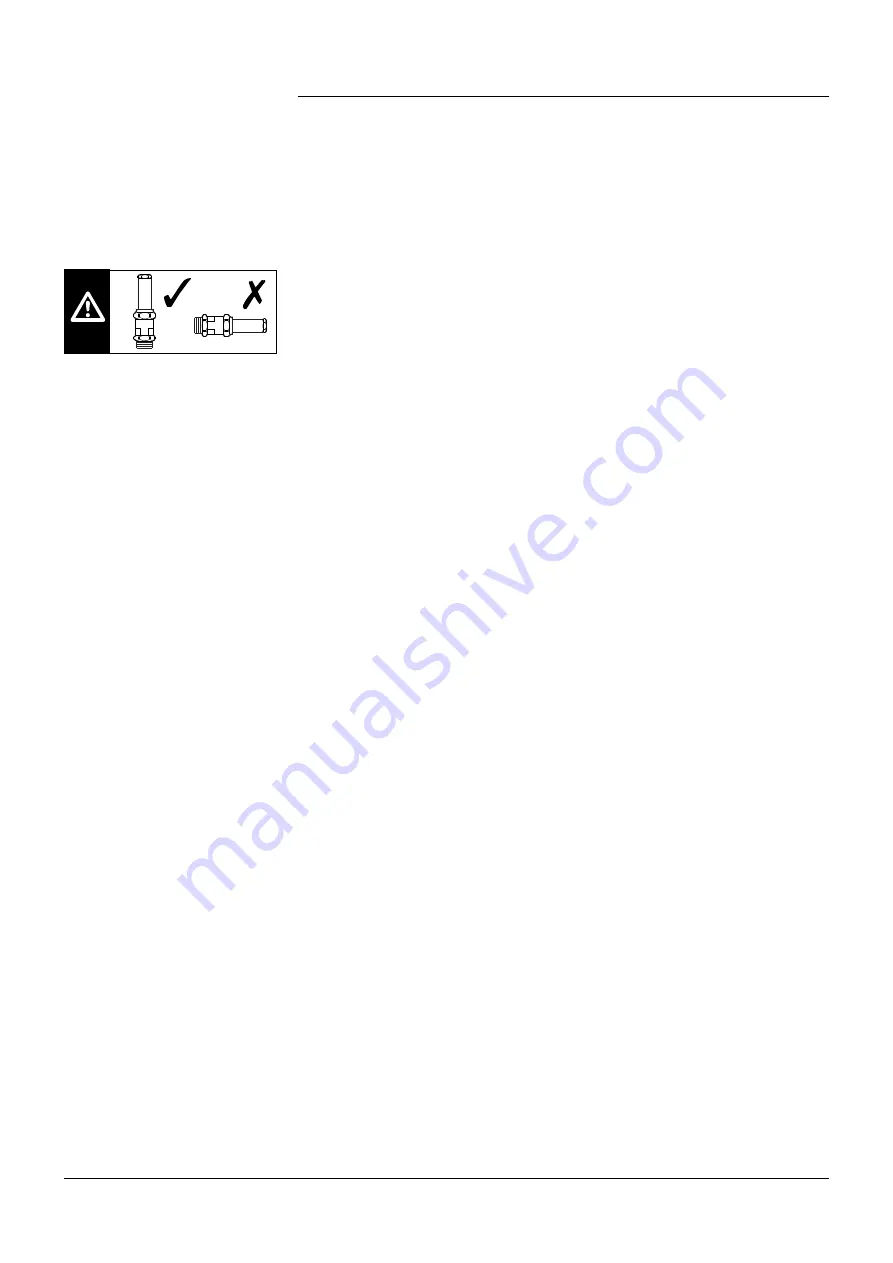
Page 13
4990140010 Date:03/15
XK12 Installation, Operating & Maintenance Manual
Page 13
4990140010 Date:03/15
XK12 Installation, Operating & Maintenance Manual
Installation
3.8 Ancillaries
(relating to fi gures 10a - 10b)
Inlet Air Filter and Flexible Induction Kit
Should be located so that the inlet air is cool and clean. Do not mount close to exhausts or
other warm air sources. Ensure screw-on cuff s are sealed onto inlet hose using suitable high-
temperature silicone sealant, such as DOW CORNING Silicone AP.
Relief Valve
The relief valve is installed to prevent the XK12 from encountering pressures beyond its
operating range.
The relief valve should be installed as close as possible to the discharge port of the machine
prior to any other discharge ancillary and should be mounted vertically (as shown in fi g 10 ).
It is pre-set, wired and leaded (tamper proof ) and fi tted to protect the XK12 (rather than the
system which should be protected by the vehicle tank relief valve) against pressures of over
2.5bar g . Adjustment of the machine relief valve will invalidate the XK12 and relief valve
warranty.
Discharge Silencer
Should be mounted/connected as close as possible to the discharge port (after the relief valve)
utilising the slip-on-weld fl anges supplied.
Silencers should be mounted/supported separately to prevent the generation of loads on
the machine and discharge port due to weight or temperature expansion. Flexibility in the
mounting or connecting pipe work to the silencer should be incorporated where this could
occur.
Check (non-return) valve
This is to prevent a back-fl ow of air and product (often encountered when stopping
compressors whilst the discharge tank is still pressurised) from entering and damaging the
XK12.
The check valve should be the last ancillary on the discharge pipework (but before any regular
disconnection point) to protect all the other ancillaries. It is often mounted directly to the
delivery port of the discharge silencer.
If the check valve has to be mounted horizontally on the silencer or separately, the check valve
hinge should be positioned at the top in horizontal pipe work to encourage closure under
gravity. If mounted vertically, the position of the check valve hinge is not important.
Torque Coupling
We recommend and supply a torque-limiting device for fi tting to the compressor when direct
PTO driving.
This is to protect all the drive-line equipment against the possibility of high torque during
operation for any circumstances.
Expansion Joints
Any pipe work or equipment should incorporate fl exible elements where:
• Movement due to thermal expansion is likely
• Pipe work crosses the vehicle chassis.
Ball Valve
A 1“ - 1.5” manual ball valve must be fi tted on the discharge side of the machine between the
compressor discharge port and the check valve.
This allows the compressor discharge air to vent to atmosphere to prevent the machine being
started against a pressurised tank.
Comissioning Filter
See section 3.7
Fig 10. Relief valve orientation