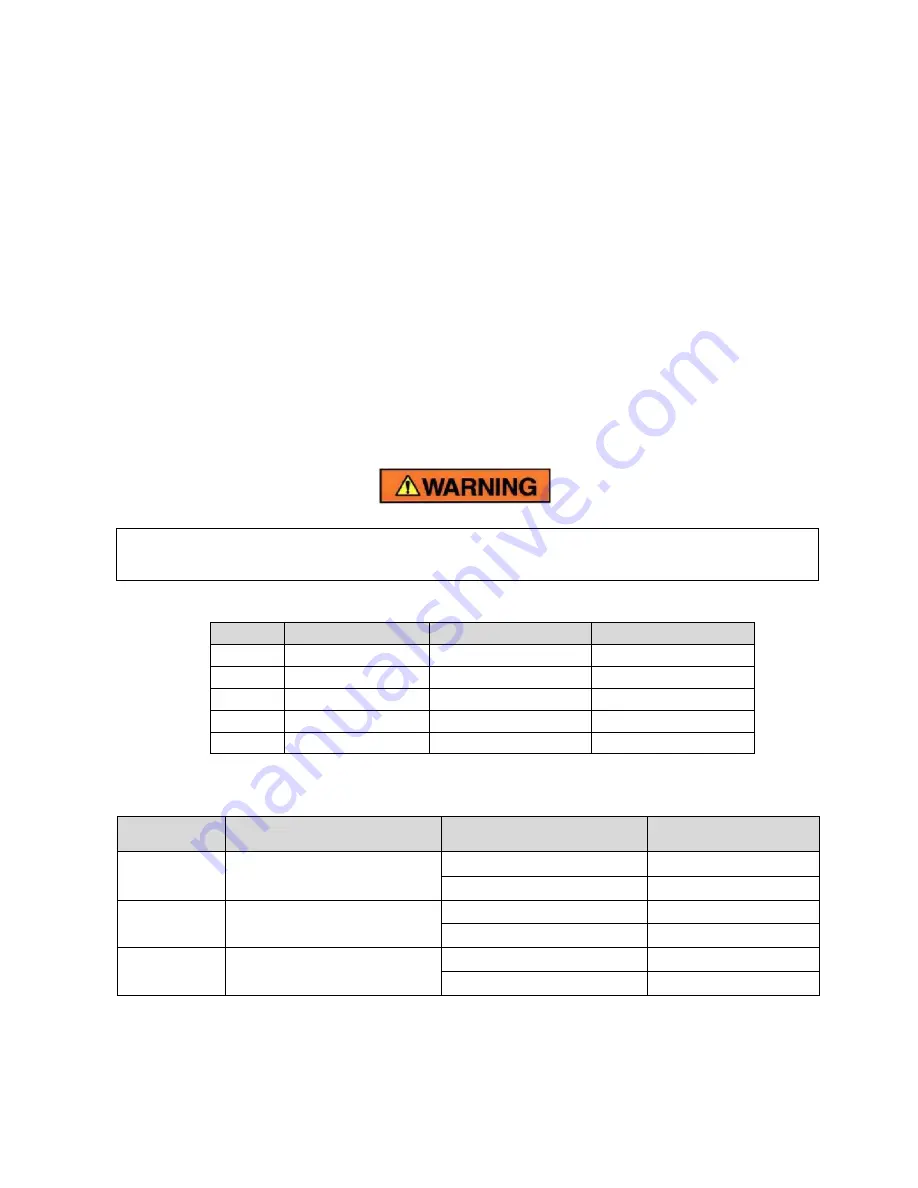
13-21-616 v00 Page 21
MOTOR LUBRICATION
- Long time satisfactory operation of an electric motor depends in large measure
on proper lubrication of the bearings. The following charts show recommended grease qualities and re-
greasing intervals for ball bearing motors. For additional information refer to the motor manufacturer’s
instructions. The following procedure should be used in re-greasing:
1.
Stop the unit.
2.
Disconnect, lockout and tagout the unit from the power supply.
3.
Remove the relief plug and free hole of hardened grease.
4.
Wipe lubrication fitting clean and add grease with a hand-operated grease gun. Refer to the table
below for the proper amount of grease to add to each bearing. All bearings are factory filled with Mobil
Polyrex EM.
5.
Leave the relief plug temporarily off. Reconnect the unit and run for about 20 minutes to expel the
excess grease.
6.
Stop the unit. Replace the relief plug.
7.
Restart the unit.
MOTOR GREASE AMOUNTS
HP/kW
Motor Enclosure Front Bearing (grams) Rear Bearing (grams)
5/3.7
TEFC
10
10
125/90
ODP / TEFC
40
35
150/110
ODP / TEFC
40
35
200/150
ODP
40
35
200/150
TEFC
45
35
ELECTRIC MOTOR REGREASING INTERVAL
Type of
Service
Typical
Rating
Relubrication Interval
Standard
One or Two Shift Operation
Up to 150 HP (112 kW)
18 Months
Above 150 HP (112 kW)
12 Months
Severe
Continuous Operation
Up to 150 HP (112 kW)
9 Months
Above 150 HP (112 kW)
6 Months
Very Severe Dirty Locations, High Ambient
Temperature
Up to 150 HP (112 kW)
4 Months
Above 150 HP (112 kW)
2 Months
Rotating machinery can cause injury or death. Open main disconnect, lockout
and tagout power supply to starter before working on the electric motor.