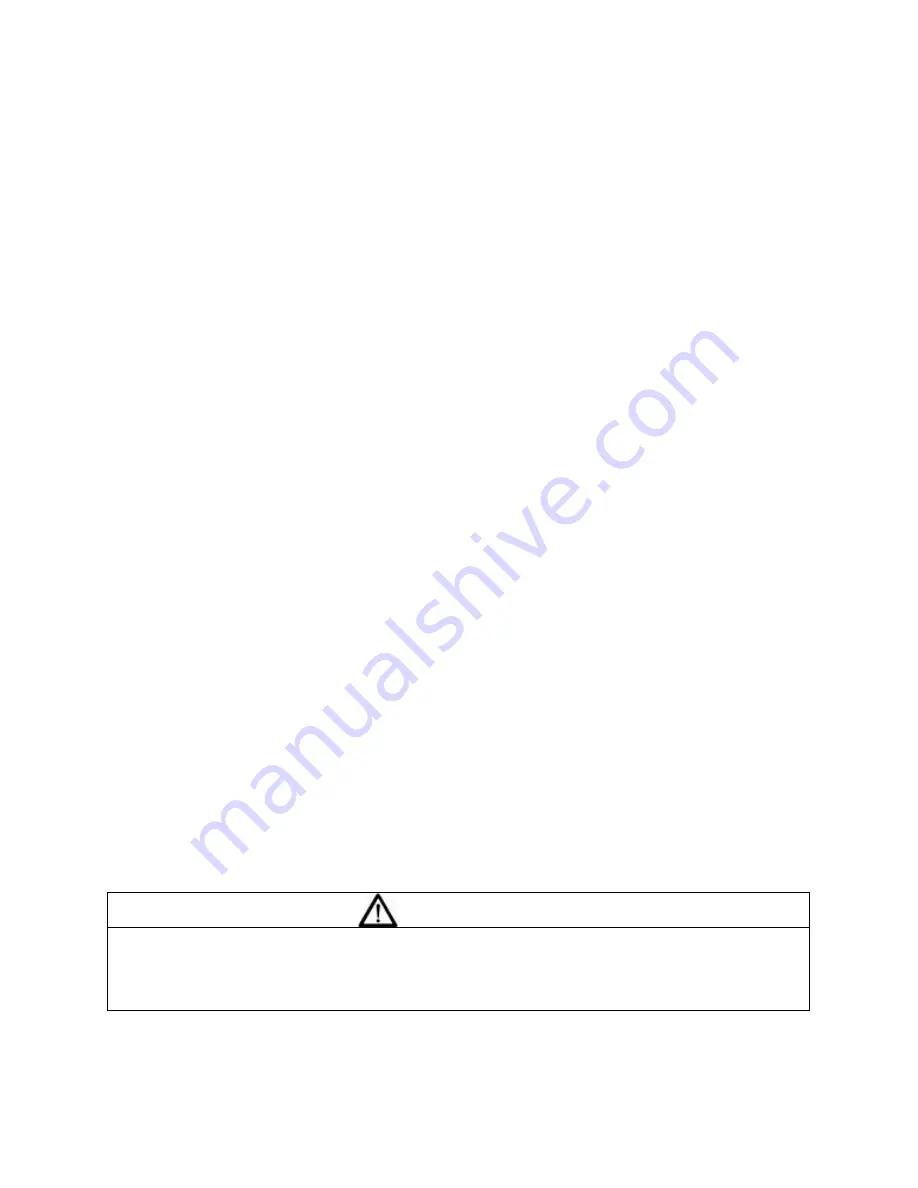
13-11-607 Page 29
If remote control is not desired, this input must be jumpered to operate the compressor. Connect a
jumper between terminals 9 and 31.
Auxiliary Shutdown
- This input allows factory or field connection of shutdown switches not included on
the standard package. Simply connect a two-wire switch to terminals 9 and 31. The switch must be
selected which has contacts closed for normal conditions, and open to shutdown the compressor. If the
contact is opened, the compressor will be shut down, and will display a user selectable message (refer to
unit setup adjustments for list of messages).
If no additional switch is desired, this input must be jumpered to operate the compressor. Connect a
jumper between terminals 9 and 24.
Alarm Relay
- The expansion board is provided with an alarm relay which may be connected to a
remote mounted indicator light, horn, or into a PLC input of a plant wide control system. The contact is
commercial rated 2 amps at 120 volts. The relay is turned on whenever there is a shutdown condition
requiring service at the compressor, and remains off during normal operation, stopping, or power off
conditions. The external connections from the controller are from an isolated form C (single-pole, double-
throw) contact. This allows control of either a ”compressor okay” or a ”compressor shutdown” remote
indicator.
To use this relay, connect the supply wire for the remote circuit to terminal 21 (relay common) on the
terminal strip. Connect a wire to the indicator from either terminal 19 (normally open) or from terminal 20
(normally closed). Connect the other side of the indicator to its neutral.
Serial Communications
– If units are NOT connected in sequence, the RS-485 port may be used for
multi-drop communications of compressor data to external monitoring system. Data available include all
pressures and temperatures, and a report of internal service data. Version 1.10 or later software is
required in the controller. Data communications are accessible with a PC or PLC with an appropriate
communications port. For protocol information, request Drawing 301EWC1255.
OTHER CONTROL DEVICES
In addition to the electronic controller noted above, the following components are also used to control
operation of the compressor unit. Refer to air/water schematic, Figure 1-3, page 3, for their relative
location.
Relief Valve
(vv) - A pressure relief valve is installed in the final discharge line and set to approximately
120-125% of the unit’s full load operating pressure for protection against over pressure. Periodic checks
should be made to ensure its operation.
The relief valve should be tested for proper operation at least once every year. To test the relief valve,
raise the system operating pressure to 75% of the relief valve set pressure and manually open the valve
with the hand lever. Hold the valve open for a few seconds and allow it to snap shut.
WARNING
When the relief valve opens, a stream of high velocity air is released, resulting
in a high noise level and possible discharge of accumulated dirt or other debris.
Always wear eye and ear protection and stand clear of the discharge port when
testing the relief valve to prevent injury.
Summary of Contents for PUREAIR EWC99C
Page 7: ...13 11 607 Page 2 Figure 1 2 PACKAGE ILLUSTRATION 307EWC797 B Ref Drawing...
Page 8: ...13 11 607 Page 3 Figure 1 3 AIR WATER SCHEMATIC 308EWC797 F Ref Drawing...
Page 25: ...13 11 607 Page 20 Figure 4 2 FLOW CHART FOR SETUP PROGRAMMING 300EWC1255 Ref Drawing...
Page 38: ...13 11 607 Page 33 Figure 4 4 WIRING DIAGRAM FULL VOLTAGE 305EWC546 B Ref Drawing Page 1 of 2...
Page 39: ...13 11 607 Page 34 305EWC546 B Ref Drawing Page 2 of 2...
Page 41: ...13 11 607 Page 36 306EWC546 B Ref Drawing Page 2 of 2...