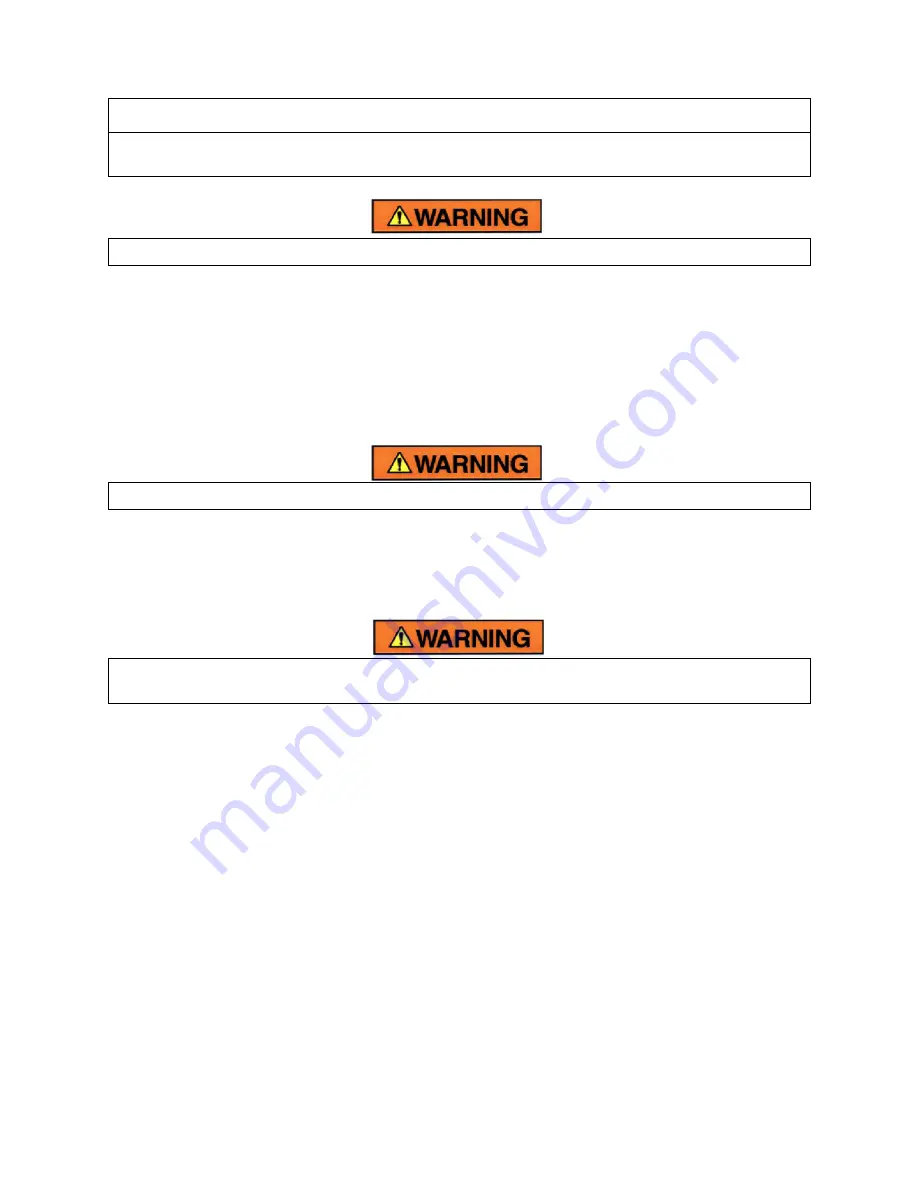
HF-7-602 Page 14
NOTICE
When changing mounting configuration, it will be necessary to reposition oil level gauge (H),
and drain plug (A). Refer to
FIGURE 3-1
, page 17, for correct location.
For Vertical Models, the oil slinger must be on the lower rotor or blower failure is immediate.
DRIVE INSTALLATION
When selecting a V-belt drive, check to be sure the shaft overhung load limitation is not exceeded. Refer
to FIGURE 2-3, page 15, for overhung load calculations and limitations.
Belt drives must be carefully aligned. Motor and blower pulleys must be parallel to each other and in the
same plane within 1/32 inch. Belt tension should be carefully adjusted to the belt manufacturer
’s
recommendation using a belt tension gauge. Check tension frequently during the first day of operation.
Over tightening belts leads to heavy bearing loads and premature failure.
On the direct connected units, alignment and lubrication of couplings to specifications of the coupling
manufacturer is very important. When mounted drives are supplied from the factory, proper alignment
has been established before shipment. However, during shipping, handling and installation, it is likely
that the alignment has been disturbed and final adjustment must be made before startup.
Exceeding overhung load limitations leads to unwarrantable premature bearing failure and shaft
breakage.
The location of the sheave on the blower shaft greatly affects the stress in the shaft. The optimum blower
sheave positioning is as close as possible to the blower drive cover, not to exceed dimension
“C” in Drive
Shaft Illustration, FIGURE 2-3, page 15.
The calculated shaft moment must not exceed the maximum allowable moment listed in Maximum
Allowable Moment Chart, FIGURE 2-3, page 15. If the calculated shaft moment exceeds the maximum
allowable moment:
•
Increase Sheave Diameters to Reduce Belt Pull
•
Use Jackshaft Drive
•
Use Direct Coupled or Gearbox Drive
To calculate shaft moment for a given V-Belt Drive Arrangement:
1.
Use the formula for Calculation of Belt Pull, FIGURE 2-3, page 15, to calculate belt pull.
Refer to Arc of Contact Factor Chart, FIGURE 2-3, page 15.
2.
Insert the calculated belt pull into the formula for Calculation of Shaft Moment,
FIGURE 2-3, page 15 to arrive at the calculated shaft moment.
Summary of Contents for Industrial Series
Page 27: ...HF 7 602 Page 26 Figure 5 5 FALSE BEARING EQ144211 5...
Page 29: ...HF 7 602 Page 28 Figure 5 8 HAND CRANK EQ144211 8...
Page 30: ...HF 7 602 Page 29 Figure 5 9 MECHANICAL SEAL DRIVER EQ144211 9...
Page 31: ...HF 7 602 Page 30 Figure 5 10 FALSE BEARING SPACER EQ144211 10...
Page 44: ...HF 7 602 Page 43 SECTION 8 PARTS LIST HYEL_AA 300HYE810 D Ref Drawing...
Page 55: ...HF 7 602 Page 54 SECTION 10 PARTS LIST HYEL_AB 301HYE810 B Ref Drawing...
Page 58: ......
Page 59: ......