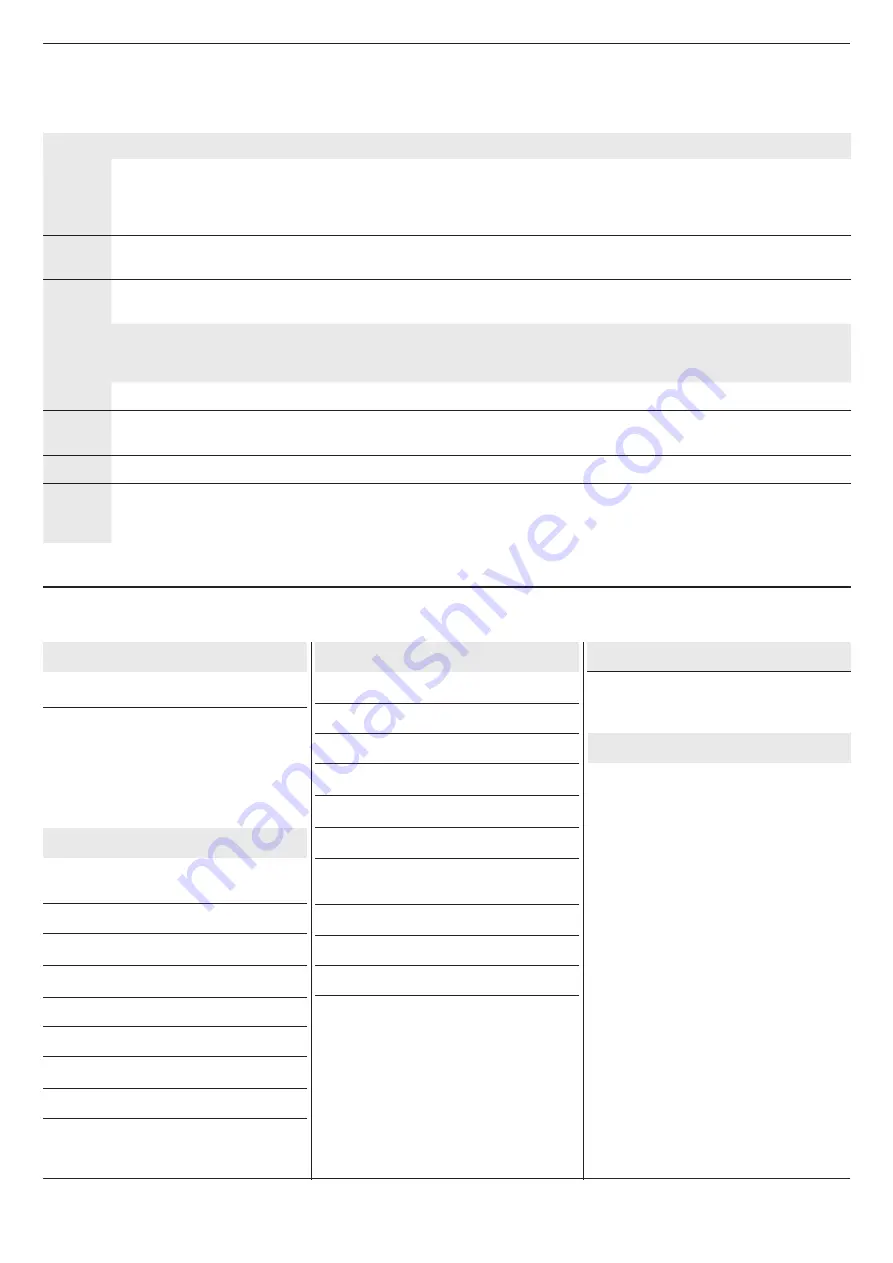
9
4.1 PROGRAMMING WITH MECHANICAL LIMIT SWITCH
ATTENTION
: to let the safeties work, these must be connected
before
starting the control unit setup.
Setup process - Mechanical limits standard
1
Set DIP10 in OFF position for selecting mechanical limits and DIP1 and DIP2 to OFF position for deadman operation.
Standard control for mechanical limits are for PNE edge type (3-4 terminals on X5) and no photo connected.
ATTENTION: Switching DIP10 to ON position and back to OFF will reset to mechanical standard with ONLY PNE edge
type.
2
Press OPEN or CLOSE to the desired close and open limit position and adjust cam until the limit is correct.
Note: if door is moving in the wrong direction the 2 phases on the mains connection must be interchanged.
3
Limits are now adjusted.
Check that the safety edge is working (if mounted).
Setting process - Mechanical limits with other safety connected
ATTENTION: additional safeties as OSE (connected to X5 5-6-7) or photocell (connected to X6 9-10-11-12)
will be active only after the setting process
4
Make setup process 1 and 2 and move the door away from close limit.
5
Connect the requested safeties.
Activate setting by pressing OPEN+STOP for about 10 sec then release. The red LED FAIL (PCB) start with 2 short flashes
6
Press STOP to stop setting the edge type and photo. Yellow LED SPEED/SER confirming with 1 sec
7
Limits are now adjusted and edge type and photo circuit are memorised. Check that the safety functions are working as
expected.
ATTENTION: moving DIP10 to ON position and back to OFF will reset to mechanical standard with ONLY PNE edge type.
Yellow LED CONF./SER. (PCB)
Fixed light
Service needed (open
counts reached)
1 sec. flash
Confirming learning
process
Green LED POWER (PCB)
Fixed light
The controller is powered
Red LED CIRCUIT ERROR (PCB)
Fixed light
PCB circuit error fail
Red LED FAIL (PCB)
Fixed light
If Photo or Edge is activated
when CLOSE pushbutton is
activated
1 long flash
Auto close learning active
2 short flashes
Limits, edge and photo not
learned
2 long flashes
Force control (speed) not
learned
3 long flashes
Door stopped by force control
4 long flashes
Door stopped by runtime
5 long flashes
Door stopped by force control
wear
6 long flashes
Tacho failure – pulses missing
Continues long
flashes
Fail state PNE edge monito-
ring. Check impuls by floor
missing.
Yellow LED STOP (PCB)
Fixed light
Stop activated or both limits
are active
1 long flash
Safety chain activated
2 long flashes
Photo – safety test failed.
3 long flashes
Safety edge – safety test
failed.
4 long flashes
Stop circuit – safety test
failed.
5 long flashes
Safety chain – safety test
failed
6 long flashes
EEPROM failure. Elec.
Counter or position counter by
force control
7 long flashes
EEPROM failure. Powerup
failure
8 long flashes
Welded contactor fail
9 long flashes
Internal watchdog timeout.
10 long flashes
Main processor crystal fail
4.2 LED GUIDANCE