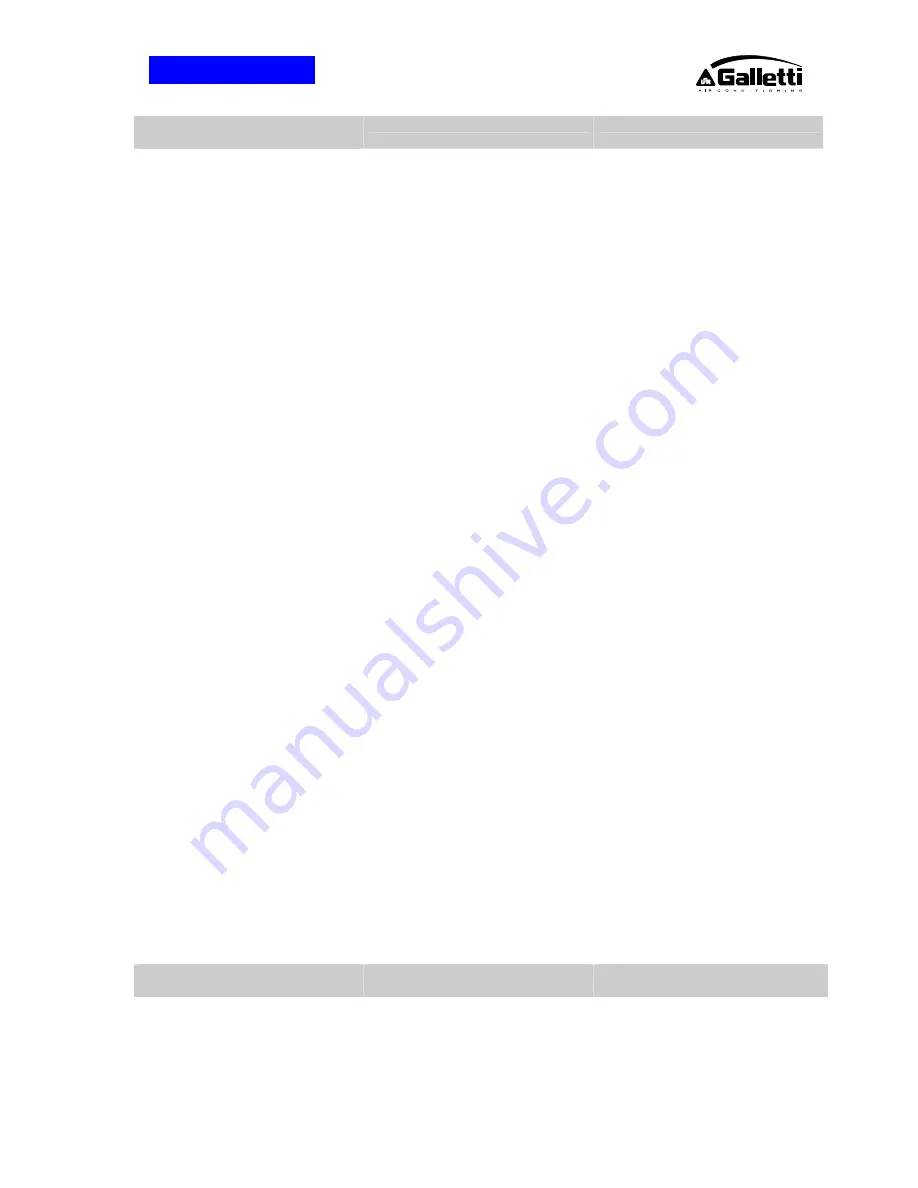
RG66001652_REV.02
37
LCW - LCR
FAULT
Possible causes
Corrective actions
Presence of abnormally high
pressure
Unit overcharged. as revealed by
an undercooling of more than 8 °C.
Drain the circuit
Thermostatic valve and/or filter
obstructed. These symptoms may
also occur in the presence of an
abnormally low pressure.
Check the temperatures upstream
and downstream from the valve
and filter and replace them if
necessary.
Insufficient flow of water in the
case of heat pump operation.
Check the water circuit for
pressure drops and/or whether the
pump is working properly [direction
of rotation]. Check the outgoing
water T and make sure it is less
than or equal to 50°C.
Low condensation pressure
Transducer
fault
Check the setting of the
condensation control device
[optional].
Water T too low
Install the condensation control
device.
Low evaporation pressure
Insufficient flow of water
Check whether the pumps are
rotating in the right direction. Check
the water system for pressure
drops.
Malfunctioning
of
thermostatic
valve
Warming the bulb with your hand,
check whether the valve opens and
adjust it if necessary. If it does not
respond, replace it.
Filter
clogged
Pressure drops upstream and
downstream from the filter should
not exceed 2°C. If they do, replace
the filter.
Low
condensation
T
Check the efficiency of the
condensation control device [where
present].
Low level of refrigerant
Check the refrigerant level by
measuring the degree of
undercooling; if it is below 2°C
replenish the charge.
The compressor does not start
The internal thermal protection
device has tripped
In the case of compressors
equipped with a protection module,
check the thermal contact. Identify
the causes after restarting.
The circuit breakers or line fuses
have been tripped by a short circuit
Pinpoint the cause by measuring
the resistance of the individual
windings and the insulation from the
casing before restoring power.
One of the high or low pressure
switches has tripped
Check on the microprocessor,
eliminate the causes.
The phases have been inverted in
the distribution compartment
Check the phase sequence relay,
then invert the phases upstream
from the main switch.
FAULT
Possible causes
Corrective actions
High evaporation pressure
Water T too high
Check the thermal load and/or
efficiency of the thermostat
function.
Check the efficiency of the
thermostatic valve