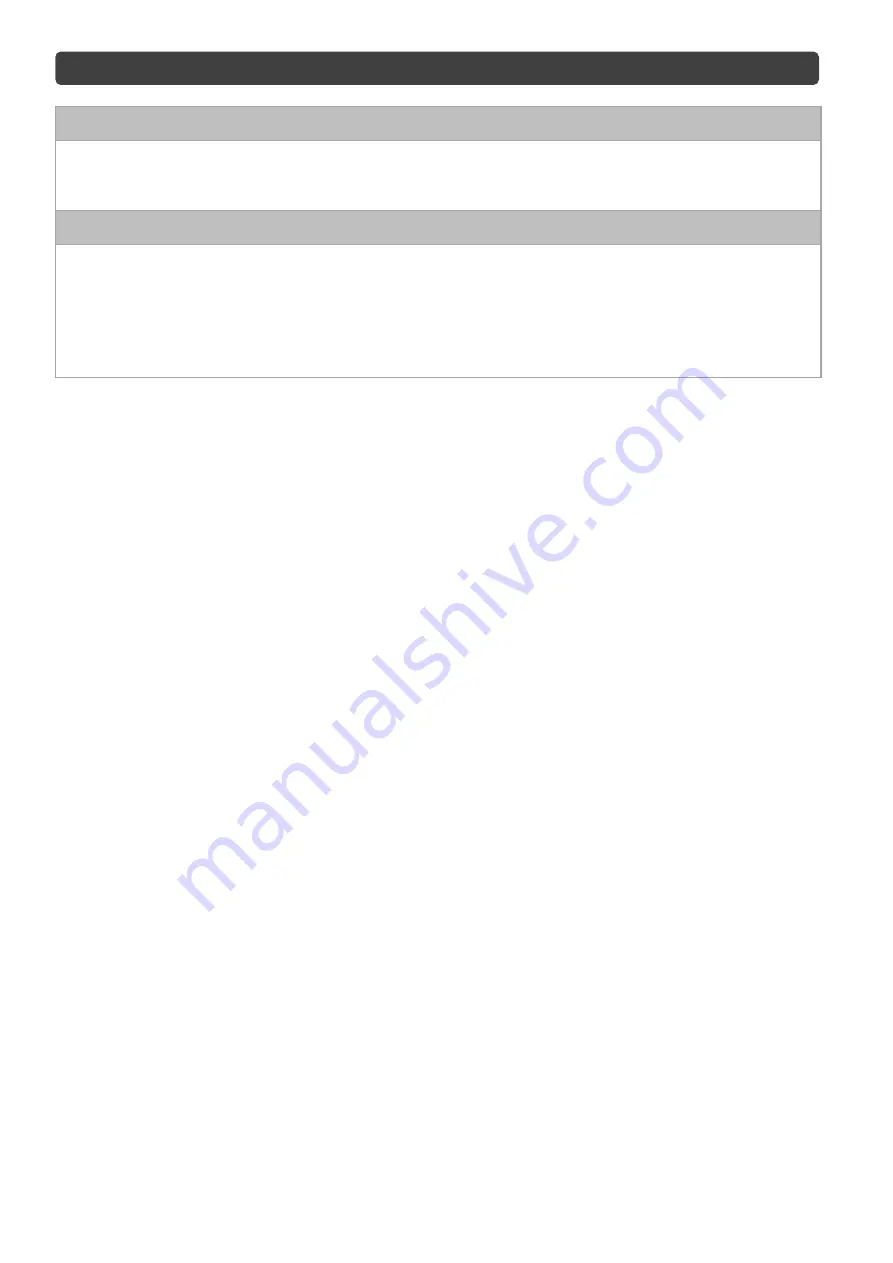
© Galvin Engineering Pty Ltd
Product Installation Guidelines
Version 1, 19 October 2022, Page
18
of
25
11.3
IMPORTANT NOTES ON DEBRIS
Although this product is protected by built-in filters, debris can still find its way to the thermostat housing area.
This can happen during servicing for example. Remove cartridge (See section 11.2 Removal And Inspection Of
Cartridge) and carry out an inspection.
11.4
MAINTENANCE CLEANING
On a regular basis the anti-splash nozzle should be inspected and cleaned if necessary. This should be done
immediately before sterilising is carried out.
In areas where lime scale build-up is prevalent this will have to be removed. An inhibited proprietary scale
solvent can be
used su h kett e des ng s vent, ut t s mp rt nt t f w the m nuf turer’s gu de nes
After descaling it is important to rinse the parts thoroughly in clean water. Clean carefully and do not use
abrasive materials or scrapers.