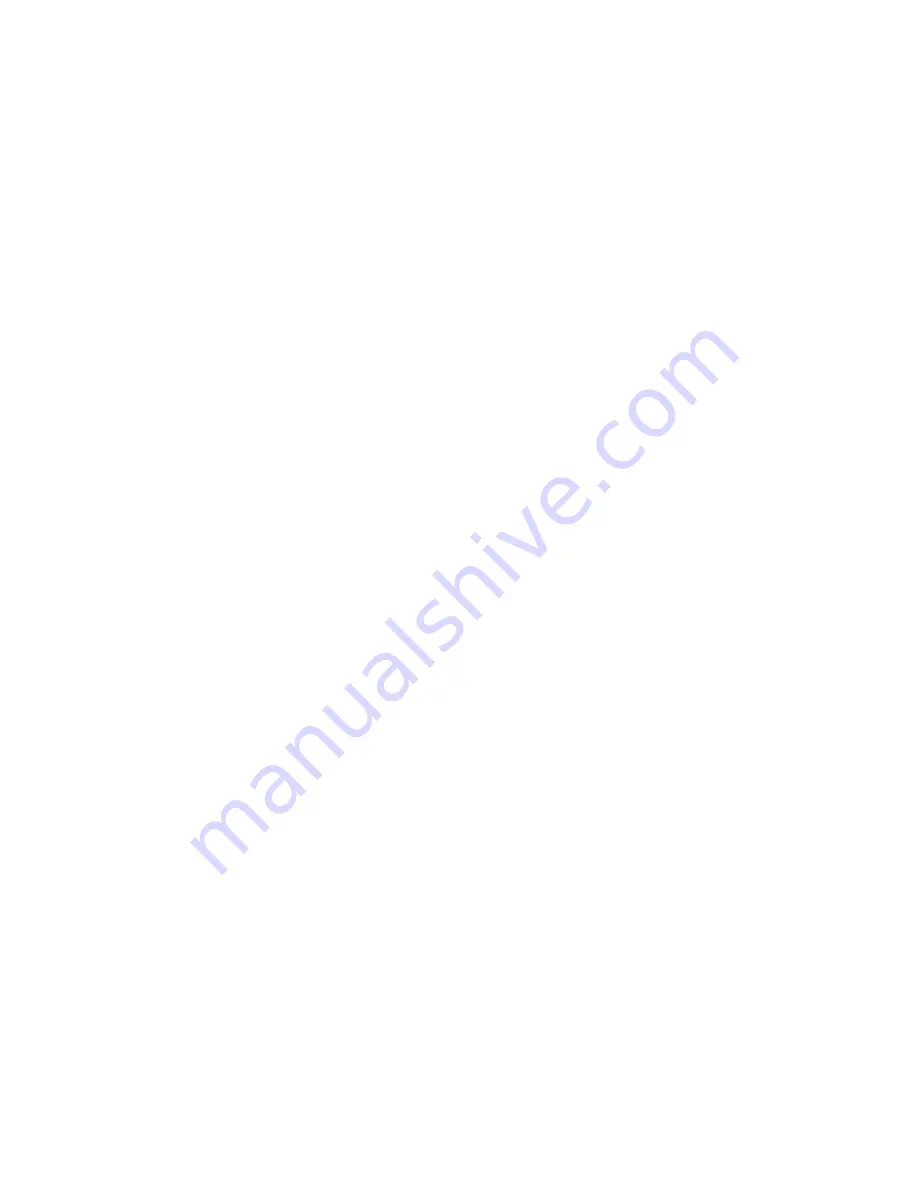
13-17-609 Page 18
2-3
The following set-up steps must be accomplished prior to operating the air-cooled package and its
separate air-cooled module
– Refer to Figures 1-6, page14 and 1-7, page 15 for hardware dimensions
and interconnection details:
·
The module shall be installed close enough to the compressor package such as the oil lines (e.g.,
pipes, hoses) interconnecting both do not exceed a total length of 50 ft.
·
The module shall be installed at grade (e.g., the same elevation) with the compressor package.
·
The end user shall provide the necessary pipes and wiring to interconnect the module to the
compressor package.
o
The air/oil lines shall shall be rated for continuous operation at 220 psig and 250ºF. Steel pipe
that is clean (e.g., no debris or welding slag) and protected against corrosion by a suitable barrier
(e.g., galvanizing) is recommended.
o
The air line nominal size shall be 4in for a max length of 25 ft
– based on the use of five (5) or
less pipe elbows. Flanged connections (150 lb rating) shall be used to interconnect all pipe
segments.
o
The oil line nominal size shall be 2in for a max length of 50 ft. Screwed connections (NPT) may
be used but flanged connections (150 lb rating) are preferred. Provisions for draining the lowest
spot on the oil line shall be made.
o
The interconnecting pipes shall be supported such as no loads are transferred to the connections
of either the compressor package or the module.
o
Communication cable between the module and the compressor package shall be equal or
equivalent to Belden 9841, with a characteristic impedance of 120 ohms
– Refer to Figure 4-7,
page 40 for details.
·
Refer to ELECTRICAL WIRING notes on this section to connect the fan motor VFD to the power
supply.
Air for heat exchanger cooling is drawn in at the cooler end of the module and is exhausted through a top-
side opening. Air for motor cooling, electronics cooling, and for the compressor intake is drawn in at the
controller end of the compressor package and exhausted through three (3) roof vents. Refer to Package
Illustrations on Figure 1-2 to Figure 1-3, pages 10 and 11, for hardware details.
Do not block flow of air entering or exiting either the compressor package or the cooler module
enclosures - allow 3-1/2 feet (1.1 m) clearance to the nearest obstruction all around and on top.
Water Cooled Units
– Separate shell-and-tube coolers for air and oil services are supplied on Water
Cooled packages. The heat exchangers require sufficient cooling water flow to operate efficiently
–
please refer to Section 6 of this manual for detailed instructions on the operation and maintenance of
Water Cooled heat exchangers, including minimum cooling water flow requirements.
Air for motor cooling, electronics cooling, and for the compressor intake is drawn in at the controller end
and exhausted through three (3) roof vents
– refer to Section 6 of this manual for enclosure ventilation
requirements. Refer to Package Illustrations on Figure 1-4 and
Figure 1-5
, pages 12 and 13, for hardware
details.
Do not block flow of air entering or exiting the enclosure - allow 3-1/2 feet (1.1 m) clearance to the nearest
obstruction all around and on top.
FOUNDATION
- The Gardner Denver Rotary Screw compressor and the air-cooled module require
no special foundation, but should be mounted on a smooth, solid surface and as near level as possible.
Temporary installation may be made at a maximum 10
°
angle lengthwise or 10
°
sidewise.
Mounting bolts are not normally required. However, installation conditions such as piping rigidity, angle of
tilt, or danger of shifting from outside vibration or moving vehicles may require the use of mounting bolts
and shims to provide uniform support for the base.