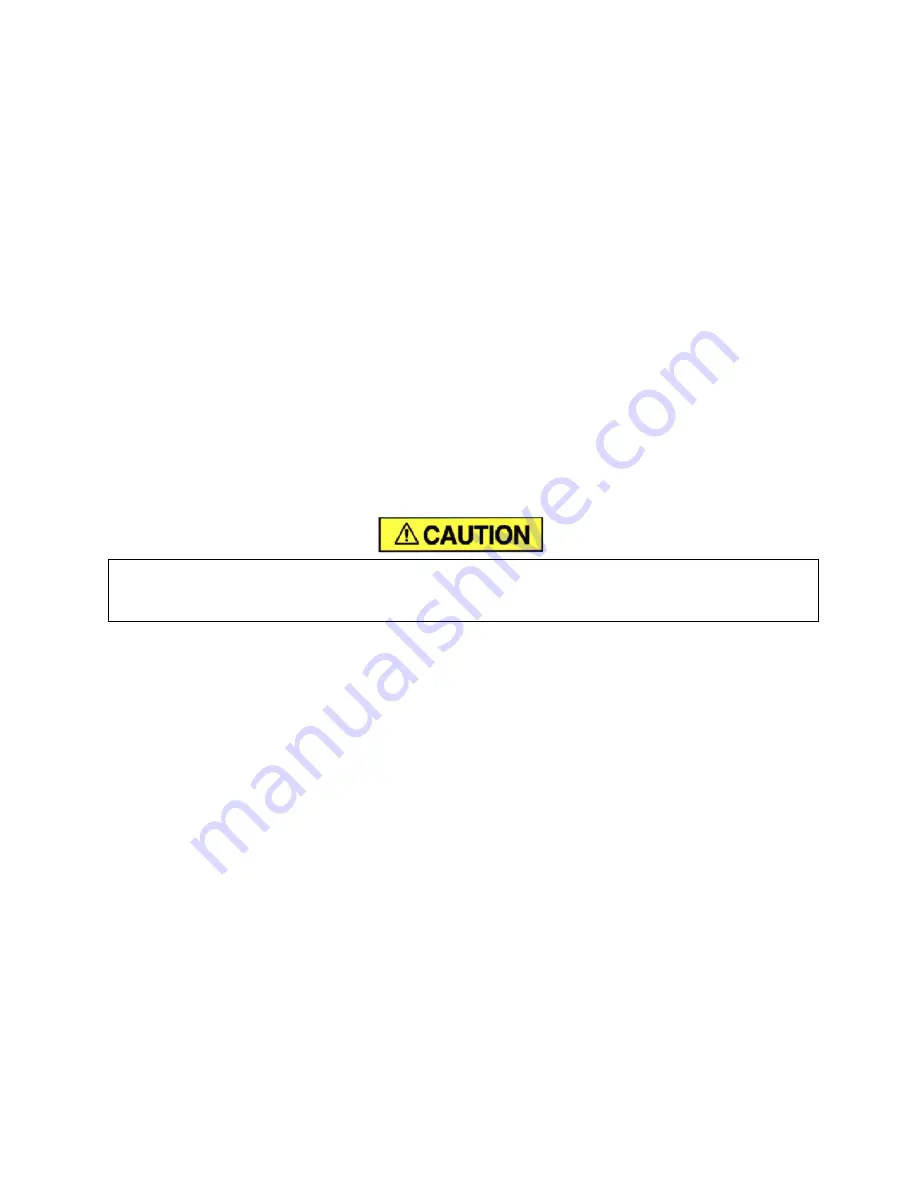
13-25-629 v03 Page 46
AIR / OIL SEPARATOR
- This device provides the final (2%) of the air/oil separation, typically 2ppm oil
content at the final discharge of the compressor package. It is housed in a removable spin-on cartridge.
Its high level of performance may be affected by the following conditions:
Compromised media (e.g., ruptured).
Contaminated media (e.g., vanish, moisture, inadequate oil type).
High oil level in oil sump.
Blockage of oil return orifice.
Abnormally frequent or fast depressurization cycles.
Oil separator element life cannot be predicted; it will vary greatly depending on the conditions of
operation, the quality of the oil used and the maintenance of the oil and air filters. The condition of the
separator can be determined by pressure differential or by inspection.
Separator Pressure Differential
- The pressure drop across the separator is equivalent to the difference
between the two (2) pressure sensors in use:
The pressure differential value may be calculated by subtracting the system pressure value from
the compressor discharge pressure value.
A pressure differential of 8 psi may indicate a moderately dirty element.
A pressure differential of 15 psi may indicate a severely dirty element, replace as soon as
possible.
Using an oil separator element at excessive pressure differential can cause
damage to equipment. Replace the separator when the pressure differential has
reached 15 psi.
OIL FILTER, AIR/OIL SEPARATOR ELEMENT INSPECTION PROCEDURE
1. Remove the spin-on element.
2. Clean the gasket seating surface of the head.
3. Inspect the element internals by shinning a light unto the media surface. If signs of contamination
(dirt, rust, varnish, etc.) or damage is evident, replace the element.
4. Before reassembly, coat the element gasket with the same lubricant used in the unit.
5. Screw on until gasket makes contact. Hand tighten 1/3 to 1/2 turn extra.
6.
Run the unit and check for leaks.
Summary of Contents for L4-5C
Page 27: ...13 25 629 v03 Page 27 FIGURE 4 5 WIRING DIAGRAM 380V 60 Hz 303ECA546 B Ref Drawing Page 1 of 3...
Page 28: ...13 25 629 v03 Page 28 FIGURE 4 6 WIRING DIAGRAM 380V 60 Hz 303ECA546 B Ref Drawing Page 2 of 3...
Page 29: ...13 25 629 v03 Page 29 FIGURE 4 7 WIRING DIAGRAM 380V 60 Hz 303ECA546 B Ref Drawing Page 3 of 3...
Page 30: ...13 25 629 v03 Page 30 FIGURE 4 8 WIRING DIAGRAM 575V 305ECA546 A Ref Drawing Page 1 of 3...
Page 31: ...13 25 629 v03 Page 31 FIGURE 4 9 WIRING DIAGRAM 575V 305ECA546 A Ref Drawing Page 2 of 3...
Page 32: ...13 25 629 v03 Page 32 FIGURE 4 10 WIRING DIAGRAM 575V 305ECA546 A Ref Drawing Page 3 of 3...
Page 61: ...13 25 629 v03 Page 61 Figure 9 5 Compressor Module Hardware...