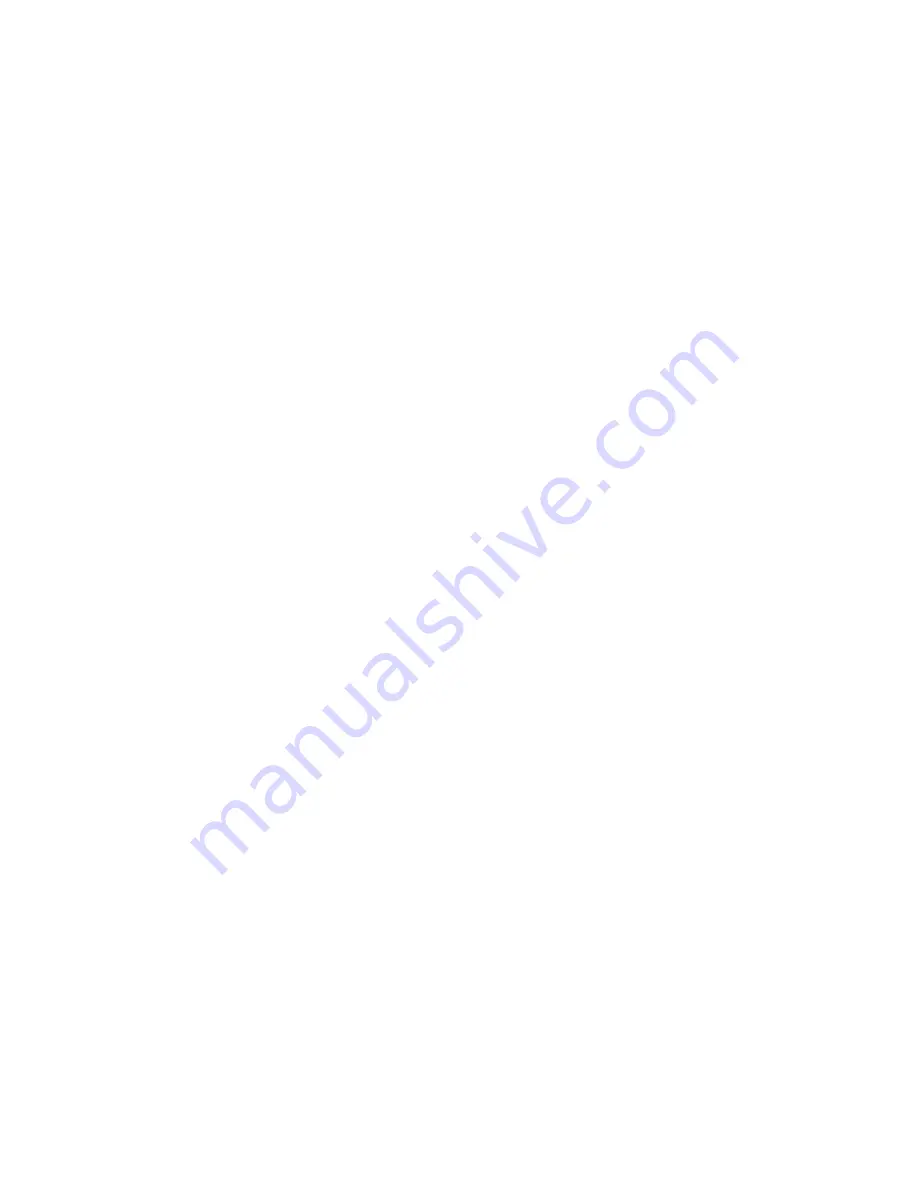
13-20-604 Page 1
MAINTAIN COMPRESSOR RELIABILITY AND PERFORMANCE WITH
GENUINE GARDNER DENVER
®
COMPRESSOR PARTS AND SUPPORT SERVICES
Gardner Denver
®
Compressor genuine parts, manufactured to design tolerances, are developed for optimum
dependability – specifically for Gardner Denver compressor systems. Design and material innovations are the result
of years of experience with hundreds of different compressor applications. Reliability in materials and quality
assurance is incorporated in our genuine replacement parts.
Your authorized Gardner Denver Compressor distributor offers all the backup you’ll need. An AirSmart
™
network of
authorized distributors provides the finest product support in the air compressor industry.
Your authorized distributor can support your Gardner Denver air compressor with these services:
1. Trained parts specialists to assist you in selecting the correct replacement parts.
2. Factory warranted new and remanufactured rotary screw airends. Most popular model remanufactured
airends are maintained in stock at the Remanufacturing Center in Indianapolis, IN., for purchase on an
exchange basis with liberal core credit available for the replacement unit.
3. A full line of factory tested AEON™ compressor lubricants specifically formulated for use in Gardner Denver
compressors.
4. Repair and maintenance kits designed with the necessary parts to simplify servicing your compressor.
Authorized distributor service technicians are factory trained and skilled in compressor maintenance and repair. They
are ready to respond and assist you by providing fast, expert maintenance and repair services.
For the location of your local authorized Gardner Denver Air Compressor distributor, refer to the yellow
pages of your phone directory, check the Gardner Denver Web Site at www.gardnerdenver.com or contact:
Gardner Denver
1800 Gardner Expressway
Quincy, IL 62305
Phone: (217)
222-5400
Fax: (217)
224-7814
INSTRUCTIONS FOR ORDERING REPAIR PARTS/REMANUFACTURED AIRENDS
Whenever an airend requires replacement or repair, Gardner Denver offers an industry unique, factory
remanufactured airend exchange program. From its modern Remanufacturing center in Indianapolis, IN., Gardner
Denver is committed to supplying you with the highest quality, factory remanufactured airends that are guaranteed to
save you time, aggravation and money
When ordering parts, specify Compressor MODEL, Method of Cooling, POWER and SERIAL NUMBER (see
nameplate on unit). The Airend Serial Numbers are also stamped on top of the discharge bearing carrier castings.
All orders for Parts should be placed with the nearest authorized distributor.
Where NOT specified, quantity of parts required per compressor or unit is one (1); where more than one is required
per unit, quantity is indicated in parenthesis. SPECIFY EXACTLY THE NUMBER OF PARTS REQUIRED.
DO NOT ORDER BY SETS OR GROUPS.
To determine the Right-Hand and Left-Hand side of a compressor, stand at the motor end and look toward the
compressor. Right-Hand and Left- Hand are indicated in parenthesis following the part name, i.e. (RH) and (LH),
when appropriate.
Summary of Contents for INTEGRA EFD99E
Page 11: ...13 20 604 Page 10 Figure 1 2 COMPRESSOR ILLUSTRATION 300EFD797 B Ref Drawing ...
Page 30: ...13 20 604 Page 29 Figure 4 3 WIRING DIAGRAM FULL VOLTAGE 308EDE46 A Ref Drawing Page 1 of 2 ...
Page 31: ...13 20 604 Page 30 308EDE46 A Ref Drawing Page 2 of 2 ...
Page 32: ...13 20 604 Page 31 Figure 4 4 WIRING DIAGRAM WYE DELTA 309EDE546 A Ref Drawing Page 1 of 2 ...
Page 33: ...13 20 604 Page 32 309EDE546 A Ref Drawing Page 2 of 2 ...
Page 34: ...13 20 604 Page 33 Figure 4 5 WIRING DIAGRAM LESS STARTER 310EDE546 A Ref Drawing Page 1 of 2 ...
Page 35: ...13 20 604 Page 34 310EDE546 A Ref Drawing Page 2 of 2 ...
Page 59: ......