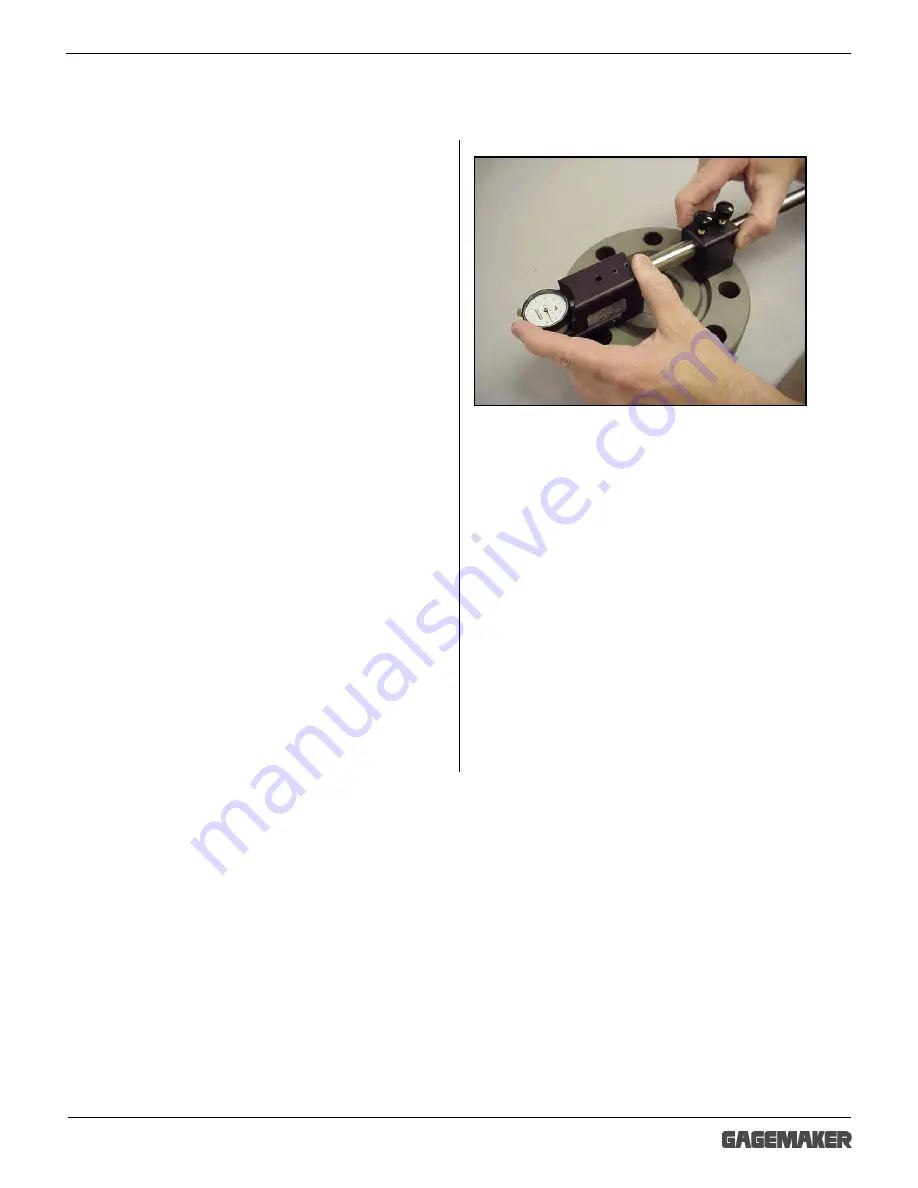
B
B
X
X
/
/
B
B
X
X
G
G
-
-
1
1
0
0
0
0
0
0
S
S
e
e
r
r
i
i
e
e
s
s
G
G
r
r
o
o
o
o
v
v
e
e
M
M
e
e
a
a
s
s
u
u
r
r
e
e
m
m
e
e
n
n
t
t
G
G
a
a
g
g
e
e
O
O
p
p
e
e
r
r
a
a
t
t
i
i
o
o
n
n
M
M
a
a
n
n
u
u
a
a
l
l
20
Inspecting Parts with the BX-1000 Gage (continued)
6. While maintaining pressure toward the lower
block and flange face, sweep the gage back
and forth, using the lower block as a pivot, to
locate the largest indicator reading.
Note:
Be sure that the small revolution counter on
the indicator is pointing to the same number
as when the gage was zeroed. Refer to the
number previously recorded on the side of
the gage.
7. Repeat the process in several locations around
the groove to get an average groove diameter.
8. Locate the groove diameter in the 6B & 6BX
Groove Inspection Tolerances table in this
manual to determine the groove width
tolerance.
9. Record the information on an inspection report.
10. Inspect the part with the BXG-1000 to ensure
the proper groove width.
11. Use the first part you inspected as a control
piece to verify repeatability. Mark the part at a
location where it was inspected and record the
deviation from zero.
12. During the inspection process, periodically
place the BX-1000 on the control piece to verify
the gage’s accuracy.