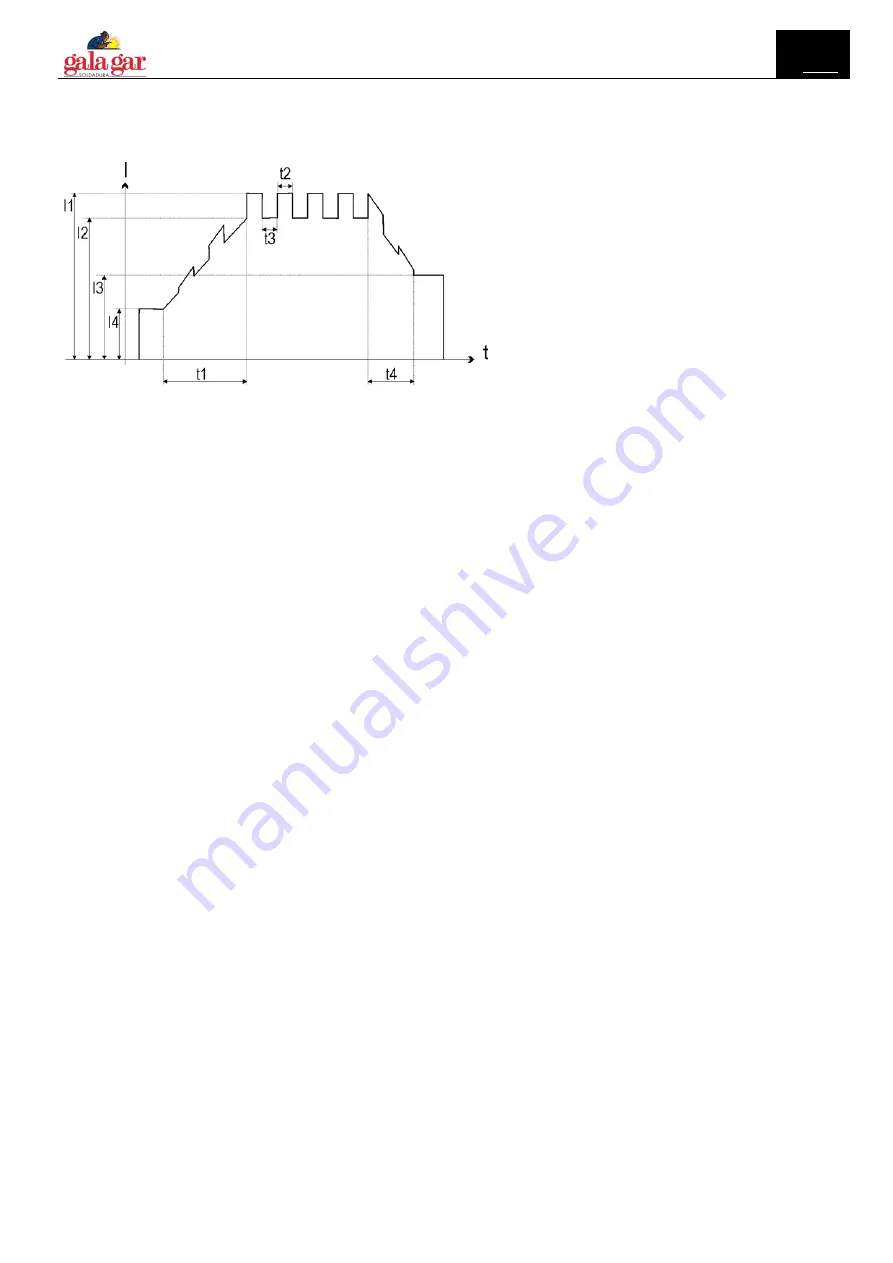
GALA ELECTRONICS 221ACDC
GALA ELECTRONICS 221ACDC
GALA ELECTRONICS 221ACDC
GALA ELECTRONICS 221ACDC
E
E
E
E
GB
GB
GB
GB
0
37
10
WELDING PARAMETERS
For a better understanding of the parameter functions described in the table, refer to the following diagram.
(I1) TIG WELDING CURRENT
(I2) BASE CURRENT
(I3) FINAL CURRENT
(I4) STARTING CURRENT
(t1) UP SLOPE TIME
(t2) PEAK TIME
(t3) BASE TIME
(t4) DOWN SLOPE TIME
(1/t2+t3) PULSED CURRENT FREQUENCY
Welding current
Output current value during welding.
Max welding current
Maximum output current value that can be achieved with remote
controller external reference.
Hot-start
This parameter aids electrode melting at the time of arc striking.
Consequences of a higher value:
−
Easier arc strike.
−
Increased spatter at welding start.
−
Increase of strike area.
Consequences of a lower value:
−
More difficult arc strike.
−
Less spatter at welding start.
−
Smaller strike area.
Arc-force
This parameter helps to avoid electrode sticking during welding.
Consequences of a higher value:
−
Fluidity during welding.
−
Welding arc stability.
−
Greater electrode fusion in workpiece.
−
More welding spatter.
Consequences of a lower value:
−
The arc is extinguished more easily.
−
Less welding spatter.
VRD
This parameter reduces the potential across the welding sockets
when welding is not in progress.
The arc strike procedure is as follows:
−
Touch the workpiece with the electrode tip.
−
Raise the electrode.
Power is released for several seconds.
−
Touch the workpiece with the electrode tip.
The welding arc will strike.
Long arc voltage
This parameter inhibits power output when the potential between
electrode and workpiece exceeds the preset threshold level.
Consequences of a higher value:
−
The welding arc persits even with a significant distance between
the electrode and the workspiece.
Consequences of a lower value:
−
Faster exit from weld.
Remote control
This parameter enables the unit to receive the current reference
signal from a remote control.
Dynamic arc
Welding power remains constant even when the distance between
electrode and workpiece changes.
Consequences of a higher value:
−
The welding arc concentration remains unchanged.
−
Prevents electrode sticking.
−
Thin workpieces may become deformed more easily.
Second current Bi-level
With a rapid press and release (less than 0.5 seconds) of the torch
trigger during welding, the output current value switches to the value
set by means of the “bi-level second current” parameter.
In DC TIG welding, the parameter is useful when welding different
gauge workpieces during the same pass; when moving between
different gauges the output current can be changed simply by
pressing the torch trigger.
In AC TIG welding the parameter is useful to change the heat output
during welding; when the workpiece heats up to the point at which
there is a risk of deformation, the current value (= heat) can be
reduced simply by pressing the torch trigger.
Base current
Pulsed wave minimum current.
Consequences of a higher value:
−
Faster creation of weld pool.