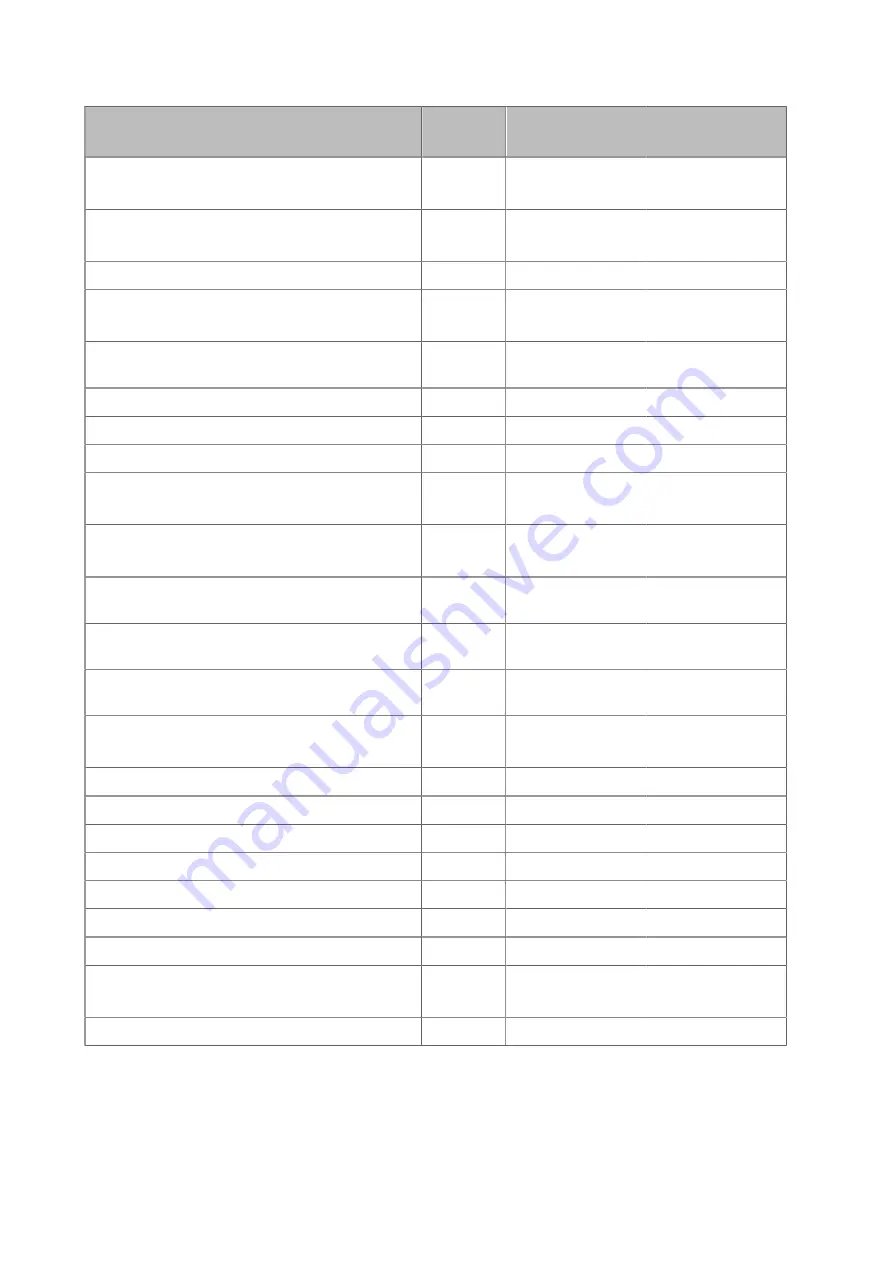
L90 RS,
50Hz, air-cooled "A” + water-cooled "W"
L90 RS,
Aftercooler outlet temperature above ambient
temperature
"A" = [°C]
"W" = [°C]
7
9
Sound pressure level (ISO 2151)
**)
"A" [dB(A)]
"W" [dB(A)]
72 / 74 (50Hz) ; 72 / 75 (60Hz)
72 / 74 (50Hz) ; 72 / 75 (60Hz)
Rated speed of drive motor
[kW]
90
Total current consumption during load operation
(380V) / (400V) / (460V)
"A" [A]
"W" [A]
189 / 179 / 156
186 / 176 / 153
Electric motor
IP55 (IE3) - IEC
60034-2-1 ECA Qualifying
Rated speed of drive motor
[rpm]
650 / 2200
Rated speed of fan motor
"A" [kW]
2.6
Rated speed of fan motor
"W" [kW]
0.37
Recommended cable cross-section (380 / 400 /
460V)
"A" [mm
2
]
"W" [mm
2
]
3 x 70 PE50 / 3 x 70 PE35 /3 x 50 PE25
3 x 70 PE35 / 3 x 70 PE35 /3 x 50 PE25
Recommended fuse rating (time-delayed) (380 /
400 / 460V)
"A" [A]
"A" [A]
3 x 224 / 3 x224 / 3 x 200
3 x 224 / 3 x200 / 3 x 200
Cooling air volume flow
"A" [m
3
/
min]
223 (50Hz) ; 197 (60Hz)
Cooling air volume flow
"W" [m
3
/
min]
100
Cooling air outlet temperature above ambient
temperature
"A" [°C]
27
Residual pressure at ambient temperature
"A" [Pa]
110 / 80 (50Hz) [35 °C / 45 °C]
90 / 70 (60Hz) [35 °C / 45 °C]
Cooling water quantity (ΔT = 17 K)
"W" [l/min]
90 @ Δp = 0.8 bar
Cooling water inlet temperature
"W" [°C]
min. 5 / max. 35
Cooling water outlet temperature
"W" [°C]
max. 55
Cooling water pressure
"W" [bar]
max. 10
Cooling water connections
"W"
EN 10226-1 Rp 11/4 (DIN 2999-R 1 1/2)
Total oil quantity
[l]
63
Compressed air connection
EN 10226-1 R 2 1/2 (DIN 2999-R 2 1/2)
Weight
[kg]
"A" = 2579
"W" = 2405
Dimensions L x W x H
[mm]
2290 x 1327 x 2039
Chart 9-7: Technical data; L90 RS, 50Hz + 60Hz, air-cooled "A", water-cooled "W"
*)
Data measurement and specification as per ISO1217 fourth edition, Appendix C & E and under the following con-
ditions:
Air suction pressure: 1 bar a / 14.5 psia
Air suction temperature: 20°C / 68°F air humidity: 0% (dry)
Summary of Contents for L110 10A V4
Page 73: ......