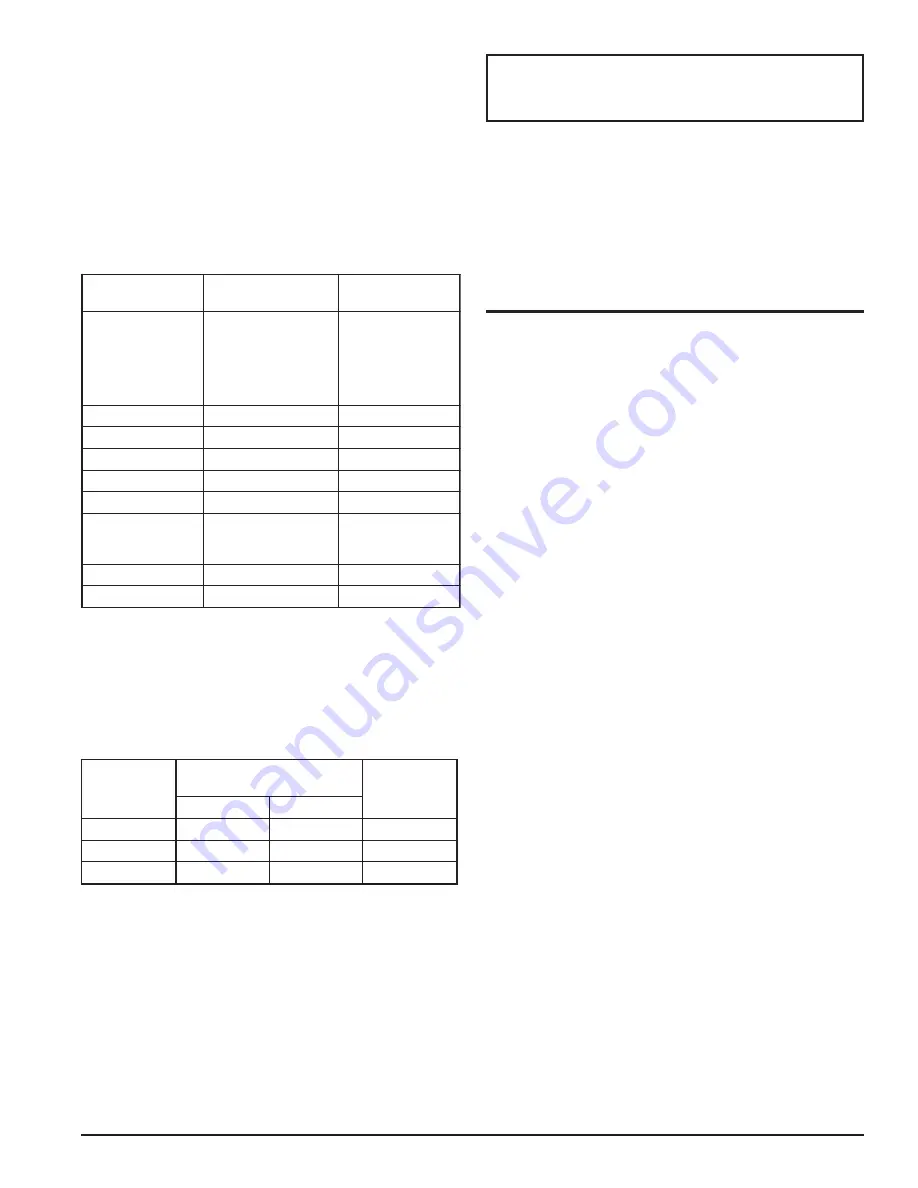
5
Fouling
Biological and organic substances (slime) can also cause
problems, but in elevated temperature environments such
as cooling processes they are not a major concern. If they
create problems with clogging, commercial shock treat-
ments are available.
To ensure continued good operation and performance of
the dryer cooling system, the recommended ranges for dif-
ferent water constituents are shown in Table III.
