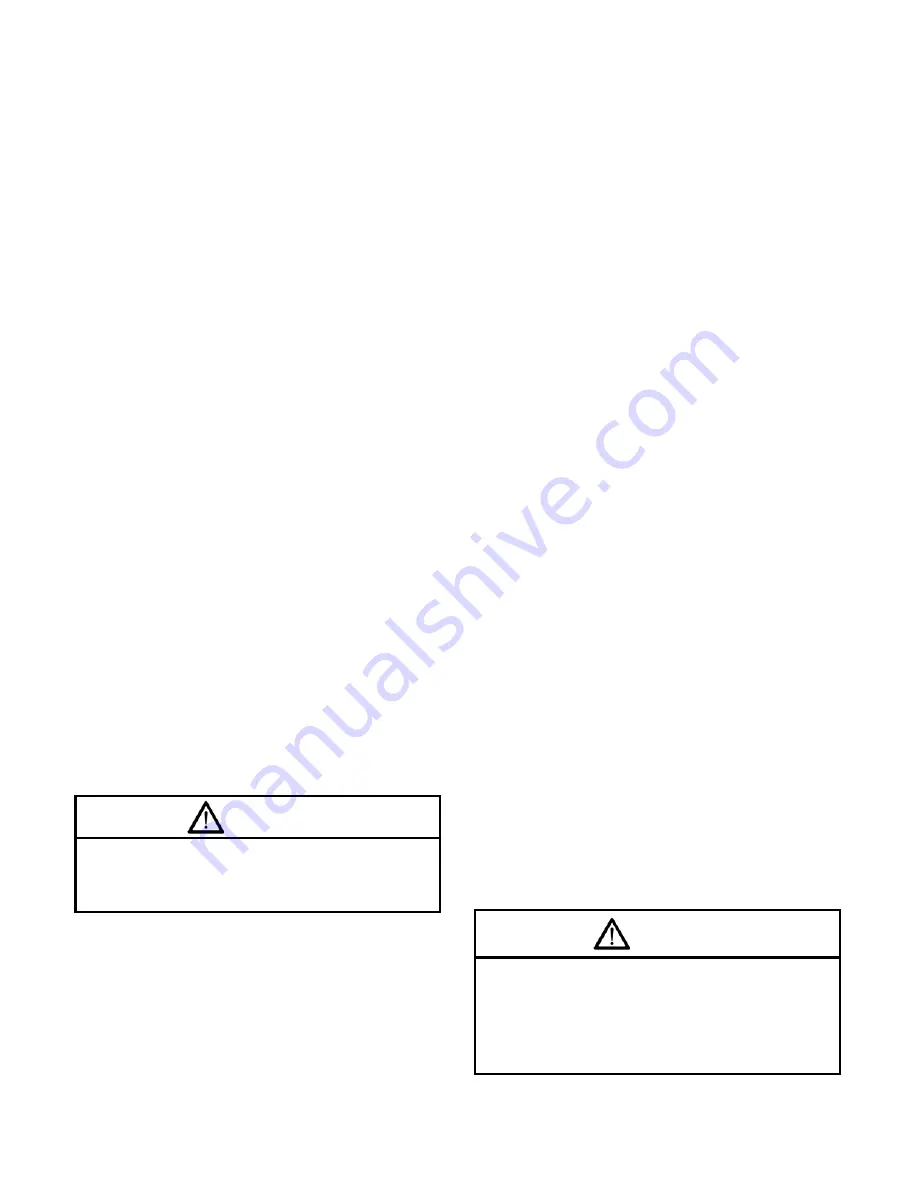
15-600 Page 24
13. Mount shim pack on end of journal and assemble
bearing retainer plate.
14. Force bearing onto shaft taper by tightening cap
screws as evenly as possible.
Bearing retainer plate must be clamped solidly
against shims. It may be necessary to vary
thickness of shim pack slightly to keep internal
running clearances within the recommended
limits.
If excessive torque on retainer plate screws is
required, it may be necessary to resort to
hydraulic assistance. See Item 8 on Page 20.
15
Rotate bearing cartridges in frame so holes for
bearing end plate cap screws line up. The lifting
device shown in FIGURE 15 and FIGURE 16,
page 19, will automatically align holes.
Bearing cartridge must enter bore in frame as
bearing is put on shaft. Use a soft mallet on end of
cartridge if necessary.
16. Remove frame slot spreader jacks. Replace frame
slot spacers. Be certain block to frame keys are in
place. Replace frame slot clamp studs, washer
plates and nuts. Tighten nuts to approximately
500 foot-pounds (69.13 kg-m) only at this time. Be
sure ends of both bearing cartridges are flush with
frame faces.
The end of L.H. bearing may not be flush with the
end of its cartridge as this is the floating bearing.
Plus or minus 1/16” (1.5875 mm), or less, is
satisfactory.
17. Tighten nuts on frame slot clamp studs a
minimum of 1/3 turn total (2 flats). This equals the
torque shown in the Torque Tables on pages 31
and 32.
WARNING
It is important that these studs are
tightened as recommended to prevent
stud and/or frame breakage.
18. Bolt R.H. bearing end plat in place first.
19. Bolt L.H. bearing end plate in place.
20. Assemble the drive pinion on the shaft of the lube
oil pump.
21. Remove all tools and loose parts from the
crankcase. Remove the device use to support the
weight of the eccentric assembly.
22. Replace lube oil pump. Put the hood back in
place. Be sure the gasket is in good condition and
in proper location. Bolt down securely. Use grease
on frame flange to help keep hood gasket in
place.
23. Do not forget to replace or renew the crankcase
oil. Now is a good time for an oil change and a
new filter element to protect the new bearings just
installed.
CROSSHEAD PINS
Procedure For Removal of Outer Crosshead Pins
1.
Cut wire and remove retainer plate to crosshead
cap screws and use these as jack screws in
tapped holes in plate to pull pins. A little
persuasion with a drift driven against the
crosshead body and close to the large end of pin
will help loosen the pin.
Procedure For Removal of Center Crosshead Pin
1.
Remove outer crosshead next to large end of
center crosshead pin to give room to remove pin
from center crosshead. Protect crosshead slide in
frame with a block of wood.
2.
Rotate pump until center crosshead is at end of its
stroke toward fluid cylinder.
3.
Remove center crosshead pin as described above
for the two outer pins.
PUSH RODS
- Push rods can be removed from the
crossheads by working through handhole plates in the
sides of the frame and also through the oil stop
openings after the oil stop head assemblies have been
removed.
Be careful not to damage the highly polished surface
on which oil seals bear.
Push rods are stainless steel and should be protected
when the pump is painted. Paint will damage the oil
stop head seals.
WARNING
Be sure to install the push rods with the
flat side and the word TOP to the top
side of the crosshead for proper
alignment of the push rod, piston rod,
piston and liner.