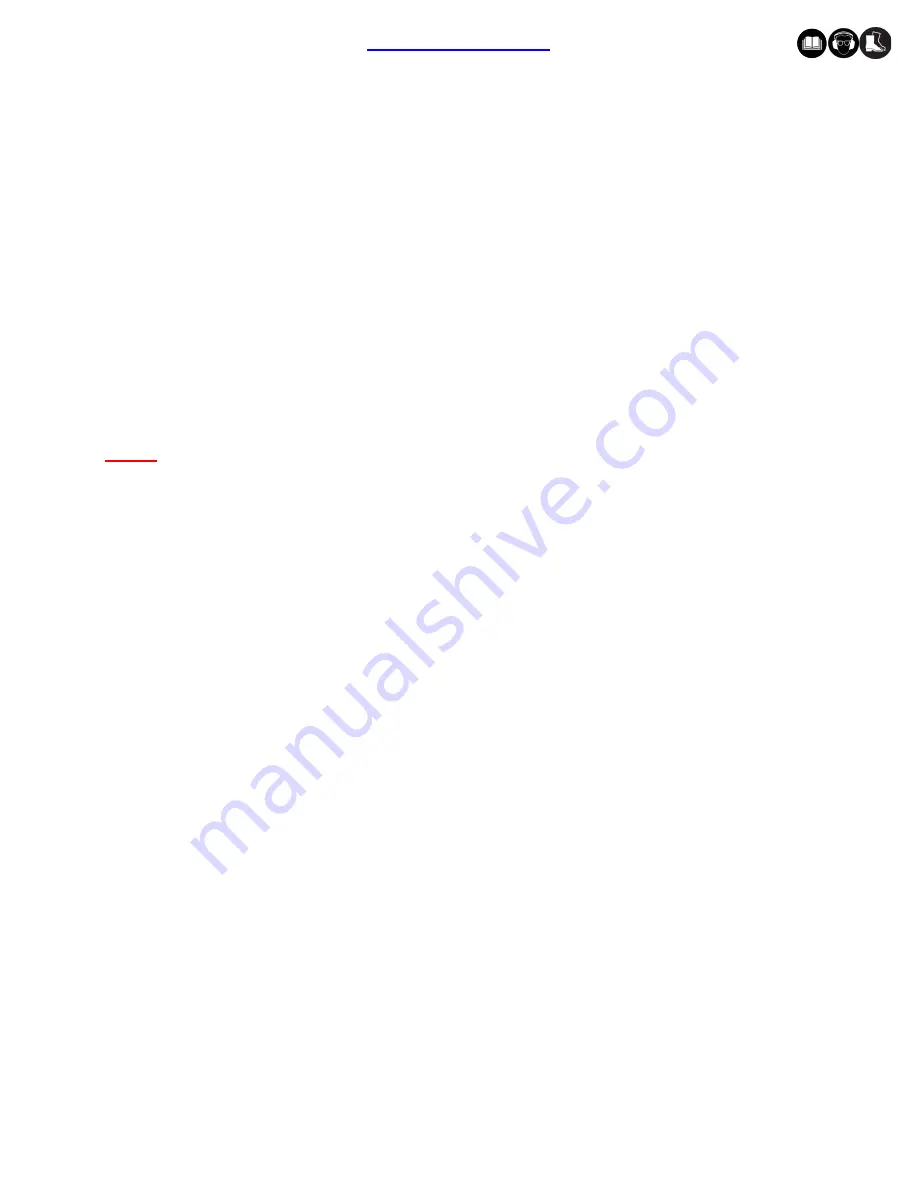
12
REV 3/23
GB743SHAVT
TROUBLESHOOTING
Providing all maintenance conditions have been met, follow this systematic approach to diagnosis.
1.
NO OPERATION WHEN LEVER (704345) IS DEPRESSED.
a.) Check powerunit power source.
b.) Faulty actuator assembly. Replace.
c.) Check hydraulic couplings; tighten, repair or replace.
2.
SLOW OR PARTIAL OPERATION WHEN LEVER (704345) IS DEPRESSED.
a.) Low hydraulic pressure. Check oil level.
b.) Polyseal (A
-
1135) or O
’
rings (400792) on the piston (743407) could be worn or damaged. Replace.
c.) Excessive wear or scoring on moving parts. Check and replace faulty parts.
3.
OIL LEAKAGE.
a)
DO NOT
OPERATE WITH OIL LEAKING FROM TOOL. HIGH PRESSURE OIL MAY CAUSE SEVERE PERSONAL INJURY.
b.) Hydraulic oil leaks from connections. Tighten threaded connections.
(See hydraulic thread preparation pg. 10).
c.) Oil leaks from tool. Determine source of leak and replace worn or defective o
’
rings and back
-
up rings.
4.
PINTAIL STRIPPED DURING PULL STROKE.
a.) Nose Assembly must be pushed onto fastener fully.
b.) Chips may have collected in chuck jaws. Disassemble nose assembly, clean jaws in mineral spirits or use a sharp pointed
object to remove chips. Re
-
lube surfaces jaws ride on.
c.) Chuck jaws may be worn or damaged. Replace.
d.) Pintail too short for jaws to properly grip. Select proper pintail length fastener.
e.) Excessive gap between sheets. Reduce gap before attempting to install fastener.
5.
PINTAIL IS NOT BEING VACCUMED THROUGH.
a.) Check the vacuum line is not kinked and that the bend radius is not too small.
b.) Check vacuum pressure using vacuum gage (703567) (sold separately).
Note: Offset nose assemblies must be check by removing the vacuum line from the nose assembly.
c.) Press gage against the vacuum line or nose assembly to create seal.
Optimum vacuum pressure at nose assembly must be between 15
-
22 inHg.
(381
-
558.8 mmHg).
6.
NOSE ASSEMBLY WON'T ACCEPT FASTENER PINTAIL.
a.) Check vacuum line is not kinked and that the bend radius is not too small.
b.) Spent fastener stem may be jammed in pulling head. Disassemble and check for worn or broken parts in nose assembly.
Replace defective parts and clean before reassembling.
c.) Verify Tool and Nose Assembly are correct for fastener.
d.) Spent fastener stem may be jammed in pulling head. Disassemble and check for worn or broken parts in nose assembly.
Replace defective parts, clean and re
-
lube jaws before reassembling.