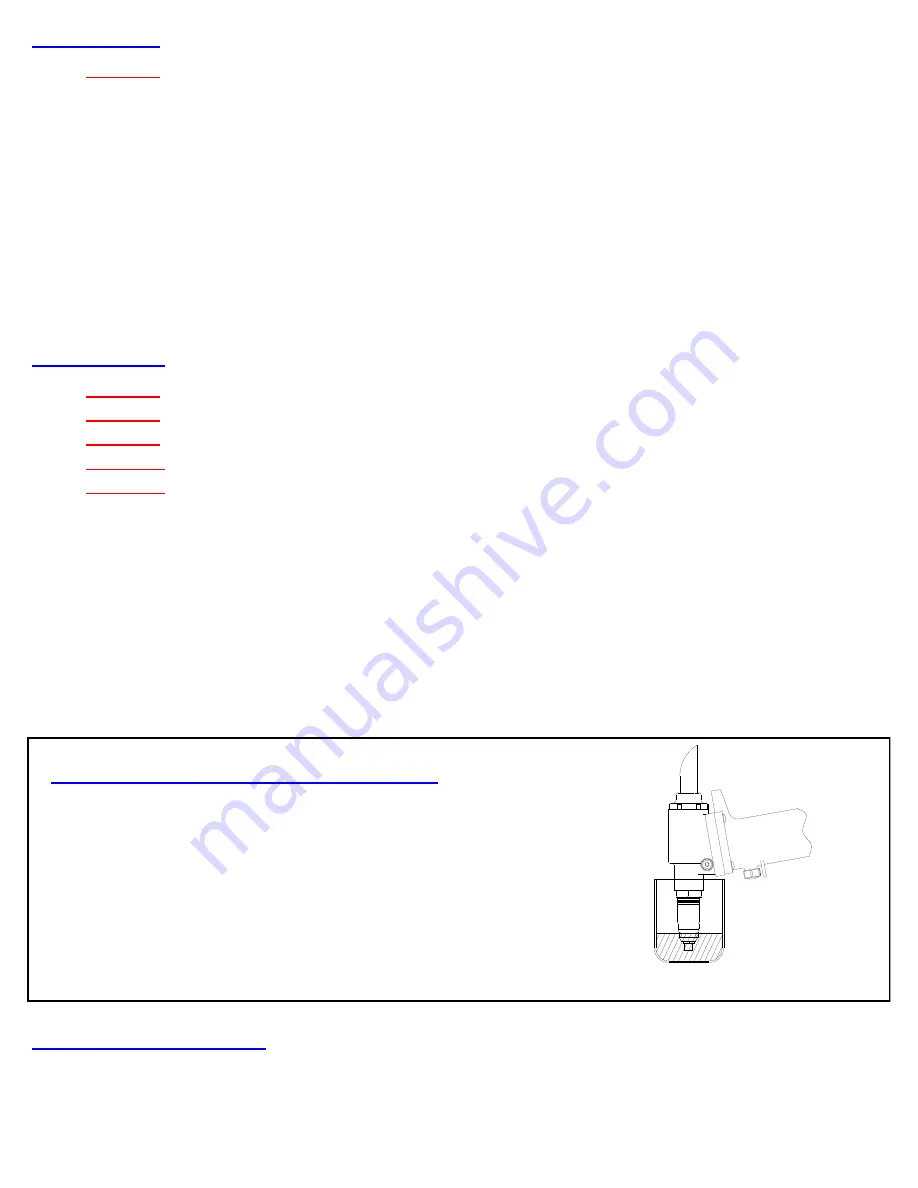
6
Rev. 2/15
S/N: 2317 AND ABOVE
PLEASE CONTACT GAGE BILT FOR ALL OTHER SERIAL NUMBERS.
DESCRIPTION
Covered under Patent No. 5,485,727
WARNING
:
The balance of this tool is designed for horizontal use and is not ergonomically best suited for all applications. Gage
Bilt will be pleased to advise for your specific application.
The GB730 is a pneumatic-hydraulic tool designed specifically for the efficient installation of a wide range of blind rivets and
lockbolts. It weighs 4.7 lbs. (2.1 kg) and can be operated in any position with one hand. It has a .500" (12.7 mm) rivet setting stroke
and a rated pull load of 4,000 lbs. (17.8 kN) with 90 psi (6.2 bar) air pressure at the air inlet.
The GB730 riveter operates on a wide range of air pressure, with 90 to 100 psi (6.2-6.9 bar) providing the maximum efficiency. At 90
psi (6.2 bar) air pressure, the GB730 does not exceed 81.5 dB (A) and consumes 3.9 cfm at 20 cycles per minute.
The air inlet is provided with 1/4-18 female pipe threads for accepting the user's air hose fitting.
Nose Assemblies that were designed for the Model 352 Installation Tool mount directly on the GB730 without the use of an adapter.
NOSE ASSEMBLIES ARE NOT FURNISHED WITH THIS TOOL AND MUST BE ORDERED SEPARATELY (SEE PAGE 13).
MAINTENANCE
WARNING:
Maintenance personnel
MUST
read and understand all warnings and cautions.
WARNING
:
Disconnect tool from its power source before performing maintenance.
WARNING
:
Excessive contact with hydraulic oil and lubricants should be avoided.
WARNING:
Dispose of hydraulic oil in accordance with all environmental regulations applicable in your area.
WARNING:
Read MSDS documents for all applicable materials.
The performance of any tool depends upon good maintenance practices. Following these minimal requirements for service and care
will extend the life of your tool.
*Only use an air supply set at 90-100 psi. (6.2-6.9 bar) equipped with a filter-regulator to prevent wear.
*The tool will eventually lose some hydraulic oil. Keep the hydraulic system full (only use Dexron III, or equivalent) and free of air by
using the fill bottle assy (745163) on a weekly basis.
*Proper care by operator is necessary in maintaining full productivity and reducing downtime. Read all applicable tool manuals
and nose assembly data sheets prior to operating tools.
*Keep nose assemblies, especially jaws, clean and free of chips and debris. Lube jaws and collet surfaces that jaws ride on with
light machine oil on a daily basis.
*All Screwed End Caps, Base Covers, Air Fittings, Air Actuators, Screws and Nose Assemblies are to be examined at the end of
each working shift to check that they are secure.
*Check tool, all hoses and all couplings daily for damage or air/hydraulic leaks. Tighten or replace (if necessary).
*For a complete overhaul, tool kit (GB730TK) is recommended (see page 9).
TORQUE SPECIFICATIONS
Button Head Cap Screws (A-928) = 40 inch lbs.
Packing Plug (704118) = 45 foot lbs.
Flexlock Nut (400559) = 40 inch lbs.
End Cap (730717) = 45 foot lbs.
Button Head Cap Screws (402482) = 35-40 inch lbs.
(Do NOT over
-
tighten)
CLEANING AND LUBRICATING PROCEDURE
Daily cleaning and lubrication of nose assembly will greatly reduce downtime and
increase life of components. Using sewing machine oil, or an equivalent cleaner/
lubricant, follow instructions below.
1. Disconnect tool vacuum line (if equipped).
2. Point nose assembly into oil as shown (Fig. A).
3. Cycle tool 8-10 times and wipe dry.
Fig A.
Image may not
reflect actual tool