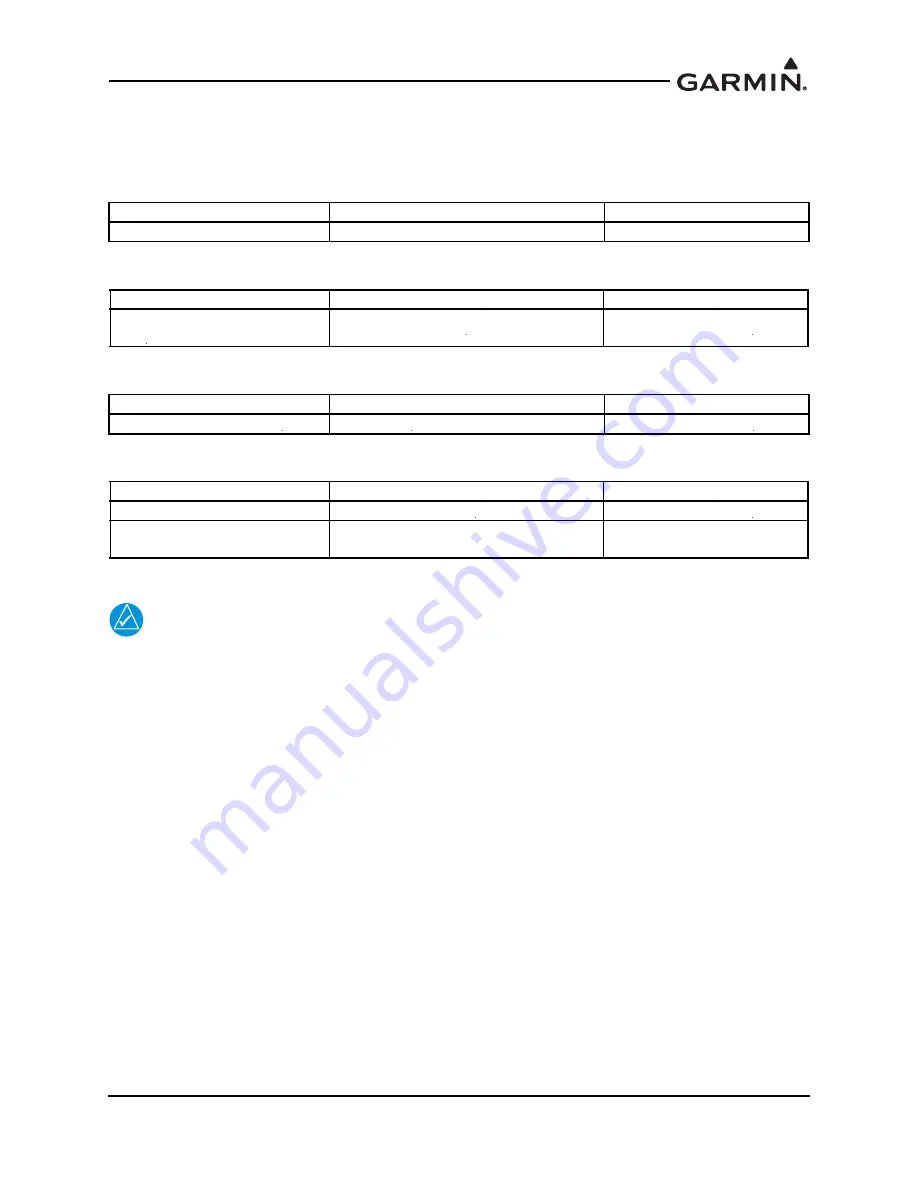
190-00734-17
GTX 335 w/GPS Installation Guidance
Rev. 1
Page 3-3
3.2 Garmin Available Installation Materials
Refer to the tables below for a list of available Garmin standard kit items.
Table 3-1 GTX 335 Connector Kit Options
Table 3-2 GTX 335 Backplate Assembly Options
Table 3-3 GTS 335 Mount Rack Options
Table 3-4 GTX 335 Configuration Module
3.3 Installation Materials Not Supplied
NOTE
The GTX series models are used with standard aviation accessories. Refer to the Acceptable
Hardware appendix for permitted installation hardware that can be necessary but not
supplied. Refer to AC 43.13-1B, Chapter 11, sections 5 through 7 for wire selection and
sizing information.
These items are necessary for installation, but are not supplied:
y
Insulated stranded wire (MIL-W-22759/16 or equivalent)
y
Shielded wire (MIL-C-27500 cable that uses M22759/18 wire (TG) or ETFE jacket (14), or
equivalent)
y
Coaxial cable
y
Aircraft hardware for installation, which includes screws, nuts/nutplates, washers, and rivets (
Refer
to the Acceptable Hardware appendix
)
y
Circuit breaker
y
Tie wraps or lacing cord
y
Ring terminals
y
Shield terminators (MS83519/2-X or equivalent)
y
Silicone fusion tape, A-A-59163 (MIL-I-46852C), or equivalent
y
USB A-to-B cable (for interface between a laptop computer and the GTX 335)
Unit
Item
P/N
GTX 335
Connector Kit
011-02977-00
Unit
Item
P/N
GTX 335 standard mount with
GPS
Backplate assembly
011-02976-01
Unit
Item
P/N
GTX 3X5 standard mount
Install Rack
115-01771-01
Unit
Item
P/N
GTX 335
Configuration Module
011-00979-03
GTX 335
Garmin altitude encoder with
configuration module
011-03080-00