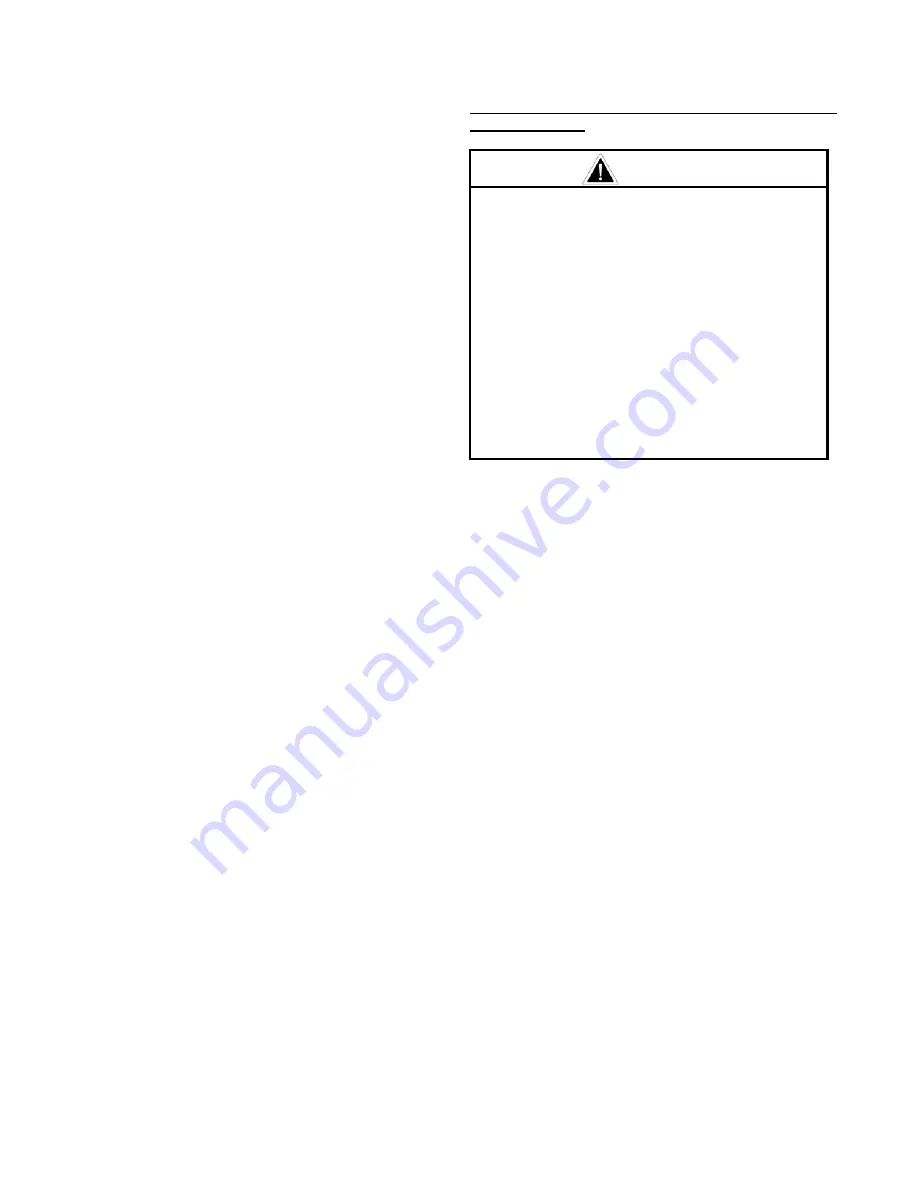
15-600 Page 5
or corrosive fluid leakage from dripping or spraying on
any components, flame, sparks, hot objects or people.
Inspect the plungers, packing, gaskets and seals for
fluid leakage frequently and replace all worn or leaking
parts.
Selection of the proper gaskets, seals and stuffing box
packing is even more critical when flammable, hot, cold
or corrosive fluids are being pumped than when other,
inherently less dangerous fluids are used. Contact a
Gardner Denver service representative for assistance
in selecting the proper gaskets, seals and packing
before beginning operation.
Since some packing weepage into the cradle area is
inevitable, the drain at the bottom of the cradle must be
connected to a drain line which conducts the fluid
leakage to a collection container located in a protected
area. The entire drain system and container must be
constructed of materials resistant to attack from the
pumped fluid or from explosion or fire of the pumped
fluid.
Heavy duty cradle covers must be securely
fastened in the proper position on the pump at all
times when the pump is operating. If the pumped
fluid releases harmful, explosive or flammable
vapors the covers must be vented to conduct the
fumes away from the pump unit to a nonhazardous
area
.
Before beginning pumping operations or starting the
pump power source (whether an engine or electric
motor) check the atmosphere all around the pumping
site for the presence of flammable or explosive vapors.
Do not begin operation and stop ongoing operation if
flammable or explosive vapors are detected. Hot
surfaces, sparks, electric current or engine exhaust
could ignite flammable or explosive vapors. Each
engine used as a power source on pumping units
where flammable or explosive vapors could form
should be equipped with an air inlet shut-off. If
flammable or explosive vapors are present in the
pumping site atmosphere, an engine could continue to
run on these vapors even after the engine fuel line is
shut-off if an air inlet shut-off is not used.
In addition, on pumping units used where flammable or
explosive vapors could form, all electric motors used
as power sources must be of explosion proof
construction and all electrical components and wiring
must meet the current National Electrical Code for
explosive atmospheres.
These precautions must be taken to avoid possible
personal injury, death and/or equipment damage from
explosion, fire or burns.
HIGH PRESSURE LIQUID JETTING, BLASTING
AND CLEANING
DANGER
Extreme caution must be exercised if
any type of wand, gun, nozzle or any
other pressure and flow directing
device is attached to the pump
discharge system for use in jetting,
blasting, cleaning, etc. This type of
equipment must be used with utmost
care by trained, experienced operators.
High pressure fluid streams can either
by direct contact or by propelling loose
objects, cause serious personal injury
or death to the operators and/or other
persons.
Pressure or flow directing devices often receive
pressurized flow through flexible hoses, which can
burst if they are kinked, cut, abraded or are otherwise
worn, damaged or pressured above their rated
capacity. Protect the hose and connections from
damage by people, objects and vehicles. A broken,
cut or otherwise burst hose can release pressurized
fluid which may cause personal injury, death and/or
equipment damage.
High pressure fluid from hand held or hand directed
pressure and flow directing devices may overpower an
operator’s ability to control or direct the device, which
could lead to personal injury, death and/or equipment
damage. The operator must brace against the
backward thrust of a hand held device. In addition, a
safety harness or safety net must be used when
working in an area where the operator could be injured
in a fall. Stand to the side of any tubing or container
being sprayed to avoid back spray and never operate a
hand held device above shoulder level.
Never direct the pressurized fluid stream at yourself or
any other person, control valves, the pump, pump
drive, suction or discharge systems. The pressurized
stream can cause serious personal injury or death and
can also change valve or control settings which could
dangerously increase the delivery pressure to the
pressure and flow directing device.
When operating a pressure and flow directing device,
use only equipment which automatically shuts off flow
when an operator releases hand or foot pressure on
the pressurized flow trigger control to prevent injury if
the operator is overpowered or becomes disabled.