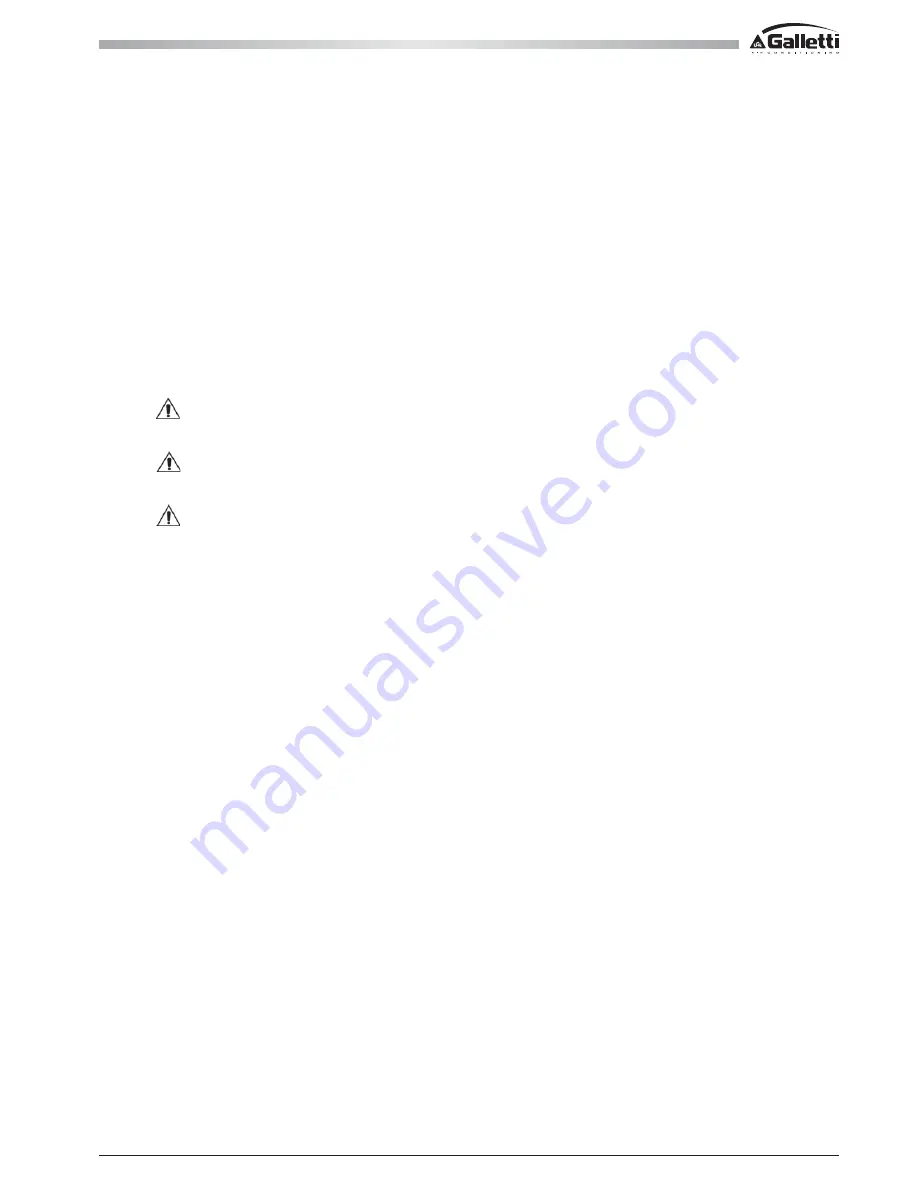
29
All copying, even partial, of this manual is strictly forbidden
RG66007169 - Rev 00
4 STARTING
UP
THE FIRST START UP MUST BE CARRIED OUT EXCLUSIVELY BY QUALIFIED PERSONNEL AND AUTHORIZED BY GALLETTI SPA (SEE WARRANTY
SHEET ATTACHED).
At first start-up of the installation make sure to comply with current national regulations.
4.1 PRELIMINARY
CHECKS
When starting up the unit for the first time or after a seasonal period of quiescence, it is advisable to have the following checks performed by specialised
personnel:
- Check that the electrical connections have been made properly and that all the terminals are securely tightened.
- Check that the external power supply is -5 % tolerance from the power supply reported on the unit identification label.
If the power supply is subject to frequent voltage fluctuations, contact Galletti S.p.A. for advice on choosing suitable protections.
- Check for refrigerant leaks, with the aid of a leak detector if necessary.
- Check that the plumbing connections have been properly made according to the indications given on the plates to be found on the unit itself
(water inlet, water outlet etc.).
- Make sure that the pump is not blocked.
- Make sure that the water circuit is duly bled to completely eliminate the presence of air: load the circuit gradually and open the air vent valves,
which the installer should have set in place.
Warning
before starting the unit, make sure all the covering panels are in place and secured with the fastening screws provided. To start the unit,
move the main switch to on. Use the keypad of the electronic control as directed in section 3.3 to select the cooling or heating mode.
Warning
You should not disconnect the unit from the power supply during periods when it is inoperative but only when it is to be taken out of
service for a prolonged period (e.g. at the end of the season). To turn off the unit temporarily follow the directions provided in section 3.3.
Warning
do not cut off power using the main switch:
the latter device serves to disconnect the unit from the electricity supply when there is no passage of current, i.e. when the unit is already turned OFF.