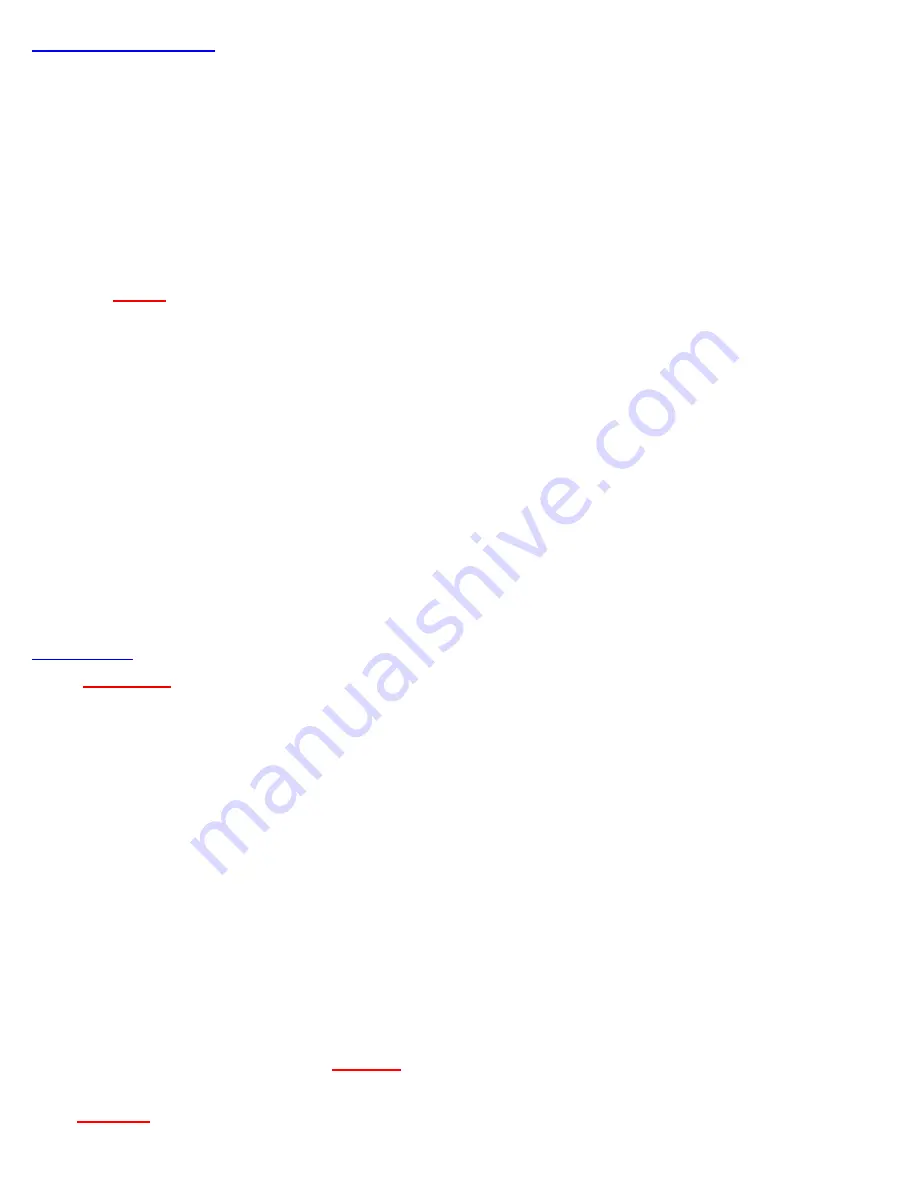
5
7/11 REV 3/14
TROUBLESHOOTING
Providing all maintenance conditions have been met, follow this systematic approach to diagnosis.
1. NO OPERATION WHEN ACTUATOR LEVER ASSEMBLY IS DEPRESSED
a.) Check powerunit power source.
b.) Faulty actuator assembly. Replace.
c.) Check hydraulic couplings; tighten, repair or replace.
