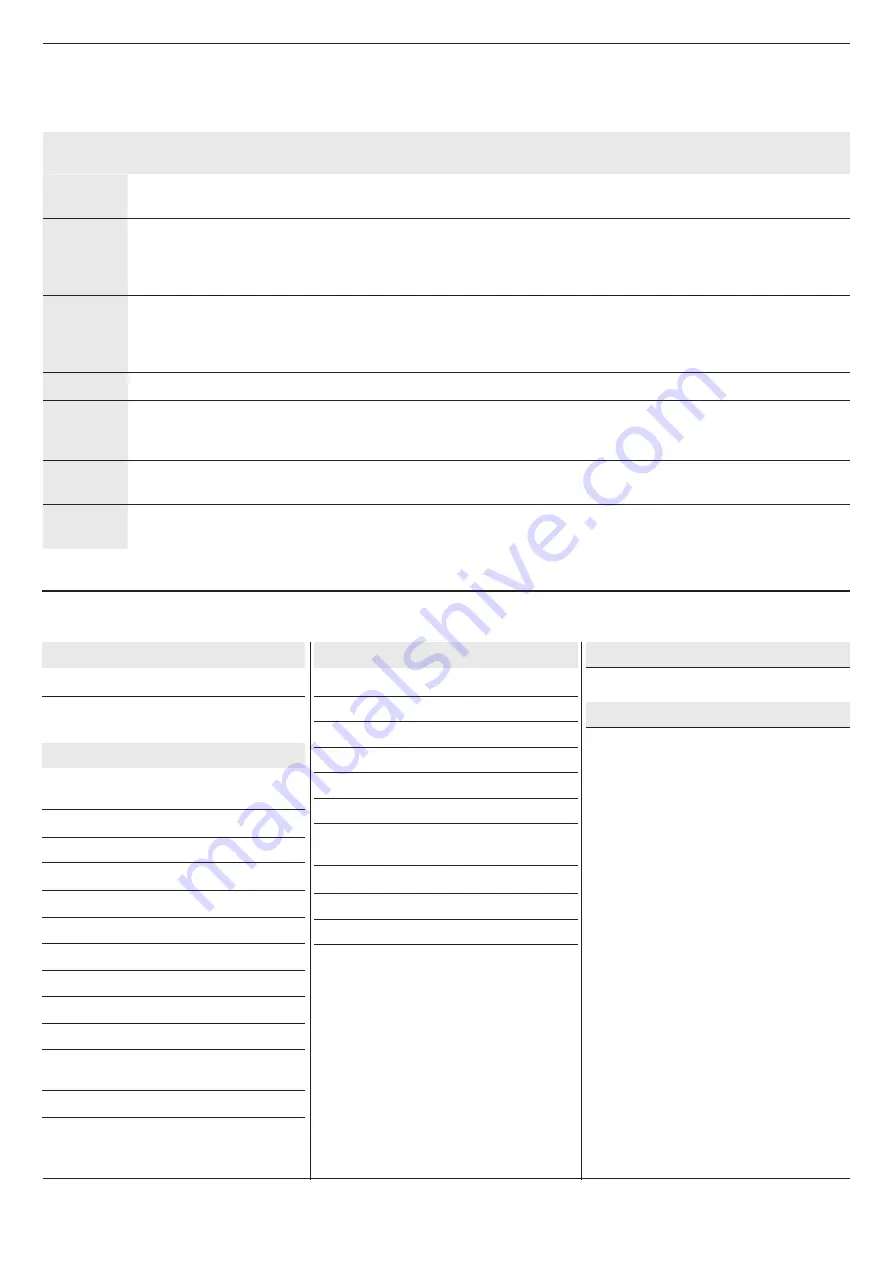
11
Setting process
1
Turn OFF the power and connect the encoder and all safety equipment.
The controller memorises the encoder type by power-up.
2
Set DIP10 in ON position and turn the power ON. Activate setting by pressing OPEN + STOP for about 10 sec until the
red LED FAIL (PCB) starts with 2 short flashes
ATTENTION: Switching DIP10 to ON position and back to OFF will reset to mechanical standard with ONLY PNE edge
type.
3
First press the CLOSE button to the desired down limit position.
Note: if door is moving in the wrong direction the 2 phases on the mains connection must be interchanged.
(Alternatively choose the special phases interchange function by pressing OPEN + STOP for 20 sec. - Yellow LED SPE-
ED/SER confirming with 1 sec.)
4
Press STOP to set the down limit position. Yellow LED SPEED/SER confirming with 1 sec
5
Press OPEN to the desired UP limit position.
By open position you can adjust the UP limit position finely by running OPEN and CLOSE, but first operation must be in
OPEN direction for minimum 2 sec.
6
Press STOP button to save the UP limit position, encoder direction,
edge type and photo
Yellow LED SPEED/SER confirming with 1 sec
7
Limits are now adjusted and edge type and photo circuit are set.
Check that the safety edge and photo functions are working as expected.
Yellow LED CONF./SER. (PCB)
Fixed light
Service needed (open
counts reached)
1 sec. flash
Confirming setting process
Green LED POWER (PCB)
Fixed light
The controller is powed
Red LED CIRCUIT ERROR (PCB)
Fixed light
PCB circuit error fail
Red LED FAIL (PCB)
Fixed light
If Photo or Edge is activated
when CLOSE pushbutton is
activated
1 short flashes
No answer from encoder.
Check RS485
1 long flash
Auto close setting active
2 short flashes
Limits, edge and photo not
learned
2 long flashes
Force control (speed) not
learned
3 long flashes
Door stopped by force control
4 short flashes
Calculation failure (e.g. both
limits the same)
4 long flashes
Door stopped by runtime
5 long flashes
Door stopped by force control
wear
6 long flashes
Tacho failure – pulses missing
7 short flashes
Encoder position out of learned
area. (Reset by power up or
resetting)
8 short flashes
Kostal encoder – Power
failure.
Continues long
flashes
Fail state PNE edge monito-
ring. Check impuls by floor
missing.
Yellow LED STOP (PCB)
Fixed light
Stop activated or both limits
are active
1 long flash
Safety chain activated
2 long flashes
Photo – safety test failed.
3 long flashes
Safety edge – safety test failed.
4 long flashes
Stop circuit – safety test failed.
5 long flashes
Safety chain – safety test failed
6 long flashes
EEPROM failure. Elec. Counter
or position counter by force
control
7 long flashes
EEPROM failure. Powerup
failure
8 long flashes
Welded contactor fail
9 long flashes
Internal watchdog timeout.
10 long flashes
Main processor crystal fail
5.2 LED GUIDANCE
5.1 PROGRAMMING WITH ELECTRONIC LIMIT SWITCH
ATTENTION
: to let the safeties work, these must be connected
before
starting the control unit setup.