Table 3
Water Quality Requirements
R
E
T
E
M
A
R
A
P
N
O
I
T
A
R
T
N
E
C
N
O
C
F
O
Y
C
N
E
U
Q
E
R
F
S
I
S
Y
L
A
N
A
y
t
i
v
i
s
o
r
r
o
C
,
H
p
,
s
s
e
n
d
r
a
H
(
d
e
v
l
o
s
s
i
d
l
a
t
o
t
,
s
d
il
o
s
t
a
e
r
u
t
a
r
e
p
m
e
t
)
y
t
i
n
il
a
k
l
a
,
t
e
l
n
i
x
e
d
n
I
r
e
il
e
g
n
a
L
1
o
t
0
y
l
h
t
n
o
M
4
o
t
3
r
o
f
e
l
b
a
t
s
f
I
e
z
y
l
a
n
a
,
s
h
t
n
o
m
y
l
r
e
t
r
a
u
q
n
o
r
I
m
p
p
2
<
y
l
h
t
n
o
M
e
t
a
f
l
u
S
m
p
p
0
5
<
y
l
h
t
n
o
M
e
d
i
r
o
l
h
C
m
p
p
0
5
<
y
l
h
t
n
o
M
e
t
a
r
t
i
N
m
p
p
2
<
y
l
h
t
n
o
M
a
c
il
i
S
m
p
p
0
0
1
<
y
l
h
t
n
o
M
n
e
g
y
x
o
d
e
v
l
o
s
s
i
D
m
p
p
0
)
e
l
b
i
s
s
o
p
s
a
w
o
l
s
a
(
y
l
i
a
D
l
a
r
e
v
e
s
r
o
f
e
l
b
a
t
s
f
I
y
l
k
e
e
w
e
z
y
l
a
n
a
,
s
y
a
d
e
s
a
e
r
g
d
n
a
l
i
O
m
p
p
5
<
y
l
h
t
n
o
M
a
i
n
o
m
m
A
m
p
p
1
<
y
l
h
t
n
o
M
Air-Cooled Models
Cooling air must be drawn from a clean source to reduce
dust and dirt accumulation on the condenser coils. Air tem-
perature (refer to Table 4) should not exceed 100°F.
Table 4
COOLING AIR REQUIREMENTS
R
E
Y
R
D
L
E
D
O
M
G
N
I
T
A
R
R
E
W
O
P
r
o
t
o
M
n
a
F
G
N
I
L
O
O
C
W
O
L
F
R
I
A
¹
)
m
f
c
(
y
t
Q
)
h
c
a
e
(
p
h
0
0
8
1
4
/
1
0
3
8
,
2
0
0
0
1
1
3
/
1
0
0
8
,
2
0
0
2
1
1
2
/
1
0
0
8
,
2
1
Air flows listed represent unrestricted air flow.
Electrical Installation
The dryer data plate lists the electric power requirements
for the dryer.
Confirm that your line voltage is the same as the voltage
listed on the data plate. Provide disconnect and fuses in
accordance with applicable codes. Field wiring must com-
ply with local and national fire, safety and electrical codes.
CAUTION
Operation of dryers with improper line voltage con-
stitutes abuse and could affect the dryer warranty.
Standard dryer enclosures and controls are designed to
meet NEMA Type 1 electrical standards. All wiring is com-
plete. Connect power leads as indicated in electrical sche-
matic and marked in the electrical enclosure. Ground the
frame.
Install a branch circuit disconnect in accordance with the
National Electrical Code and local standards. The discon-
nect must be adequate to handle the starting current.
HOW IT WORKS
Airflow
Energy Saving Cycling dryers use refrigeration cooling to
condense entrained moisture out of the airstream. Warm
saturated air enters an air-to-air heat exchanger, where it
is cooled by outgoing cold air. The inlet air is further cooled
in the glycol chiller (air-to-glycol solution heat exchanger).
Cooling condenses entrained moisture.
The condensate is removed from the airstream by a grav-
ity separator and discharged from the dryer by an auto-
matic drain valve.
The cold air is reheated by incoming warm air as it passes
back through the air-to-air heat exchanger. Using the out-
going air to pre-cool the inlet air condenses up to 65 per-
cent of the moisture out of the inlet air before it reaches the
chiller. Pre-cooling the inlet air reduces the heat load on
the refrigerant compressor, permitting the use of a smaller
refrigerant compressor.
Refrigeration System
The refrigeration system is designed and fabricated in ac-
cordance with recognized commercial/industrial practices.
It consists of a compressor, a compressor motor contactor
and the controls, safety interlocks and associated equip-
ment necessary for safe performance.
A high discharge pressure switch interlocked with the mo-
tor-compressor contactor turns the refrigerant compressor
off if cooling is inadequate. This switch prevents damage
to the compressor and must be manually reset.
The thermal overload switch turns off the compressor in
the event of high motor temperature. This switch is not ac-
cessible. It will automatically reset when the motor has
cooled to an acceptable level. Refer to the Field Service
Guide for causes of and remedies for compressor motor
overheating.
Summary of Contents for RCD800
Page 27: ...27 NOTES...