2. SLOW OR PARTIAL OPERATION WHEN ACTUATOR LEVER ASSEMBLY DEPRESSED
a.) Low hydraulic pressure. Check fluid level.
b.)
Polyseal (A-1119) and o’ring (400793) could be worn or damaged. Replace.
c.) Excessive wear or scoring on moving parts. Check and replace faulty parts.
*See Overhaul
3. OIL LEAKAGE
a)
DO NOT
OPERATE WITH OIL LEAKING FROM TOOL. HIGH PRESSURE OIL MAY CAUSE SEVERE PERSONAL INJURY.
b.) Hydraulic oil leaks from connections. Tighten threaded connections.
c.) Oil leaks from tool. Determine source of leak and replace worn or defective o’rings and back-up rings.
4. PINTAIL GROOVES STRIPPED DURING PULL STROKE
a.) Nose Assembly must be pushed onto fastener fully.
b.) Chips may have collected in chuck jaws. Disassemble nose assembly, clean jaws in mineral spirits or use a
sharp pointed object to remove chips. Re-lube surfaces jaws ride on.
c.) Chuck jaws may be worn or damaged. Replace.
d.) Pintail too short for jaws to properly grip. Select proper grip length fastener.
e.) Excessive gap between sheets. Reduce gap before attempting to install fastener.
5. NOSE ASSEMBLY WON'T ACCEPT FASTENER PINTAIL
a.) Spent fastener stem may be jammed in pulling head. Disassemble and check for worn or broken parts in
nose assembly. Replace defective parts, clean and re-lube jaws before reassembling.
6. FASTENER STEM JAMMED IN NOSE ASSEMBLY
a) Nose assembly components require service.
DISCONNECT AIR FROM TOOL
, remove the nose from the tool and
disassemble. Replace worn or broken parts. Clean the surface the jaws ride on.
b) Stems lodged side by side in the follower. Disassemble, remove stems, and reassemble.
c) Incorrect follower.
OVERHAUL
WARNING:
DISPOSE OF HYDRAULIC FLUID IN ACCORDANCE WITH ALL ENVIRONMENTAL LAWS AND REGULATIONS
APPLICABLE TO YOUR AREA.
Service Kit 713138 contains a complete set of o’rings, back-up rings and screws to facilitate overhaul
Perform overhaul in a clean, well lit area using care not to scratch or nick any smooth surface that comes in contact
with an o’ring. Use of Lubriplate® (Gage Bilt part no. 402723) or other lubricant is recommended during reassembly to
prevent tearing or distorting of o’rings. Use extreme care during disassembly and re-assembly not to damage, mar or
nick any smooth surface that comes in contact with seals.
Disconnect hydraulic hose and air line from powerunit.
Remove complete nose assembly and extensions from tool. Remove socket head cap screws (400061) separating han-
dle (700324) from head cylinder ass’y (713123). Replace o’ring (S832) and gasket (704129). Remove end cap (713217).
Carefully push piston (713211) out of head cylinder ass’y (713123). Using a small blunt object, remove polyseal
(A-1119) and o’ring (400793) from piston (713211), remove o’rings (S834) and back-up ring (401089) from inside head
cylinder assembly (713123) and remove o’rings (400808) and (400824) from end cap.
Clean parts in mineral spirits or other o’ring compatible solvent being sure to clean o’ring grooves. Inspect compo-
nents for scoring, excessive wear or damage.
Reassembly sequence is opposite of disassembly. Be sure relative positions of polyseal, o’rings and back-up rings are
as shown in exploded view and parts list. Coat hose fitting threads with a non-hardening Loctite® 30534 or similar Tef-
lon® infused Pipe Dope is recommended.
CAUTION
Teflon tape is an excellent thread sealer, however, if it is not
properly applied, pieces of Teflon may enter the hydraulic system and cause malfunction or damage. Use 1 1/2 wraps
of tape on each thread. Cut off all loose tape ends. Tighten until fitting feels snug and then go 1/2 to a full turn past that
point.
CAUTION:
Over tightening can easily distort the threads.