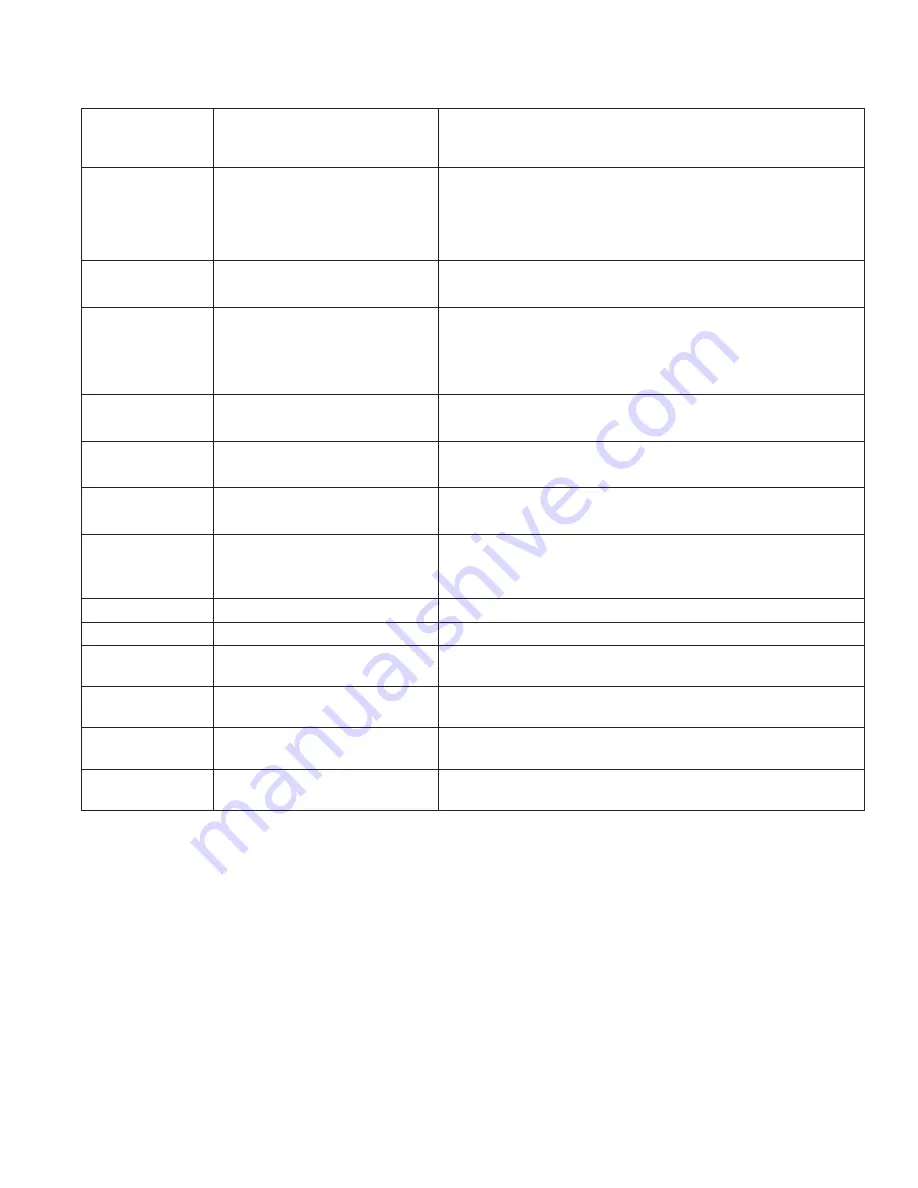
Part # 4521635 (03/04/08)
Page 13
Number Of
Flashing Signals
Error Code
Significance
(Asterisk Refers To Notes At End
Of Chart)
Measures To Take
8
-........-........-........
Sensor error***
a. Check Cu coil
b. Check heat sink sensor
c. Check RTCS-sensor
d. Check board sensor
12
Power reduction, heat sink
temperature **
a. Turn the power level down
b. Check fan
13
Power reduction, temperature of
cooking surface **
CU sensor 1
Warning temperature
a. Take pan off until cooking area has cooled down
b. Wait until it has cooled down
c. Check coil
17
CU sensor 1 over
temperature ***
a. Temperature of the cooking field too high
b. Check CU sensor 1, index value 5 -Ohms at 25°C (77°F)
18
CU sensor 2 over
temperature ***
a. Temperature of the cooking field too high
b. Check CU sensor 2, index value 5 -Ohms at 25°C (77°F)
19
CU sensor 2, high temperature
warning
a. Temperature of the cooking field too high
b. Turn the power down
20
Power reduction generator inside
temperature **
a. Check for heat sources around the generator and remove
them if any
b. Check air circulation
21
Heat sink sensor error ***
a. Contact the factory
24
Board temp. sensor error ***
a. Exchange power unit
25
CU sensor 1 error ***
a. Check CU sensor 1 for short circuit or discontinuation, index
value 5 Ohms at 25°C (77°F).
26
CU Sensor 2 error ***
a Check CU sensor 2 for short circuit or discontinuation, index
value 5 Ohms at 25°C (77°F)
27
Empty cooking detector CU
sensor 1 *
a. Check cooking material in the pan
28
Empty cooking detector CU
sensor 2 **
a. Check cooking material in the pan
* The induction unit can only be restarted by turning the control knob first to the “OFF” position, and then back to
the “ON” position to reset.
** The induction unit continues working
*** The induction unit does not heat.
Summary of Contents for Enodis GIU-1.5 (BH/BA 1500)
Page 23: ...Part 4521635 03 04 08 Page 23...
Page 24: ......