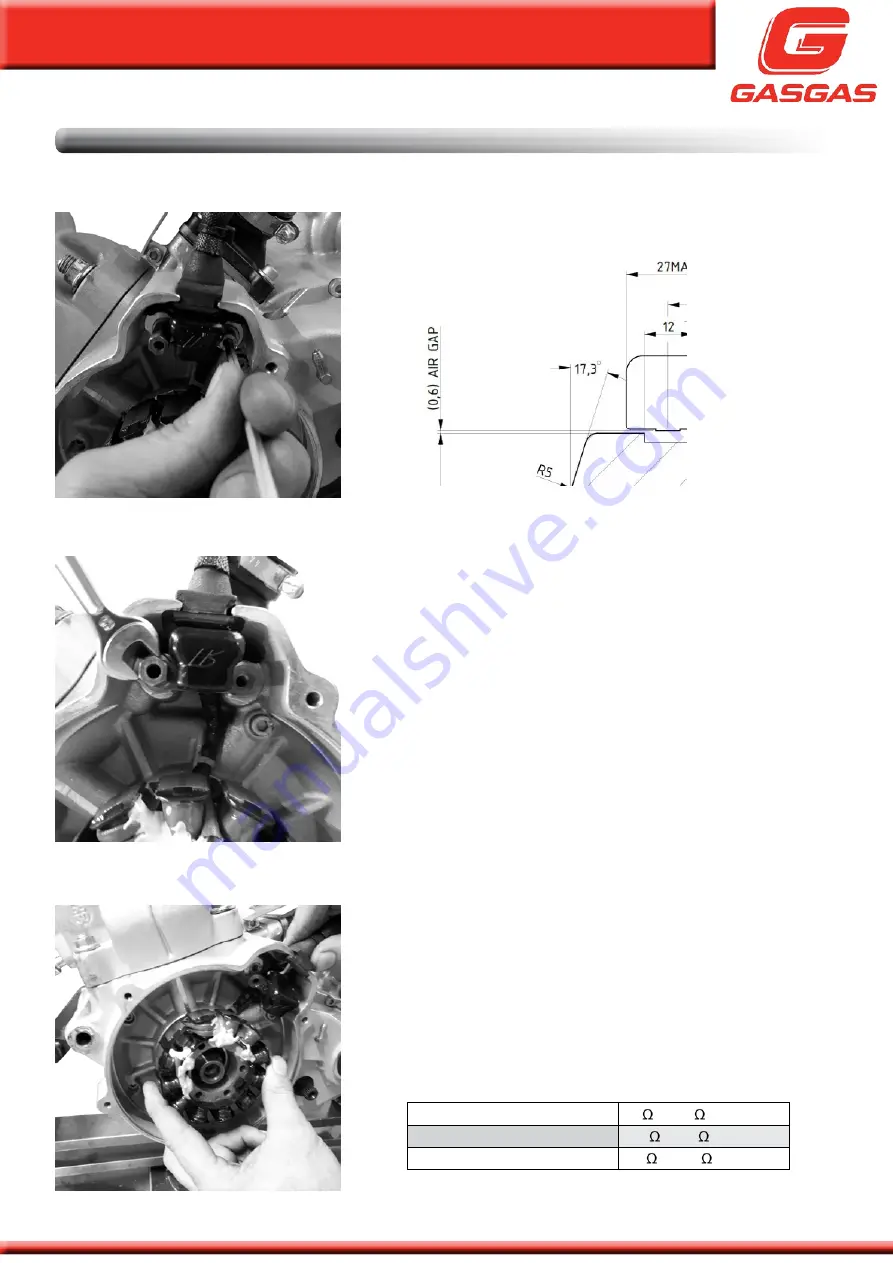
Workshop manual
-40-
- Release the ignition pick-up.
- loosening and extracting the two bolts that secure it to the semi-crankcase.
- once all of the fixing bolts are released, you can remove the stator assembly
and ignition pick-up.
check for proper operation and, in the event of a fault, replace altogether the
component where the problem is located.
- Reassemble the assembly, paying special attention to the condition of the cot
-
ter pin on the end of the crankshaft. Replace if it shows damage.
- To reassemble the components, follow the same steps in reverse.
Starter system disassembly and inspection
generator coil
0.7 +- 0.07
capacitor charging coil
15.8 +- 1.6
Pick Up coil
101 +- 20%
Summary of Contents for TXT 2018 Series
Page 1: ...Trial 80 125 250 280 300cc txt SERIES 2018 Workshop Manual...
Page 4: ...Workshop manual 4 General information...
Page 10: ...Workshop manual 10 SPECIAL TOOLS...
Page 12: ...Workshop manual 12 maintenance...
Page 30: ...Workshop manual 30 Cylinder head disassembly and inspection...
Page 37: ...Workshop manual 37 Starter system disassembly and inspection For models with electric starter...
Page 78: ...Workshop manual 78 Electrical diagrams...
Page 79: ...Workshop manual 79 TXT approved electrical system...
Page 80: ...Workshop manual 80 TXT ignition electrical system...
Page 81: ...Workshop manual 81 CONTACT approved electrical system...
Page 82: ...Workshop manual 82 CONTACT ignition electrical system...
Page 83: ...Workshop manual 83 TXT 80 School electrical system...
Page 84: ......