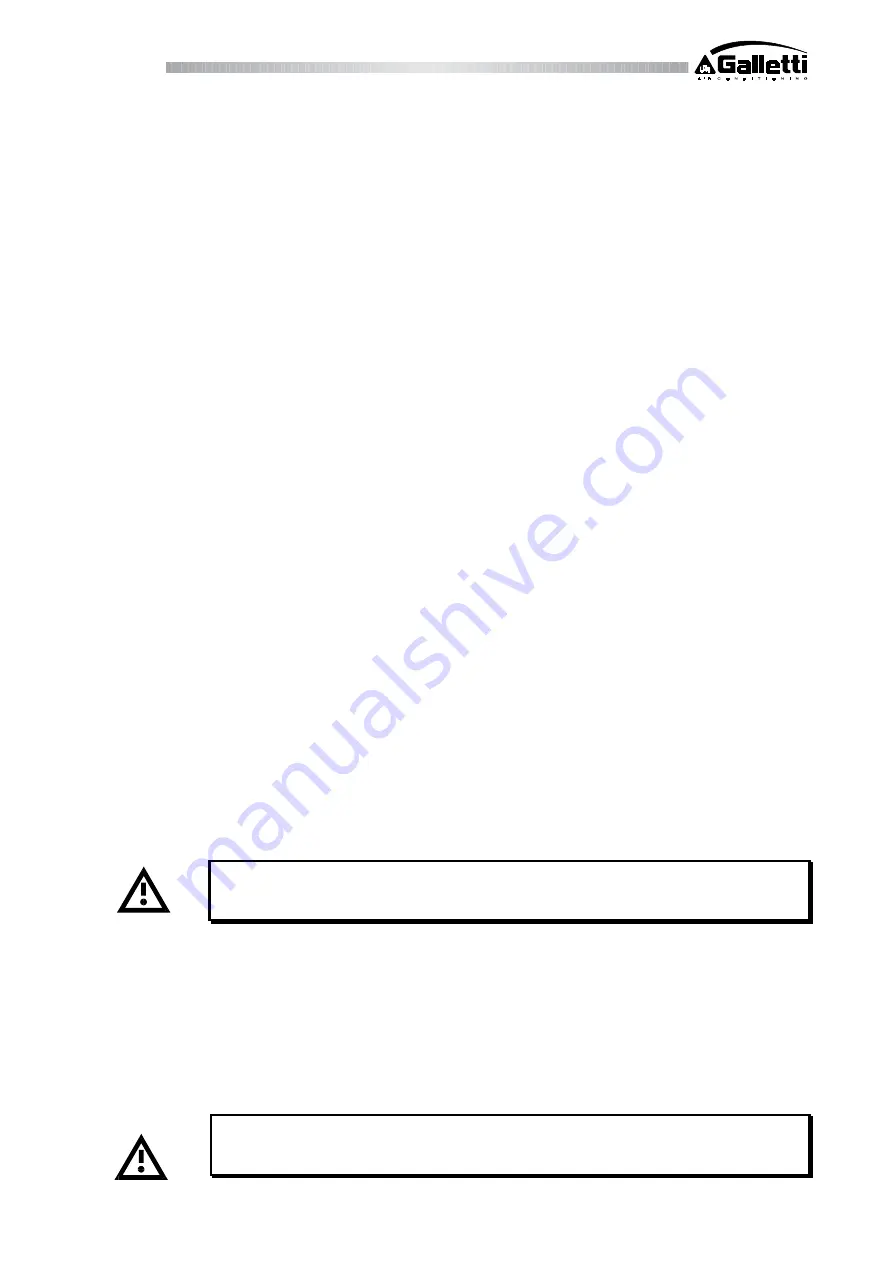
LCA
RG66000986 – Rev.00
9
GENERAL GUIDELINES FOR PLUMBING CONNECTIONS
When you are getting ready to set up the water circuit for the evaporator you should follow the
directions below and in any case make sure you comply with national or local regulations (use the
diagrams included in this manual as your reference).
- Connect the pipes to the chiller using flexible couplings to prevent the transmission of vibrations and
to compensate thermal expansions.
- It is recommended to install the following components on the pipes:
•
temperature and pressure indicators for routine maintenance and monitoring of the unit. Checking
the pressure on the water side will enable you to verify whether the expansion tank is working
efficiently and to promptly detect any water leaks within the equipment.
•
traps on incoming and outgoing pipes for temperature measurements, which can provide a direct
reading of the operating temperatures. Temperature readings can in any case be obtained from the
microprocessor installed on the unit.
•
regulating valves (gate valves) for isolating the unit from the water circuit.
•
metal mesh filter (incoming pipes), with a mesh not to exceed 1 mm, to protect the exchanger from
scale or impurities present in the pipes.
•
air vent valves, to be placed at the highest points of the water circuit for the purpose of bleeding
air. [The internal pipes of the unit are fitted with small air vent valves for bleeding the unit itself:
this operation may only be carried out when the unit is disconnected from the power
supply
]
•
drainage valve and, where necessary, a drainage tank for emptying out the equipment for
maintenance purposes or when the unit is taken out of service at the end of the season. [A 1”
drainage valve is provided on the optional water storage reservoir:
this operation may only be
carried out when the unit is disconnected from the power supply
]
WATER CONNECTION TO THE EVAPORATOR
It is of fundamental importance that the incoming water supply is hooked up to the
connection marked “Water Inlet”
Otherwise the evaporator would be exposed to the risk of freezing since the antifreeze thermostat would
not be able to perform its function; moreover the reverse cycle would not be respected in the cooling
mode, resulting in additional risks of malfunctioning
The dimensions and position of plumbing connections are shown in the dimension tables at the back of
the manual.
The water circuit must be set up in such a way as to guarantee that the nominal flow
rate of the water supplied to the evaporator remains constant (+/- 15%) in all operating
conditions.